在 CAD 中进行设计时,您是否依赖于测试按面值构建的数字模型?然后预计组件组装和成品在实际条件下的行为会出现问题
材料准备者:AQT 中心科学主任 谢尔盖·格里戈里耶夫
免费获取文章不会以任何方式降低其中所含材料的价值。
分析生产过程的变化将有助于减少负面影响 不可避免的变化 产品的尺寸质量、成本和上市时间。
以下是数字模型本身普遍存在次优化的证据,没有考虑数字模型应该服务的目标。
我们的团队在俄罗斯一家研究和生产公司的一次会议上发表了一份报告,内容涉及需要了解实际生产过程在产品设计和生产中关键质量指标的可变性方面的能力。
该报告的其中一个章节专门讨论了设计产品的质量问题,而没有了解我们自己和供应商的实际生产过程的统计状态和能力。特别是,该企业之一的副总设计师(ZGK)表示,建设新的数据中心(数据存储和处理中心)将减少全面测试。
我们对ZGK声明的态度:只要您不知道真实过程的可能性,我们建议您警惕此类声明。即使是全尺寸的原型(prototype)也不是系列产品。
“原型测试不充分。
样机单一,参数人为接近标称参数。如果不了解变化,就无法预测变化。”
当您考虑用数字模型测试取代全面测试时,您必须了解您愿意忽略什么以及忽略多少。简而言之,您必须了解数字模型的测试结果与实验模型的全面测试有多大不同,与系列产品更是如此。假设您愿意忽略的因素的影响微不足道,您必须了解,考虑到其固有的可变性,这些因素和未考虑的(被忽略的、未区分的和/或数字上不可估量的)因素的结果可以显着地从从测试目的的角度来看,超出了您的假设。你认为这不是真的吗?你怎么会知道这事?你有什么数据可以得出这样的结论?
让我举一个举世闻名的例子。
第二次世界大战期间,美国和英国空军司令部指派亚伯拉罕·沃尔德(Abraham Wald)参与美国统计研究小组(SRG)的秘密项目,找出飞机机身的哪些部分需要额外的保护。盔甲。军方建议在空战中遭受最严重影响的飞机部件上安装额外的保护装置。沃尔德研究了从战斗任务中返回的飞机,记录了被击中的位置。因此,他建议在孔数量最少的区域(机身中部和后部)安装额外的保护装置。该建议基于这样的结论:有必要防止沃尔德没有看到的袭击——接收袭击的飞机根本没有返回。随后,基于仅分析已知数据而做出的决策被称为“幸存者偏差”。
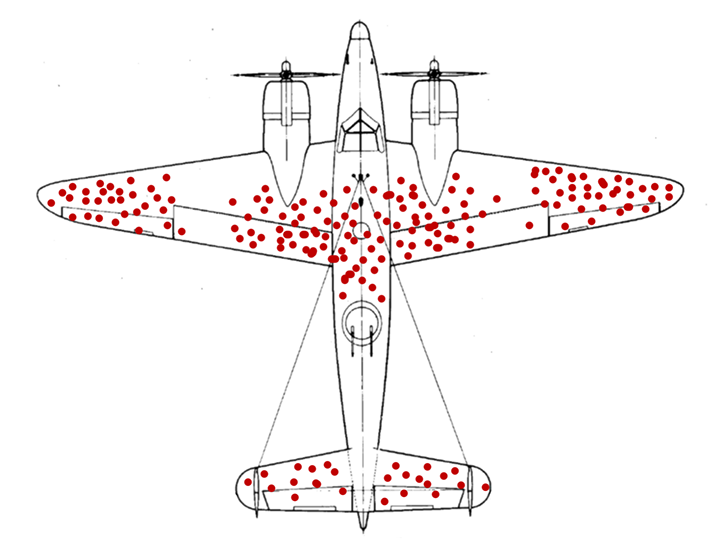
图 1. 亚伯拉罕·沃尔德。幸存者偏差。一架带有红点的飞机代表返航的美国飞机上的弹孔统计数据。
如果您希望随后将数字模型的结果与真实原型的测试进行比较,那么您计划为此生产和测试多少原型:1; 5; 8; 25?这些原型会相同吗?你怎么会知道这事?要声称原型的同质性,您必须有证据证明您自己的制造过程以及参与原型生产的供应商的制造过程具有统计可控性。您能否演示休哈特对这些过程的所有关键参数的控制图?
我们声明的解释
计算机辅助设计系统 (CAD) 中的设计以名义术语(数字模型)进行,而不是在硬件中发生的情况。设计人员必须使用有关现实世界制造流程固有可变性的数据来决定必要时对设计、材料、技术、公差的更改,或要求制造部门和供应商在实际原型开始生产之前改进流程和技术。
我们仔细研究了该公司一家重点制造企业的公开企业刊物。在出版物中,该公司的员工充分详细地报告了他们在生产中遇到的问题。
特别是,装配车间的工艺工程师报告说:
“技术人员必须寻找装配过程中出现的问题的最佳解决方案,因此他被迫对当前情况做出快速反应。考虑到可能会出现一些紧急情况,他必须赶时间,一切都跟上。这是装配车间工艺工程师的正常工作节奏。”
这位技术专家在组装产品时已经习惯了不断发生的紧急情况,他自己也认为这是正常的。从而确认装配过程中问题的持续性(稳定性)。稳定是系统性问题的标志。处理系统性问题是管理层的责任,而不是技术人员的责任。
铁匠说道:
“当铁匠在锻造中加热工件时,他会通过视觉确定温度并感觉金属是否已准备好进行锻造。加热时,碳和其他合金元素会燃烧出来,因此不要过热很重要。例如,初学者可以通过四次加热将金属制成所需的形状;一个有经验的铁匠只需要两个”。
设计师是否考虑到了生产过程的这种不确定性?有谁知道不同铁匠在不同条件下无限量加热到“肉眼”确定的温度后会得到什么样的合金?在这种情况下,数字模型强度的自动计算是否有助于预测实际产品的机械性能,例如耐腐蚀性?!
