统计过程控制(SPC),针对生产过程和操作的配给(计时)的错误做法。以及休哈特控制图如何帮助改进生产计划。
材料准备者:AQT 中心科学主任 谢尔盖·格里戈里耶夫 。
免费获取文章不会以任何方式降低其中所含材料的价值。
“基于质量的管理极大地改变了对经理角色的理解。管理者必须成为一个领导者,其主要任务是创建一个使员工能够有效工作的系统。发挥这一作用的必要条件是领导者了解可变性的一般原因和特殊原因之间的差异。”
普遍应用的流程和操作标准化程序完全忽略了标准化工作的可变性的本质。因此,考虑到标准化工作所处状态的差异,即统计上受控(可预测的行为)或统计上不可控(不可预测),谈论标准化者和管理者甚至没有意义。
考虑一下!您可以通过在随机时间点对过程或操作进行点估计来“标准化”,然后在规划和控制中使用该数据。
在完全混乱的状态下,配给有助于深入了解您一无所知的流程,但却成为流程改进的障碍。如果标准化指标得到满足,为什么还要费力改进流程呢?如果不遵守,我们就会剥夺“有罪扳道工”的工资并处以罚款。如果规范重叠得更好,我们会奖励那些“参与”的人,也许还会修改“规范”以收紧它。
回答问题:如果图表(图 1.)显示某个流程的重要输出,例如每个班次的输出,您将在纵轴上设置“真实”目标(计划、规范、任务)对于下一个班次或班次分配的该指标? 1 到 4 位于哪个灰点或区域?记住你的答案。
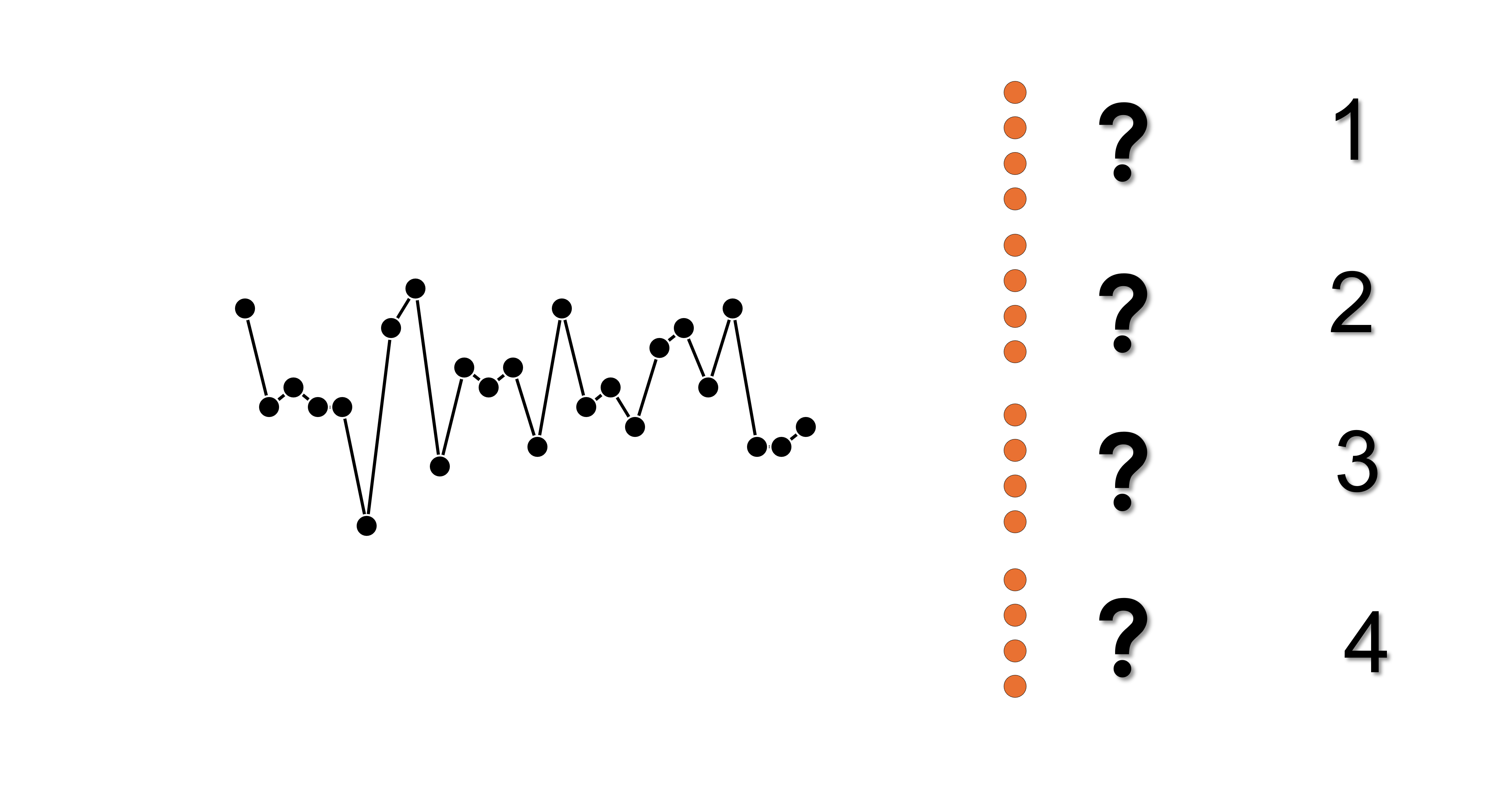
图 1. 流程时间表。该过程的“真实”数字目标将位于哪个灰点?
证据1
进行“标准化”的过程处于统计控制状态。如果您选择了区域 2 或 3 中的目标:
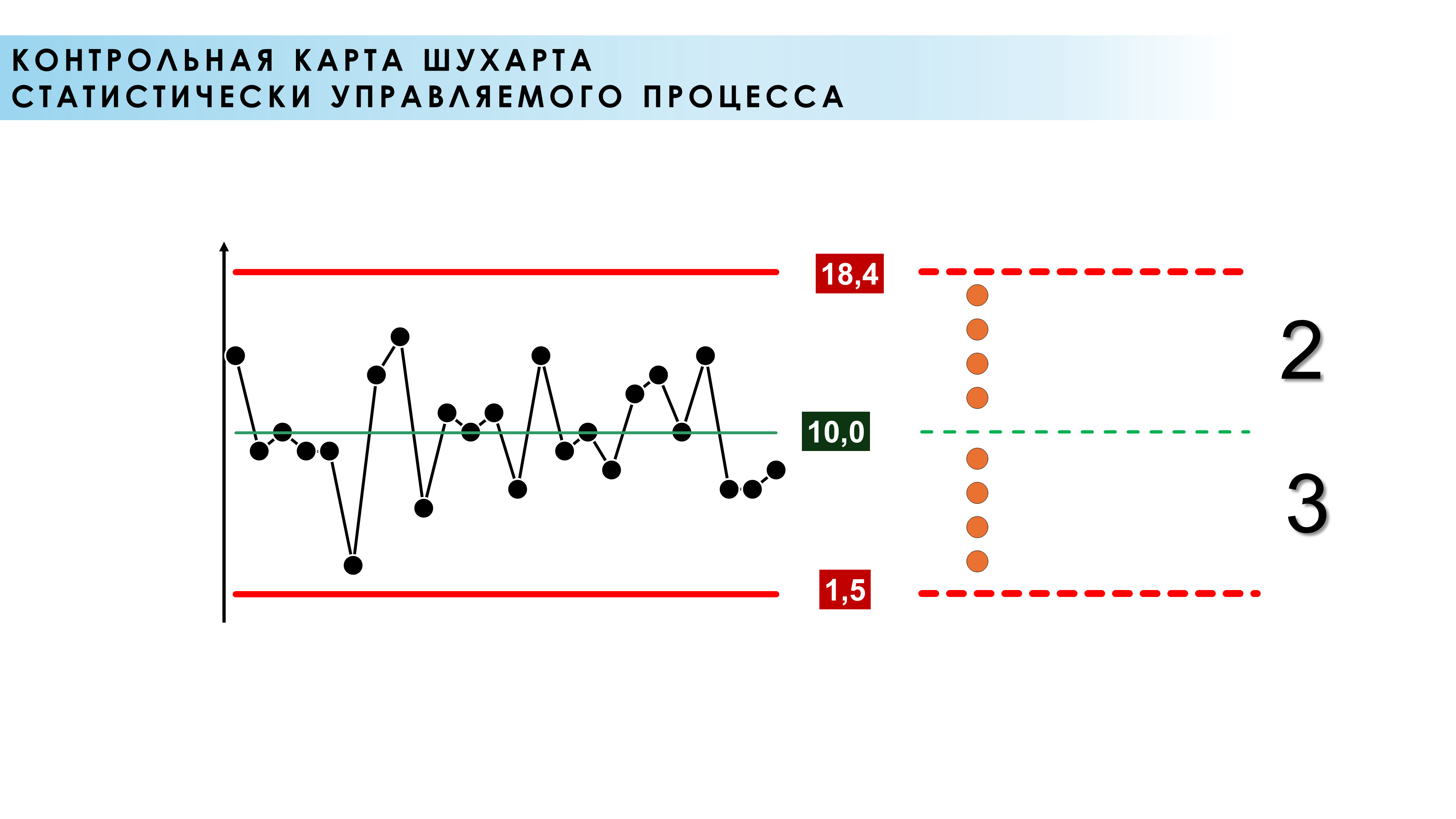