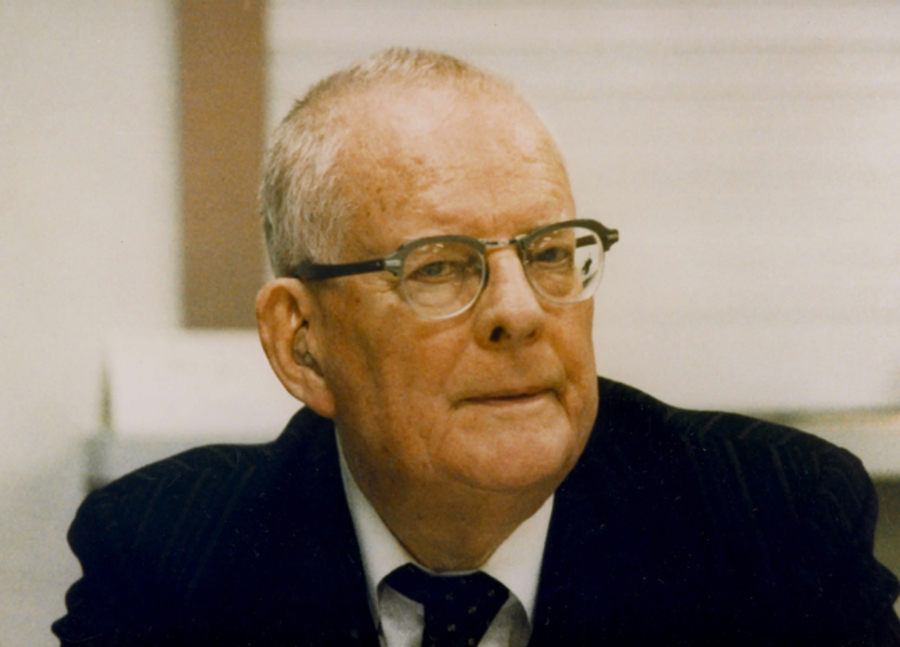
“实践比纯科学更精确,比训练更精确。休哈特认为,制造业和服务业所需的知识和技能标准比纯科学更严格。”
上面爱德华兹·戴明的引言部分解释了当前的情况:俄罗斯科学自信地经受住了国际层面的竞争,而俄罗斯工业在许多领域都在失败。
我们还举了其他例子来说明企业管理层对其质量责任缺乏认识,我不在本文中发表。
我希望现在越来越清楚,由具有标称公差的零件和符合设计过程中规定的要求的合金制成的数字模型与真实原型有何不同。如果我们谈论的是系列产品,那么这些差异会更大。由于设计、生产、供应以及与供应商合作等部门之间存在壁垒,拒绝对数百甚至数千个零部件的产品进行全面测试将导致巨大的损失,而其真正原因永远不会被了解。该公司的管理。
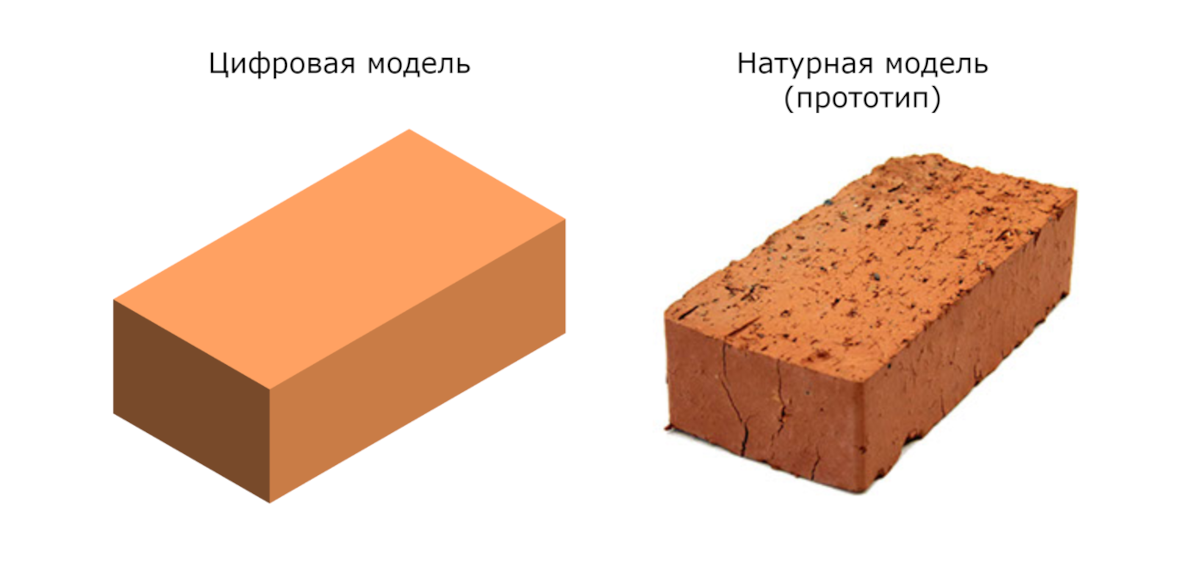
图 2. 数字模型与自然模型。
接下来,我们邀请与会人员考虑间隙配合中轴和孔的公差域的最简单二维配对的方案。真实零件的几何尺寸的可变性是数字模型与全尺寸模型的最小区别。
下面是轴和孔公差域配对的条件显示。设计师将在 CAD 中按标准创建零件。在最好的情况下(在最先进的俄罗斯公司中),将检查数字模型的相互作用零件的公差范围的组合以及是否符合由于其相互作用而获得的相关公差范围。
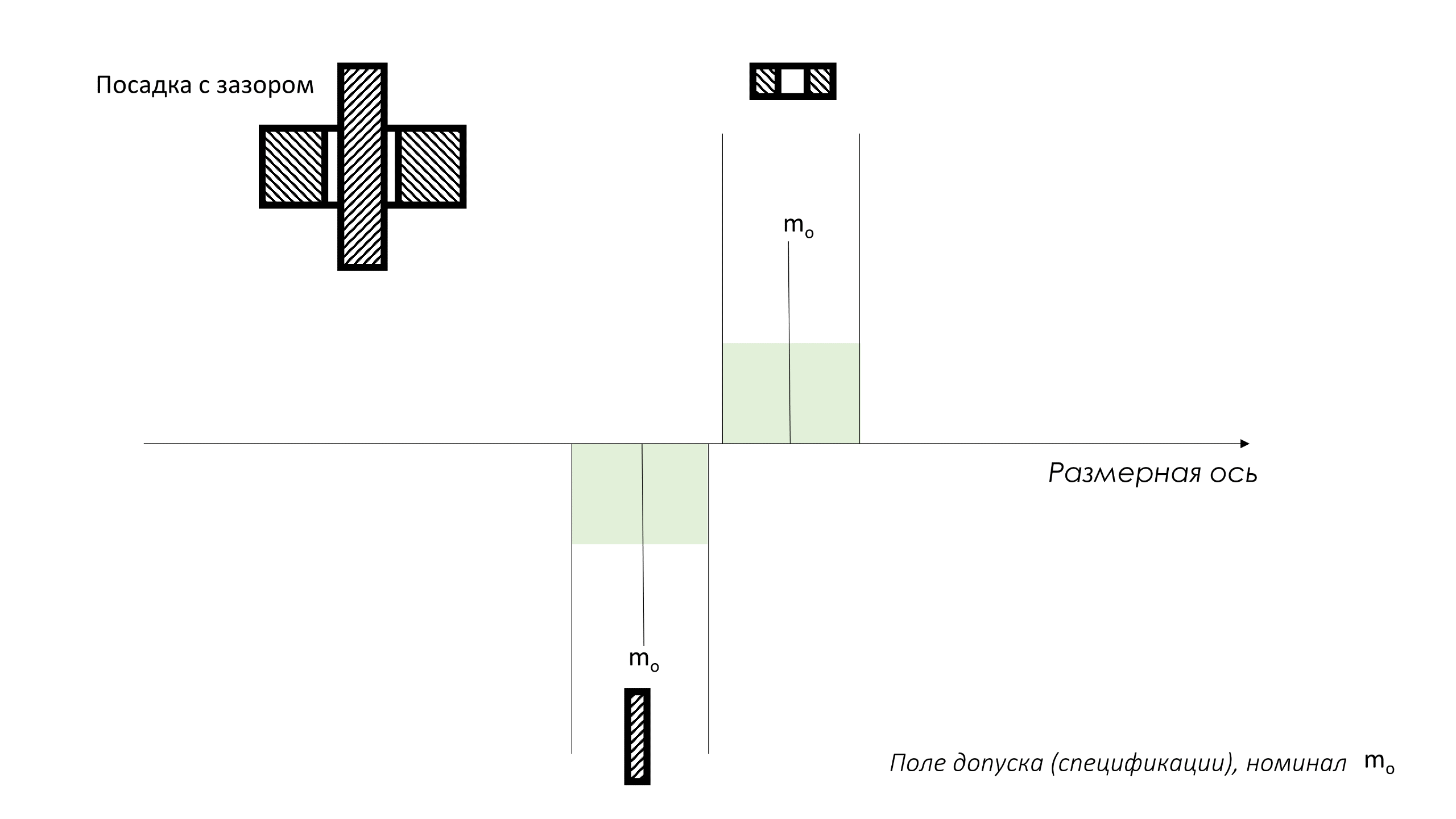
图 3. 轴和孔公差域配对的条件显示(间隙配合)。
在这种情况下,生产零件的理想制造工艺应与各个测量的分布密度相对应(任意选择对称钟形曲线),如下图 4 所示:稳定、完全居中且分布为个别数值在公差区内有一定的自由空间。在这种情况下,预先知道所有部件都 100% 合适。对零件进行罕见的控制抽样就足够了,以确认过程的稳定状态并控制将这些过程的分布的平均值(中心线)调整到标称公差范围。
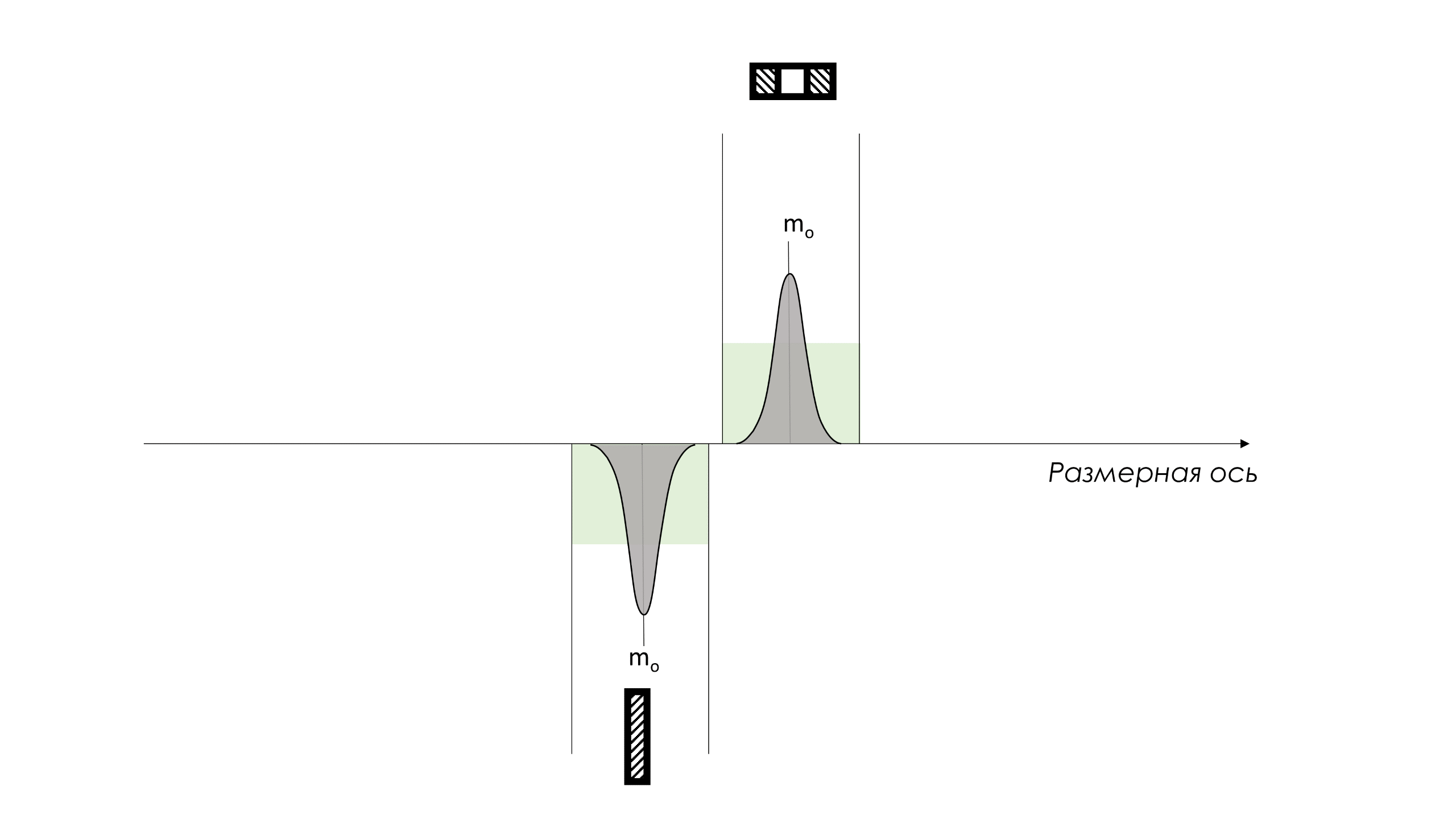
图 4. 稳定且完全居中的生产过程,各个值分布在具有一些自由空间的公差区内。
现在考虑下图中的选项,当生产过程处于统计控制(稳定)状态时,它们的散布 6σ 小于公差域的宽度(例如,Cp≥1.33),但它们并不居中。那么,一些产品就会超出公差范围并出现缺陷。从表面上看,不会有任何细节。必须将所有生产的零件分为符合公差带的零件和不符合公差带的零件,进行100%的控制,这是昂贵且低效的。在这种情况下,预先知道几乎一半的零件将不符合公差范围。参见公式说明 重现性指数 Cp 和 Cpk 的计算 。
重现性指数计算公式:Cp=公差范围/6σ
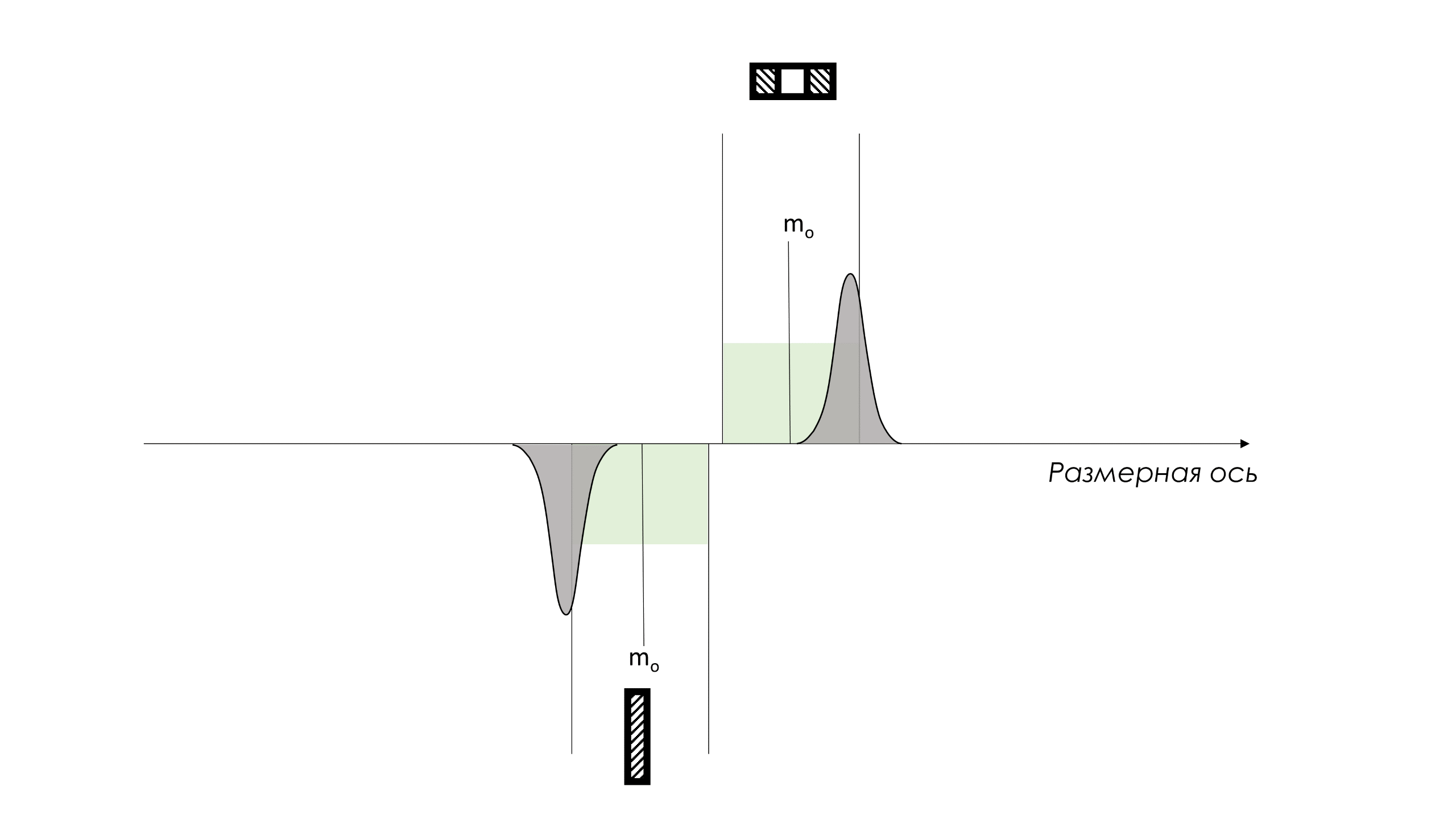
图5. 生产过程处于统计控制(稳定)状态,其散布6σ小于公差域的宽度(例如,Cp≥1.33),但不居中。
接下来,考虑当生产过程处于统计控制状态时的选项(参见下图6),它们的散布6σ大于公差域的宽度(例如,Cp<1.00),并且它们完全居中(例如,Cpk≈Cp)。那么,部分制造出来的产品又会超出公差范围。所有生产出来的零件都要分为符合公差带的和不符合公差带的,进行100%的控制。在这种情况下,预先知道某些零件将不符合公差。
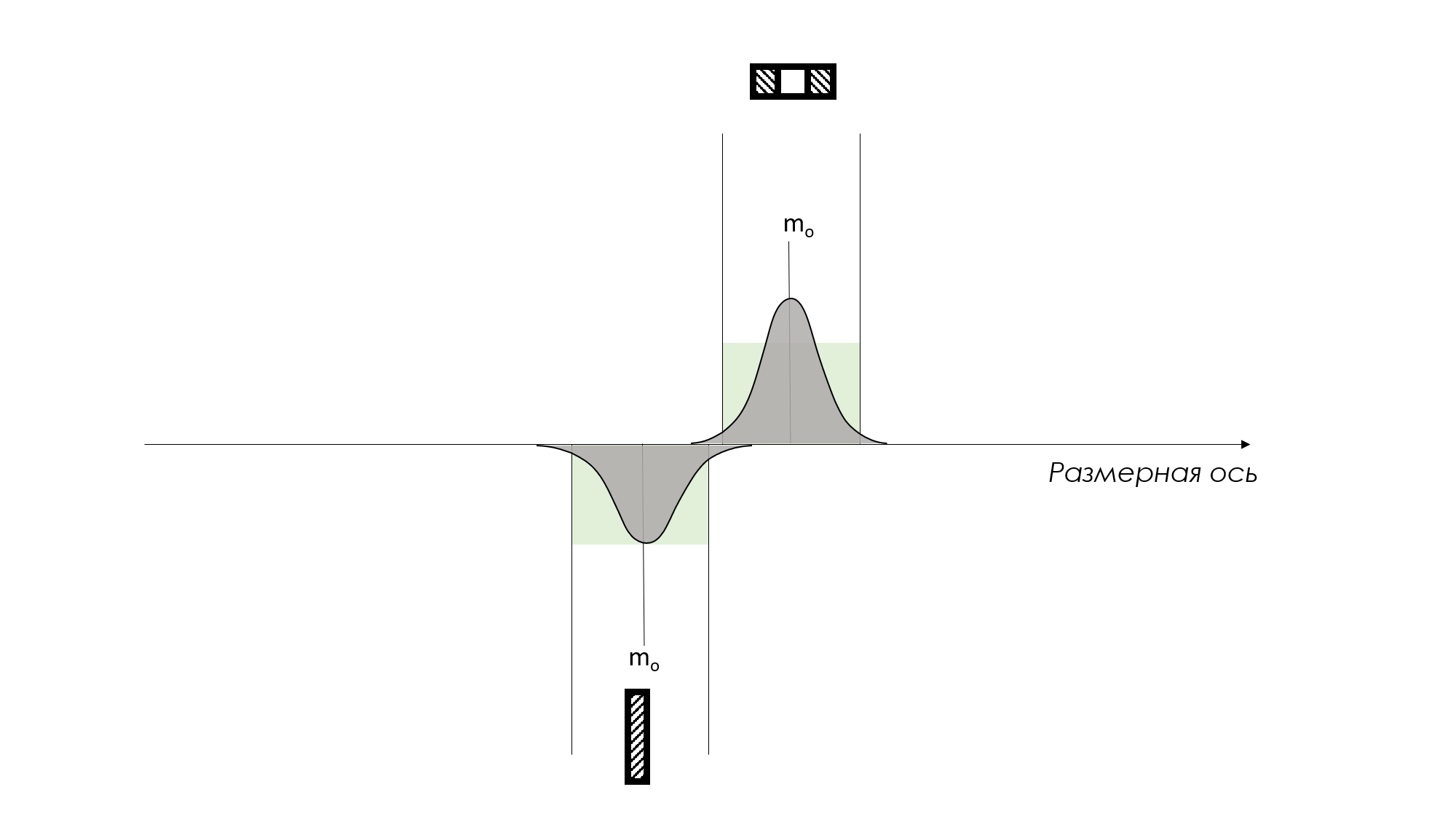