图 2. 统计控制过程的休哈特控制图。区域 2 或 3 中过程的数值目标。CL - 中线,ВКГ - 控制上限,LKG - 控制下限
答案:当一个过程表现出合理程度的统计控制时,该过程的行为是可预测的并且处于最佳状态。这样的流程(以及其中的人员)会尽其所能(见图 2)。了解此类过程的过去行为可用于预测其未来,即控制范围内的随机变化,数据根据经验法则分布(图 3)。为了更好地理解本文中的内容,我们建议您首先阅读这篇文章: 变异性(变异性、可变性)的本质是统计思维的基础 。
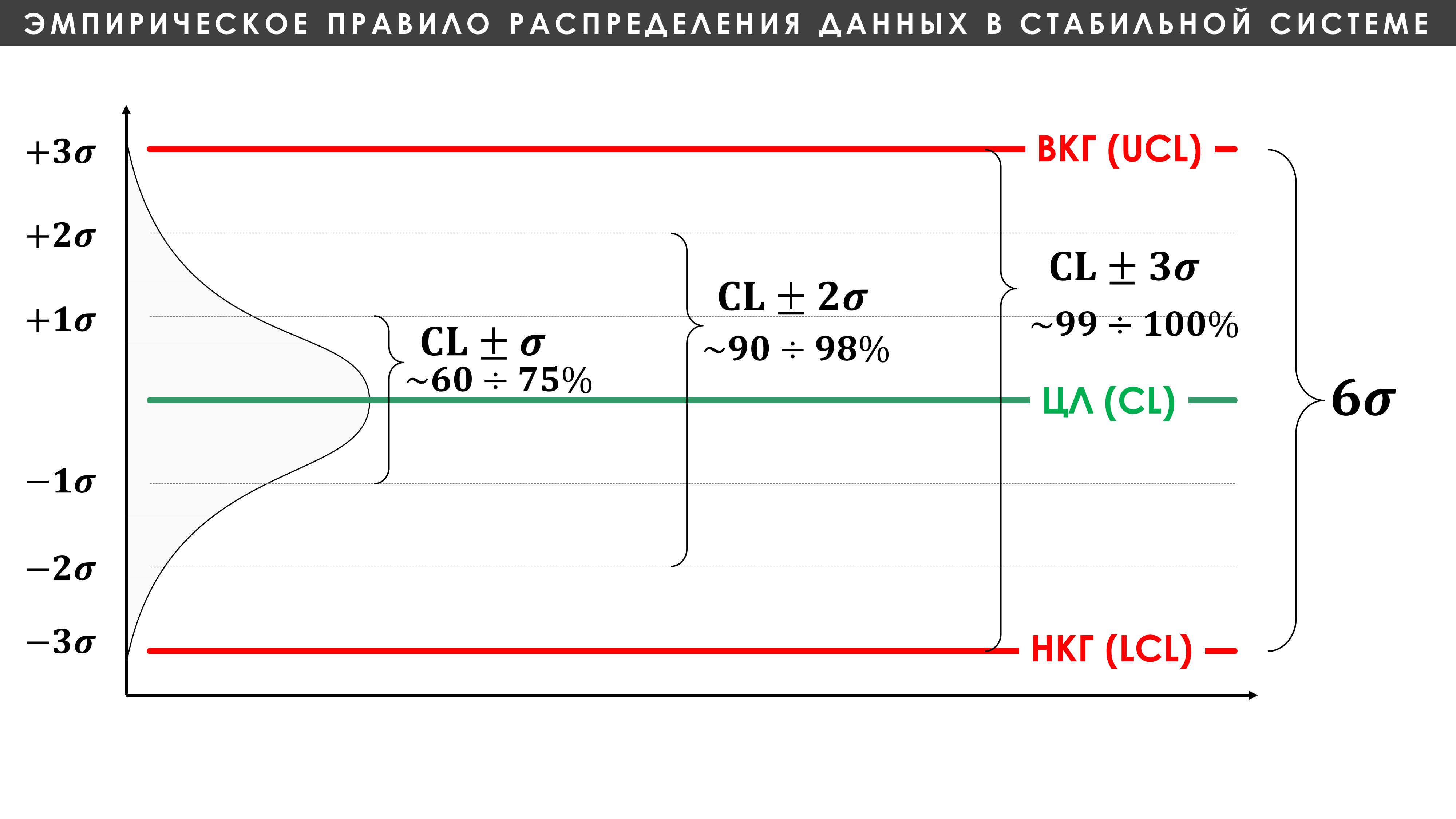
图 3. 稳定系统中数据分布的经验法则。休哈特控制图。 LCG - 过程的控制下限, ВКГ - 过程的控制上限。
“经验法则为我们提供了一种使用位置度量和分散度度量来描述数据的有用方法。如果给定一组同质数据,则:
1) 大约 60–75% 的数据位于平均值两侧的一个西格玛单位内;
2) 大约 90% 到 98% 的数据位于平均值的两个西格玛单位内;
3) 大约 99-100% 的数据与平均值相差不超过 3 个西格玛单位。
西格玛单位 (σ) 是数据规模的度量。一般散射统计数据可以使用已发布的公式*转换为 (σ) 单位。”
* 计算 σ 单位的公式,请参见 [11.1] GOST R 50779.42-99 (ISO 8258-91)。

图 4. 数据分布演示以及不随时间变化且处于统计控制状态(稳定过程)的过程的子组平均值和范围的相应控制 XbarR 图(XR 图)。
想一想:标准化人员是否使用处于统计控制状态的流程来完成工作?你怎么知道?哪一天(点)?