图 6. 制造过程处于统计控制(稳定)状态,其分布 6σ 大于公差域的宽度(例如,Cp<1.00),并且它们完全居中(例如,Cpk≈Cp)。
接下来,考虑当生产过程处于统计控制状态时的选项(参见下图7),它们的散布6σ大于公差域的宽度(例如,Cp<1.00),并且它们不居中(Cpk< cp)。那么,更多的产品将超出公差范围。后果是显而易见的。所有生产出来的零件都要分为符合公差带的和不符合公差带的,进行100%的控制。在这种情况下,事先就知道有一半以上的零件是不合适的。
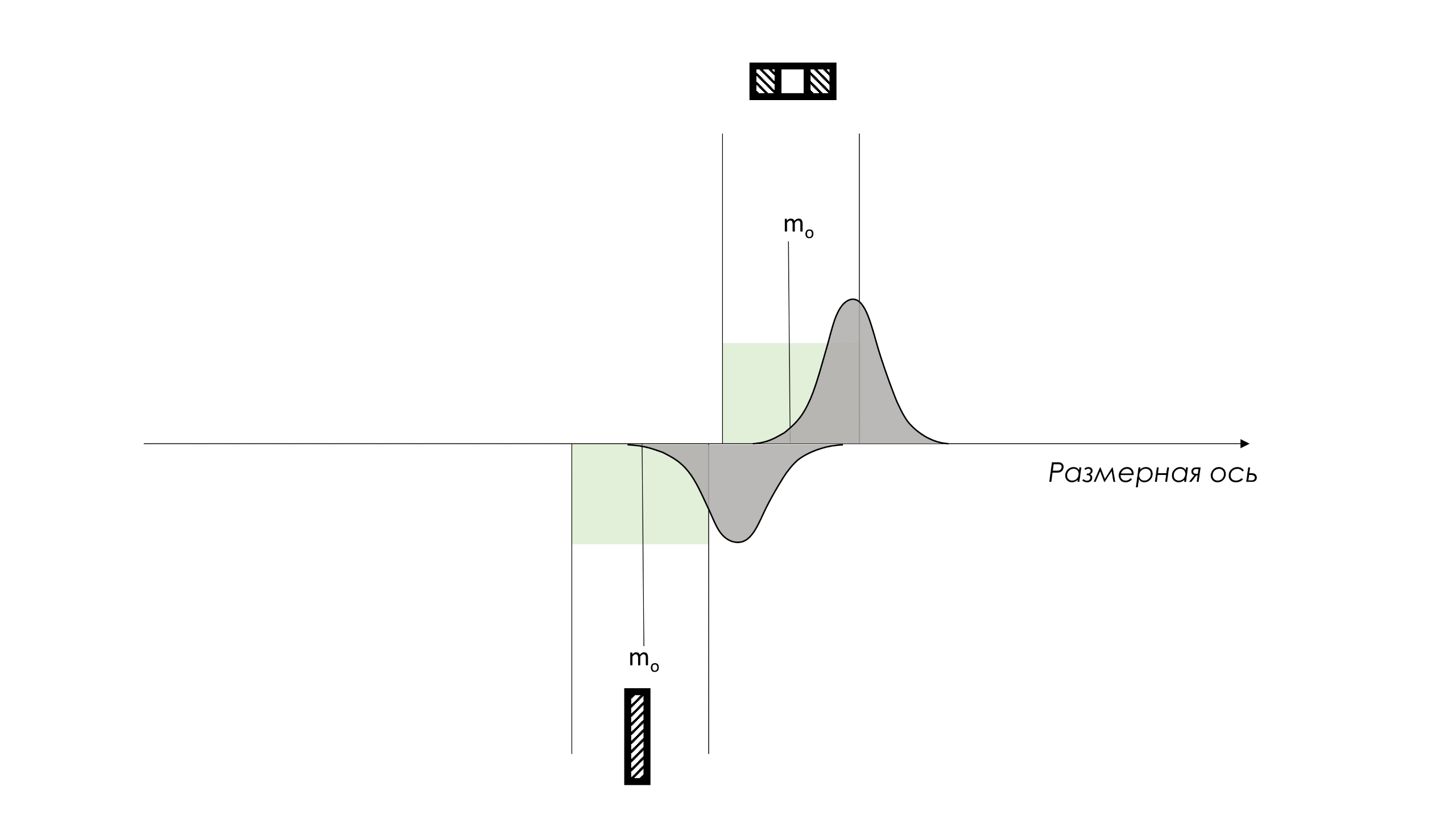
图 7. 生产过程处于统计控制(稳定)状态,其散布 6σ 大于公差域的宽度(例如,Cp<1.00),并且不居中(Cpk<Cp)。
下面的图 8 是与上面图 7 所描述的条件相匹配的另一个选项。同样,后果是显而易见的。所有生产出来的零件都要分为符合公差带的和不符合公差带的,进行100%的控制。在这种情况下,事先就知道有一半以上的零件是不合适的。
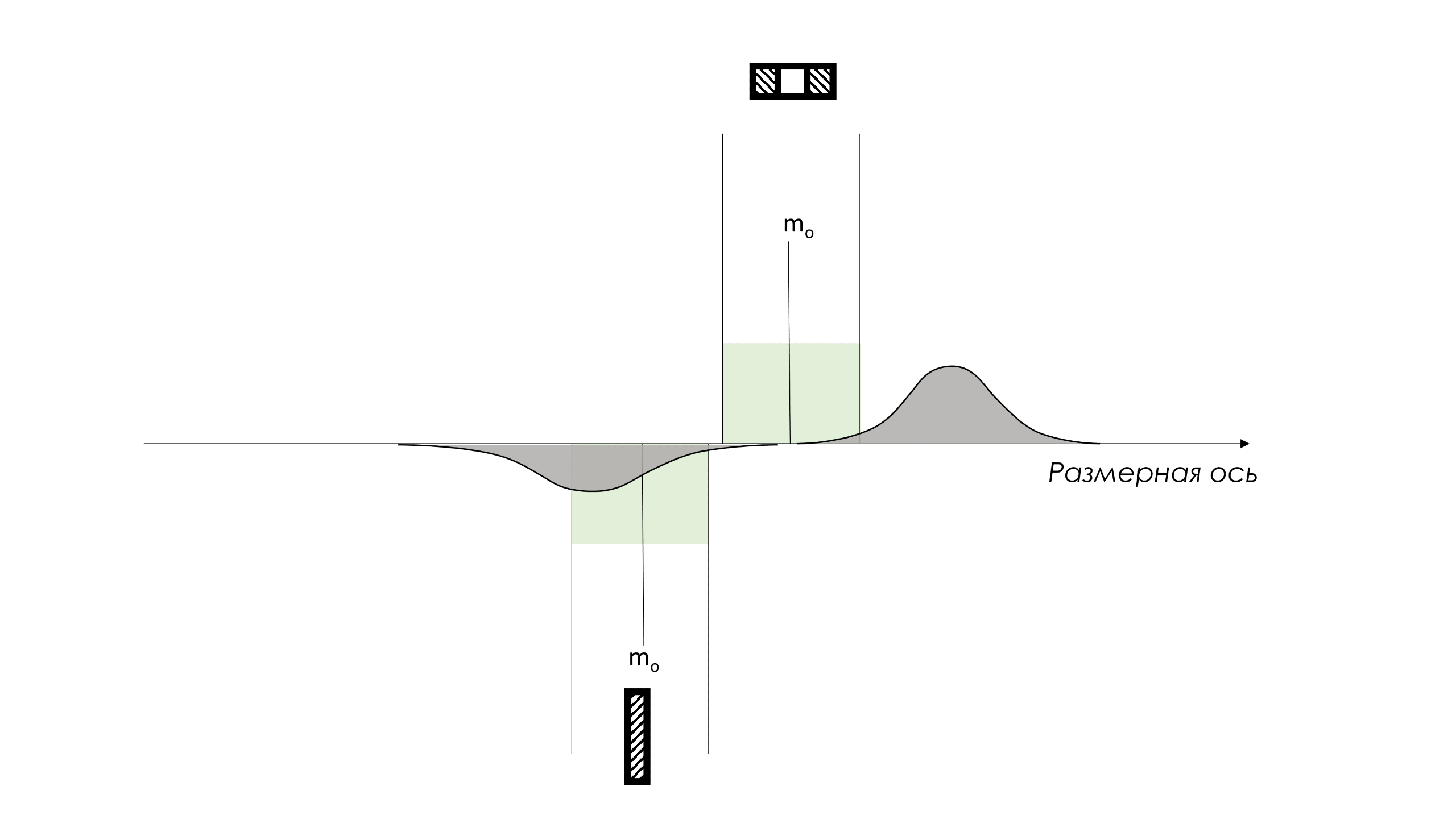
图 8. 图 7 中的选项的特殊情况。生产过程处于统计控制(稳定)状态,其分布 6σ 大于公差域的宽度(例如,Cp<1.00),并且它们不居中(Cpk<Cp)。
下图显示了当实际生产过程处于统计上不可控(不可预测)状态时的另一种选择。它们的分布 6σ 不可预测地缩小然后扩大,它们的平均值也不可预测地改变其相对于名义公差范围的位置。所有生产出来的零件都要分为符合公差带的和不符合公差带的,进行100%的控制。没有人事先知道有多少细节会不一致,也许是100%。没有人能够预测统计上不可控过程的行为。生产过程的不可预测性给企业带来的总损失是最大的!通过这种工艺生产的零件并不统一。
数字化模式可能是理想的,但公司整体的损失可能是最大的。
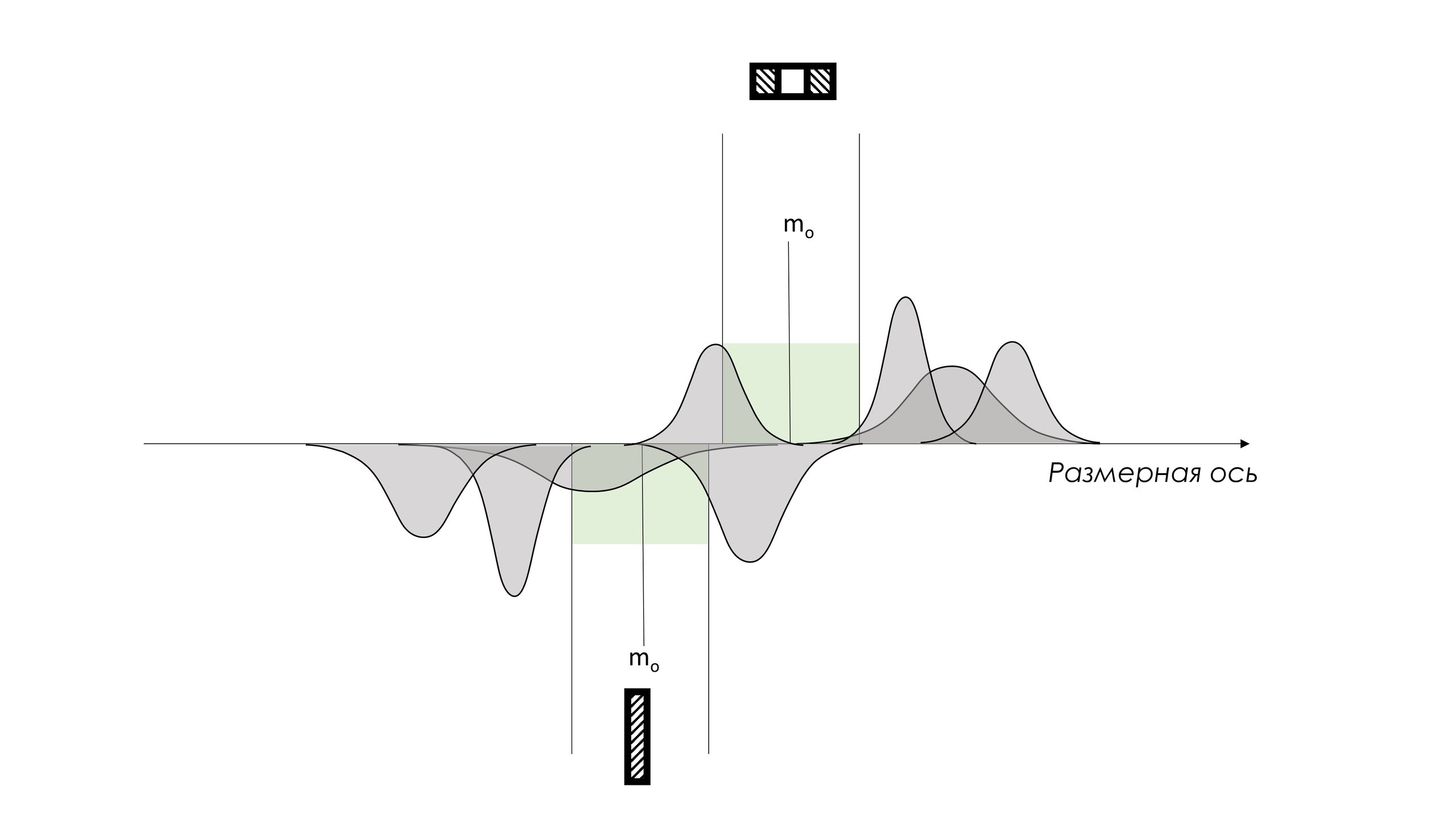
图 9. 生产过程处于统计上不可控(不可预测)的状态。它们的分布 6σ 不可预测地缩小或扩大,它们的平均值也不可预测地改变其相对于名义公差范围的位置。
在这个问题上的额外和重要的一点是测量系统稳定性的强制性要求,测量系统偏差的分析,考虑到更严格的生产规范中测量系统的误差。我们的文章中讨论了后者: 规格中的产品实际上符合要求吗? 。
最后,我们遇到了与数字模型的次优化相关的问题,而不是需要根据其目标优化公司所有部门的活动,作为一个整体系统,例如,生产可靠的产品系列发动机为运营商提供最低的拥有成本。
“次优化比优化更容易实现。然而,次优化并不便宜。次优化可能会造成改进的假象,但实际上它会造成阻碍真正进步的障碍。而且,某个部分的次优化常常损害其他部分,从而使整体变化造成更大的损害。” “这没有好处。它也让做出真正有利可图的改变变得更加困难。”
通过进一步的交谈,我们发现该公司的生产管理层和设计师都不知道他们的实际生产流程是如何运作的。但休哈特控制图仍未用于评估状况和改进流程。
在这种情况下,设计工程师只能满足于标称材料的公差范围和理论属性,而生产人员在没有管理层的帮助和理解变异性本质的情况下,执行 第一类和第二类错误 尝试生产具有所需特性的零件并组装成品。
公司不同部门的单独 KPI 只会让事情变得更糟。
您的企业正在发生什么?