在这种情况下(图2),以在垂直轴上控制限和下控制限之间的任何点建立的具体数字目标和规范的形式对流程工作的干预是有限范围内的“轮盘赌游戏”。范围。这样的游戏与计划无关,更与流程改进无关。
如果您选择了区域 1 或 4 中的目标:
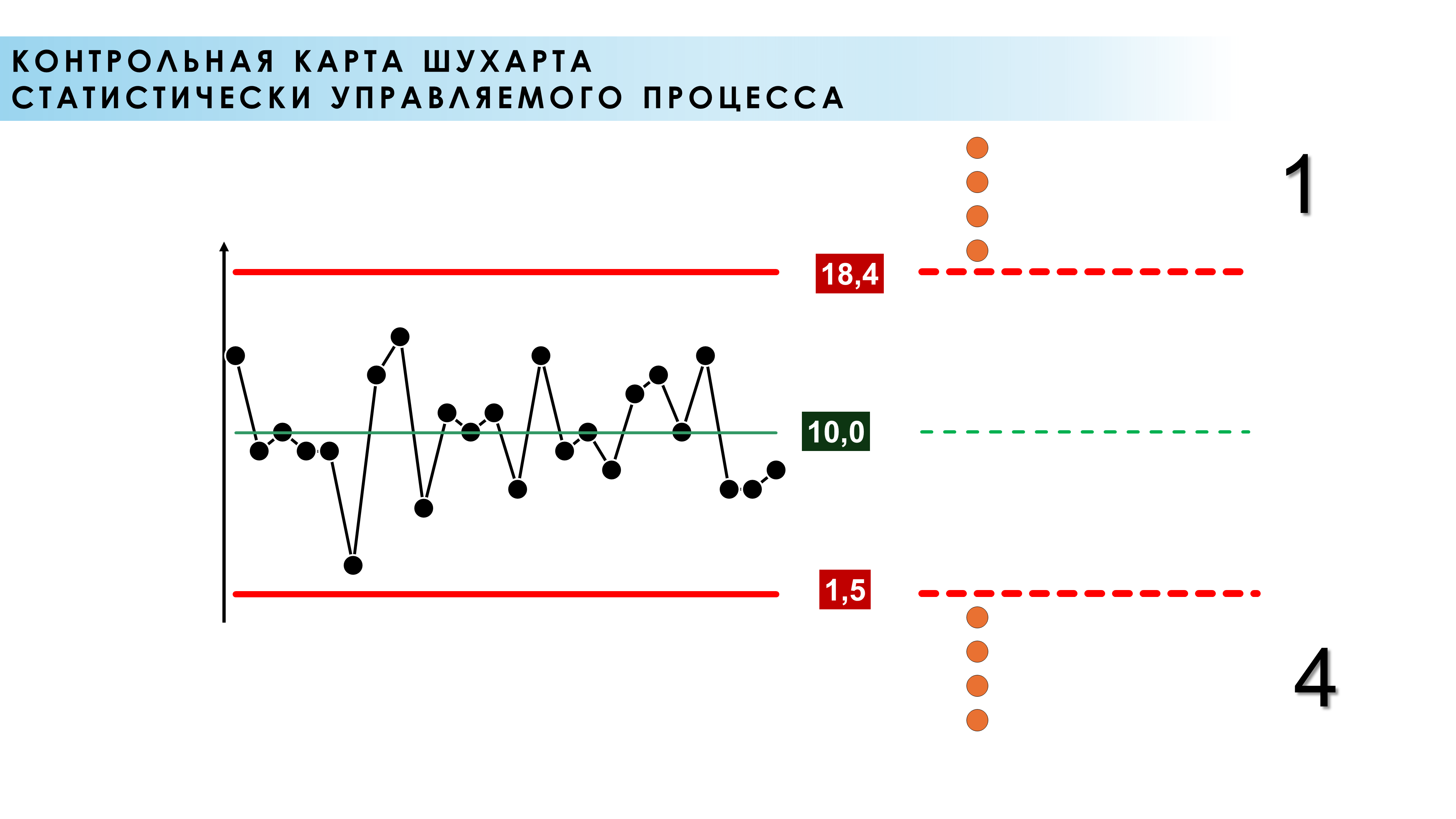
图 5. 统计控制过程的休哈特控制图。您设置的“真实”数值过程目标是否位于过程的自然控制上限或下限之上(在控制限之外)? CL - 中线,ВКГ - 控制上限,LCG - 控制下限
超出统计控制过程的控制极限范围的目标对于工人来说没有任何意义。