爱德华兹·戴明准备好了 帮助管理的问题 , 这里是其中的一些:
- 你们的生产工艺稳定吗?
- 你怎么会知道这事?
- 你有什么数据?
- 您正在采取哪些措施来弥合产品设计、实际生产和交付之间的差距?
如果您对上述问题没有明确的答案,那么您如何依赖数字装配流程并用测试数字模型代替现场测试?!
“我们对材料、人力和机器时间的浪费感到遗憾。当一家公司无法利用和开发其现有潜力时,知识的浪费就更令人遗憾了。”
我们看到许多数字模型本身存在次优化的证据,而没有考虑数字模型应该服务的总体系统目标。所有这些都是为了对臭名昭著的开发生产力进行次优化,并且常常不加考虑地降低成本,而没有对生产流程给予应有的关注。
“如果不考虑产出的目的,就不能考虑产出。”
在产品开发人员效率被视为减少开发时间和成本的环境中,依靠用虚拟测试代替现实生活中的产品测试是一个错误,对于整个公司来说可能会付出非常高昂的代价。这都是一种偷工减料的尝试。使用休哈特控制图分析生产过程和售后数据将显示设计过程的优化如何影响它们。
“然而,有必要对生产绩效进行系统分析,以确定改进措施是否实现了目标以及它们是否适当。”
分析所采取的改进措施的有效性的最好、最简单的工具是休哈特控制图。
以下摘录自马文·曼德尔 (Marvin Mandel) 的《衡量和提高服务和政府组织的生产力 - Aoyama Dai-ichi Mansions, 4-14 Akasaka 8-chome, Minatoku, Tokyo 107》,1975 年。 – 第 3–4 页)对此进行了阐述问题:
“如果不考虑系统创建的目的,就无法考虑输出。
为了创建一些背景,让我们分析几个例子。据说,美国伟大发明家托马斯·爱迪生在美国国会提出了一种投票机来改进这一程序。他向议长和参议院主席展示了他的设备。根据发明者的想法,每位国会议员和参议员的椅子上都会有三个按钮:红色表示“不”,绿色表示“是”,白色表示“弃权”。
爱迪生建议,在投票开始时,参与者按下相应的按钮,之后就会立即出现一份报告,显示每个人的投票情况以及总体结果如何。爱迪生自豪地向参议院议长和议长保证,他的设备将消除顺序唱名投票方法中出现的错误,显着缩短投票时间,并提供其他优势。
当众议院议长和参议院议长在他说到一半时打断他,并宣称这种制度完全不可取,不仅不会改善众议院或参议院的工作,反而会彻底扰乱众议院的工作时,他感到非常震惊。美国国会顺利运作。从爱迪生的角度来看,这是一种进步,相反,从国会的角度来看,则是一种恶化。点名过程的长度是国会决定做什么的审议过程中不可或缺的一部分。
爱迪生的提议——快速投票——不符合国会的目的。”
该怎么办?
首先,你需要改变你的管理方式并摆脱 致命疾病和转型障碍 。
设计产品时,不要仅使用公差表,而是要考虑现实世界的工艺能力以及几何形状、材料属性和其他特性固有的可变性。
请注意,生产规格(公差)必须考虑到您的测量系统的误差,您的控制至少有 96% 的概率不会遗漏有缺陷的产品,即比客户对测量系统的两个可能误差的公差更窄。双方现场客户端访问。测量系统本身必须稳定!请参阅这篇文章的解释: 规格中的产品实际上符合要求吗?
在经验丰富的讲师的指导下,使用休哈特控制图推动设计变更、公差变更,或要求制造部门和供应商在必要时改进流程。并且不要满足于空洞的响应陈述,要求以产品和过程关键特性控制图的形式对质量特性进行统计确认。
我在下面的短视频中展示了改进生产流程的建议。
视频 1。流程改进路线图。视频中元素的符号:。 НГД 和 IOP - 分别为公差下限和上限(Eng、LSL 和 USL); m0——标称公差范围; LGP和ВГП——流程的下限和上限(英文LCL和UCL); CL - 过程的中心线(平均)。
全新的、甚至按照世界标准的一流质量管理体系软件(QMS软件)的质量管理工具可以为设计、生产、采购和销售部门之间交换信息和建立团队合作提供重要帮助借助 SPC 研发模块 QM,利用休哈特控制图,使用有关其自己的生产流程和供应商流程的关键质量特征可变性的数据。
我们提供我们全部力量的整合 软件 俄罗斯企业申请: CAD (CAD)- , PLM- , ERP , MES- , 实验室信息管理系统 、培训并为公司员工提供持续有效的科学和实践支持。
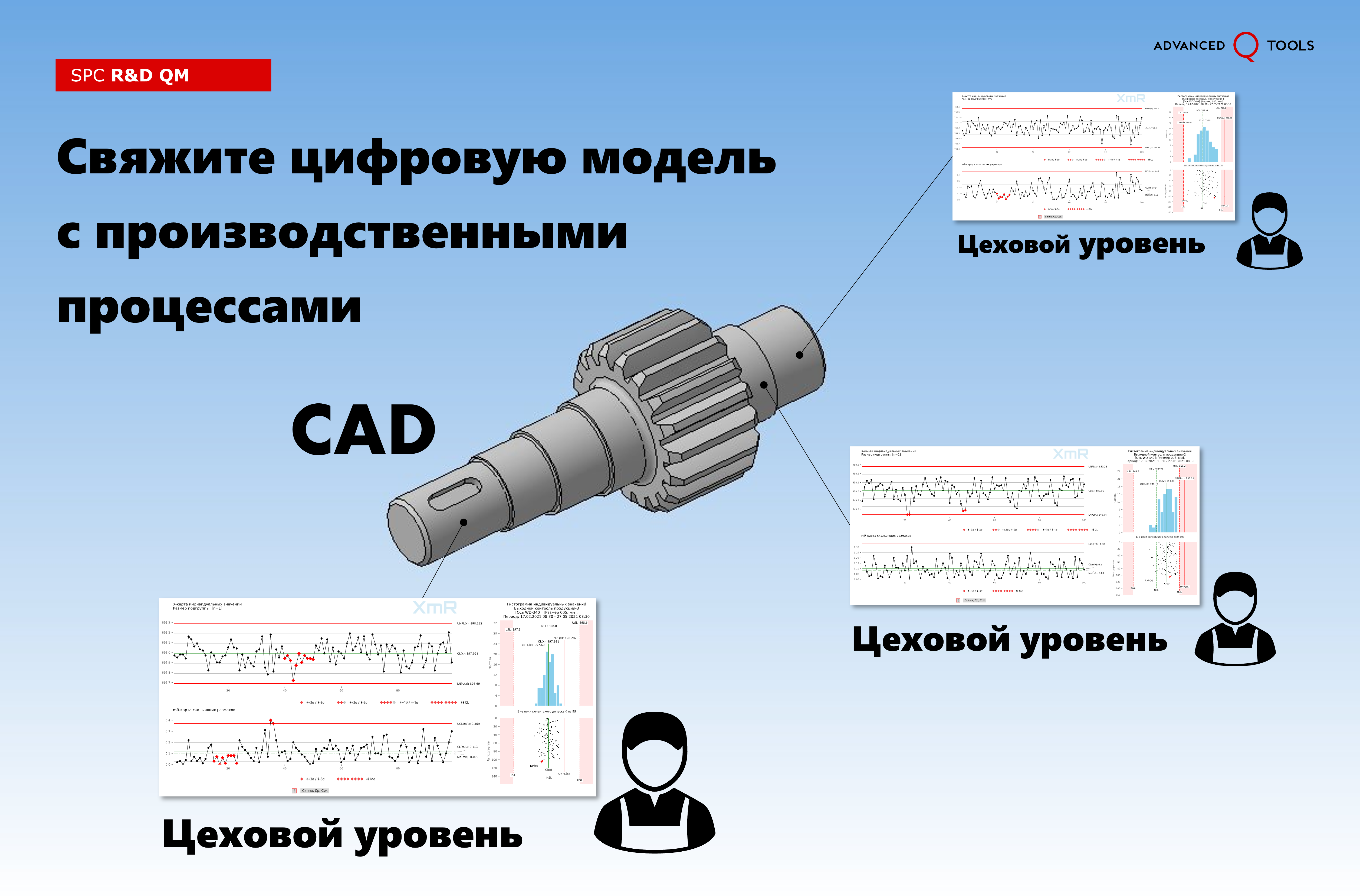
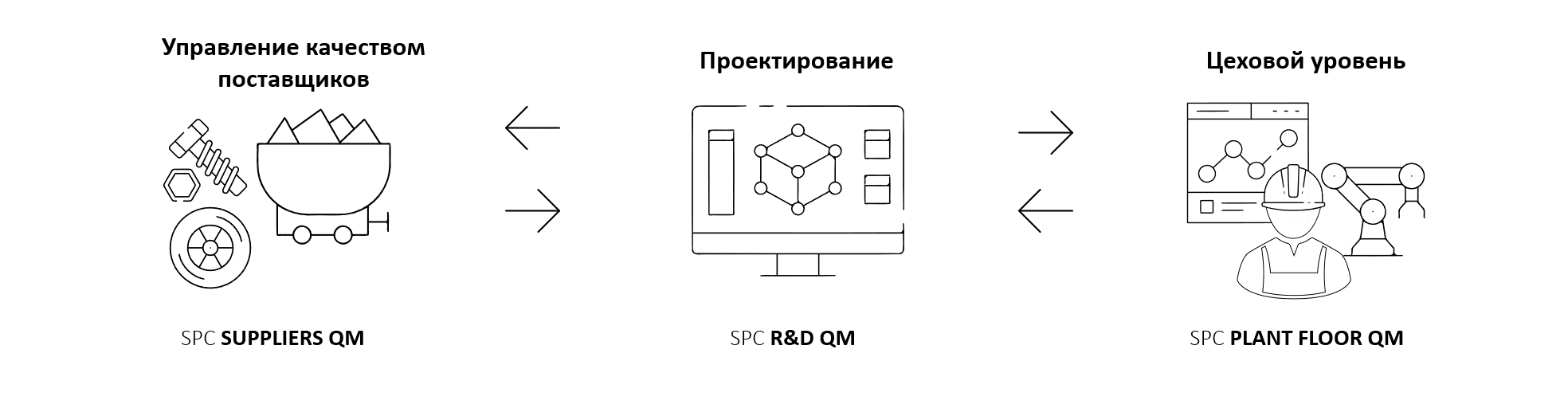
图 10. 下一代质量管理工具 SPC R&D QM。供应商质量管理、设计和生产职能的相互作用。
将统计过程控制与产品设计模块结合使用的一个示例是 肠易激综合征质量管理系统 – 由Siemens PLM Software 开发的跨行业QMS(质量管理系统)级解决方案。
再次强调,在没有深入理解统计过程控制(SPC)方法的情况下,碎片化、不系统地使用统计过程控制(SPC)方法不会给整个公司带来显着的改进。
“任何计划有效使用控制图的组织都必须首先分解 所有障碍 戴明描述的。
你不能只是“实施统计过程控制”。控制图不能在真空中工作。它们的使用对工人和管理层提出了一定的要求,组织必须尽一切可能满足这些要求。一旦控制图哲学成为企业文化的一部分,甚至成为组织本身结构的一部分,工人或管理层偶尔的干扰将不再能够干涉任何事情。
统计过程控制首先是一个有一定方法支持的整体世界观。这是一种思维方式,这就是它的全部内容。没有这样的思想,任何方法都是毫无用处的!只有高级管理层才能强调控制图对于持续改进的重要性。如果高级管理层对此提供积极支持,实施控制图的潜在影响将超出所有人的预期! ”
最后,我想提醒大家四个密不可分的部分之一 深层知识体系 ,由爱德华兹·戴明形式化,即在理解系统方面。我建议不要对系统的任何部分(部门)进行次优化,而是专注于改善系统所有组件的交互以实现其主要目标。
“系统是组织内一系列相互关联的功能或活动,它们共同努力实现组织的目标。
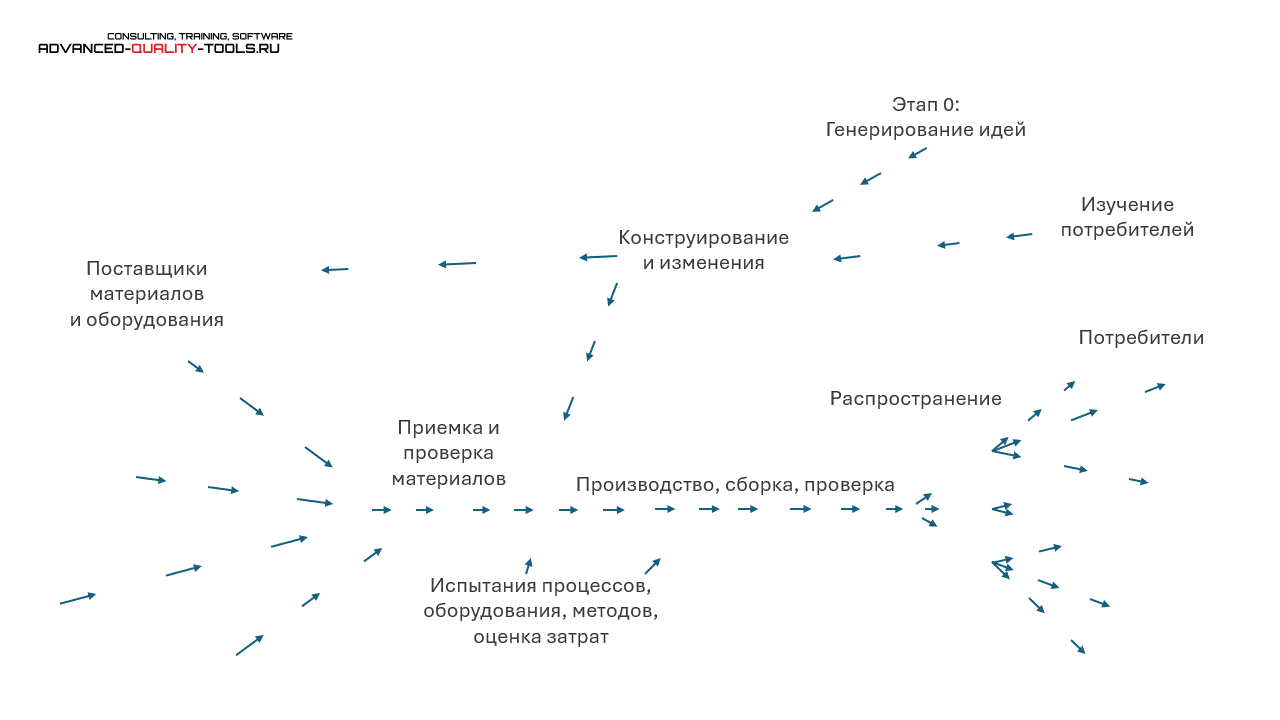
图 11. 生产被视为一个系统(材料来自 Edwards Deming 的讲座,1950 年,日本)
该图不仅说明了物料流向,还说明了将公司作为一个系统进行管理所需的信息流向。使用框架可以为产品或服务的持续改进和持续学习提供反馈。”
以供参考
国外工业企业很早就开始使用二维(2D)统计分析方法来改进设计流程。下面是 1998 年波音文件的页面截图,可以在 部分下载 参考书目 我们的网站。
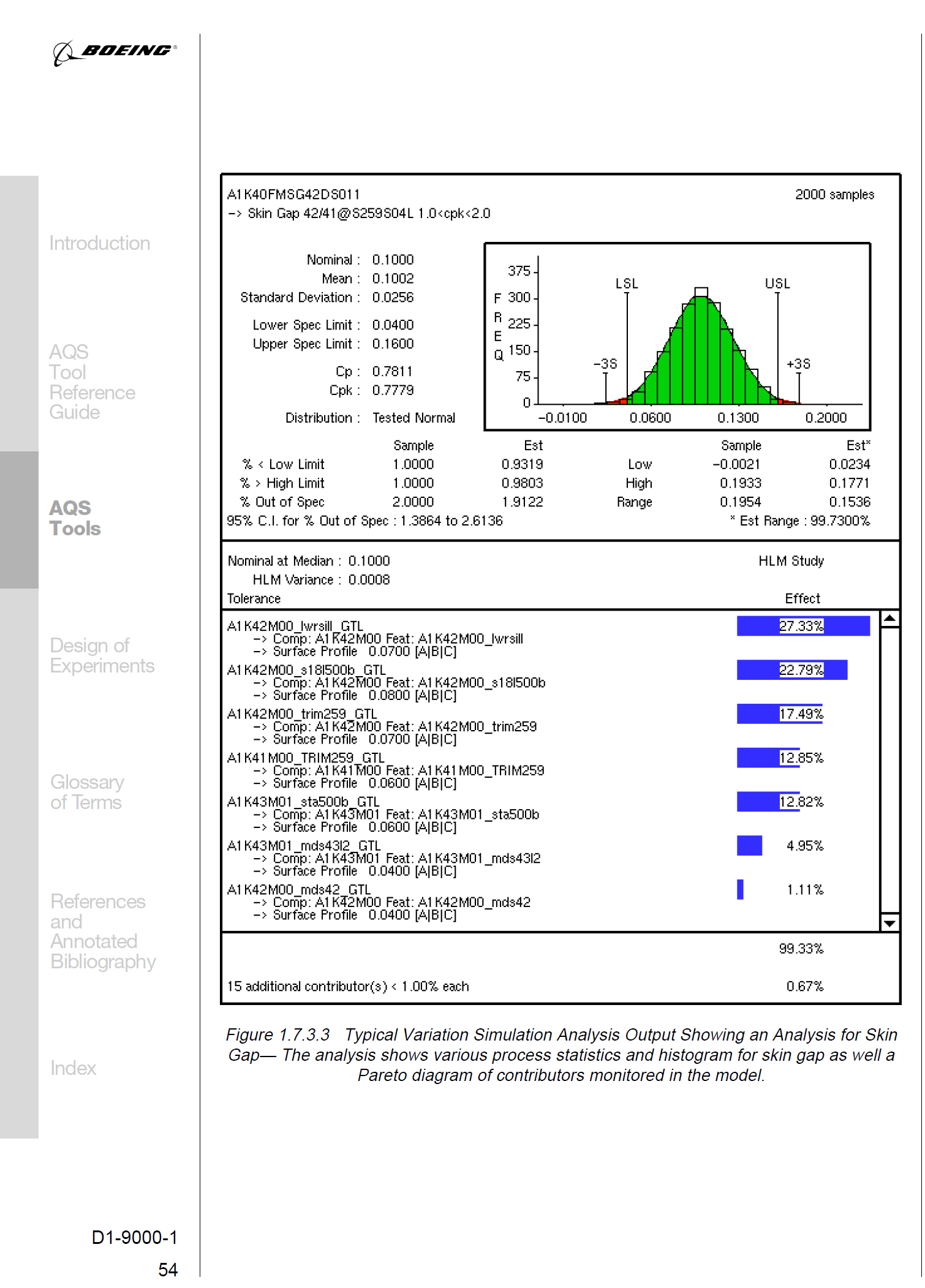
图 12. GD&T(几何尺寸和公差)领域的二维 (2D) 统计变异分析。波音公司小册子“高级质量系统工具”页面 | “先进的波音质量体系工具”,1998 年。
此外,甚至GD&T(几何尺寸和公差)领域的三维(3D)统计变异分析也早已被西方领先公司所采用。
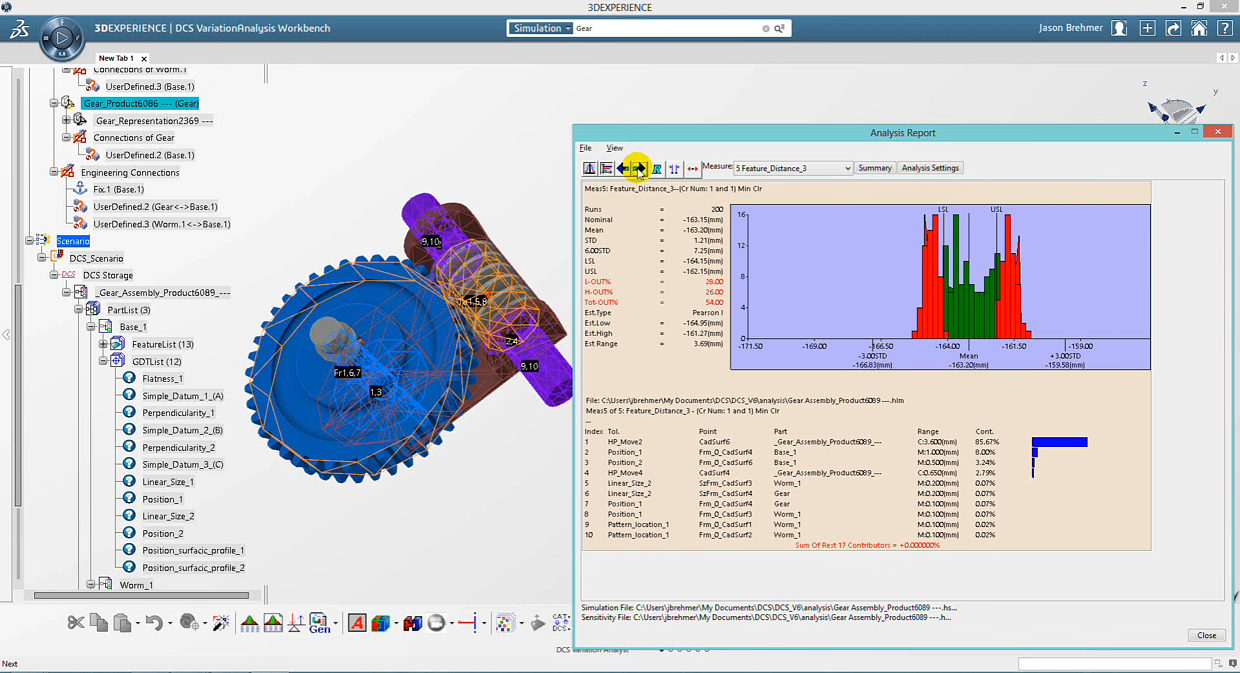
图 13. GD&T(几何尺寸和公差)领域的三维 (3D) 统计变异分析。美国Dimensional Control Systems Inc.公司的软件产品3DCS Variation Analyst既可以作为集成到CAD CATIA V5、SOLIDWORKS、CREO、NX、3DEXPERIENCE中的工具,也可以作为独立工具。
这些公司使用 GD&T(几何尺寸和公差)领域的自动化仿真工具来验证数字模型中公差字段的正确对齐。例如,在出版物中 [22] 波音公司 1998 年的“高级质量系统工具”(第 51 页)描述了三维统计变分分析的目的和操作原理。请参阅文档中对此问题的更详细讨论 [23] 波音公司报告 ISSTECH-95-030,公差叠加分析方法,由 Fritz Scholz (1995) 撰写,第 7 节 参考书目 我们的网站。
他们可能会犯错误
虽然 3D 统计变异分析是了解设计产品(数字模型)变异性的下一步,但它是一种高级的子优化,因为它与生产过程的实际变异性无关。
2D、3D 统计变异分析的缺点
1. 过程可能处于统计上不可控(不可预测)的状态,这使得这种分析纯粹是理论上的。
2. 稳定过程的受控特性的传播可以比公差带更宽或超出公差带。同时,如果生产管理层决定保留一些超出容差限制的产品,例如通过降低其“质量等级”,则变异分析将不会给出可能的配对选项这样的部分。
3. 稳定过程的受控特性的传播可以在容差范围内运行,那么您将毫无意义地进行现实中不会发生的选项的计算。
4. 流程可能不太集中在公差范围内,则存在犯上述第 2 段和第 3 段错误的风险。