如果目标高于系统的能力(高于控制上限),那么这样的目标会引起工人的愤怒和不满。我不会谈论在相同条件下通过合理管理对低于控制下限(4 区)的发电进行规划的选择,因为这种情况不太可能发生。
对于处于统计控制状态的过程,预期点高于控制上限或低于控制下限(图 5.,区域 1 和 4),仅在三种情况下可能 [1]:
1.简单的数据失真。
2. 系统扭曲(例如,对选定的指标(例如指标 3)进行次优化,从而损害了其他同等重要的指标)。见图6。 (变形前)和图7。 (扭曲后)。
3.通过管理改变制度(流程)。这正是公司管理层应该做的。见图 8 和 9。
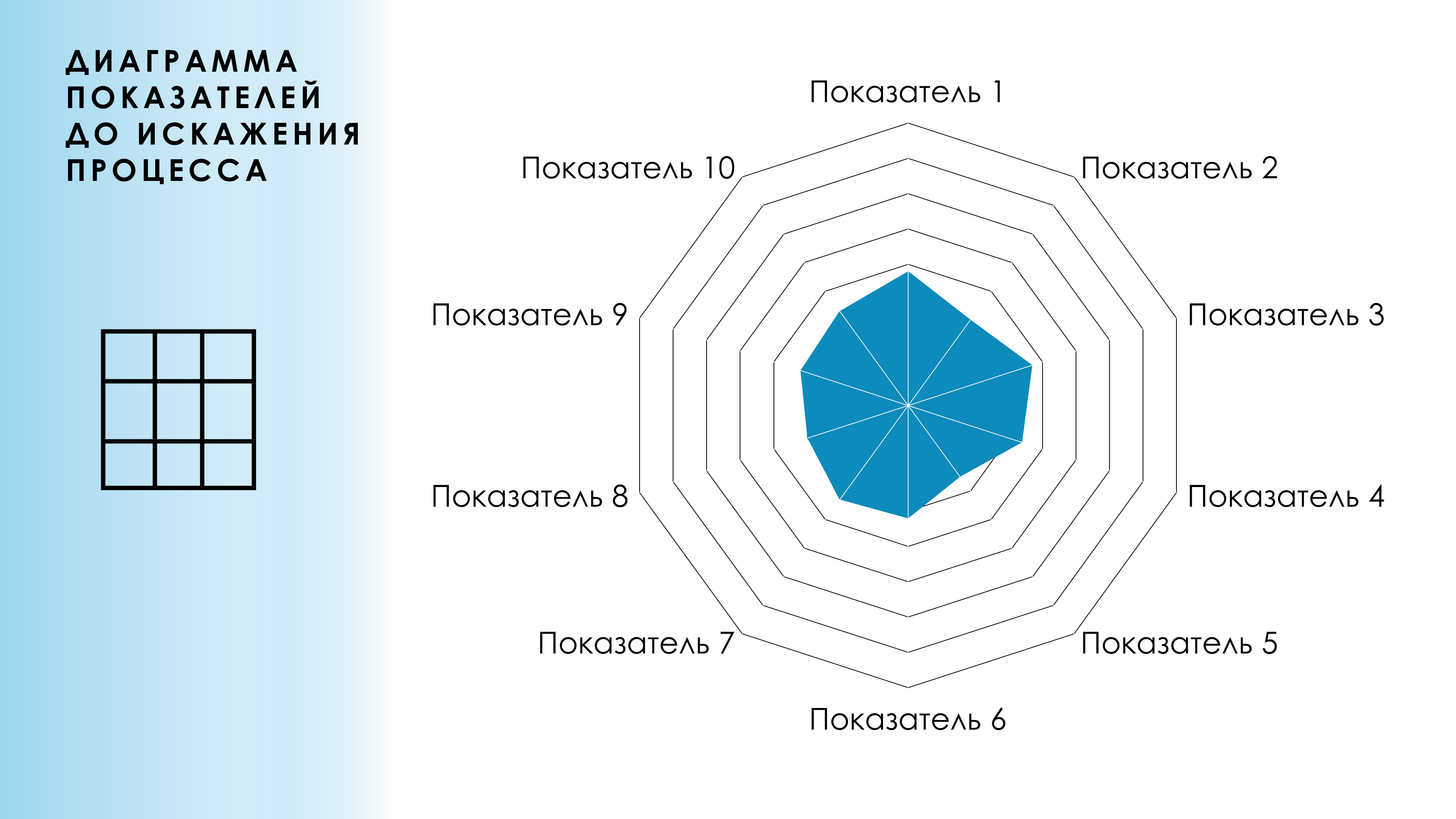
图 6. 流程扭曲干预之前的跟踪指标。
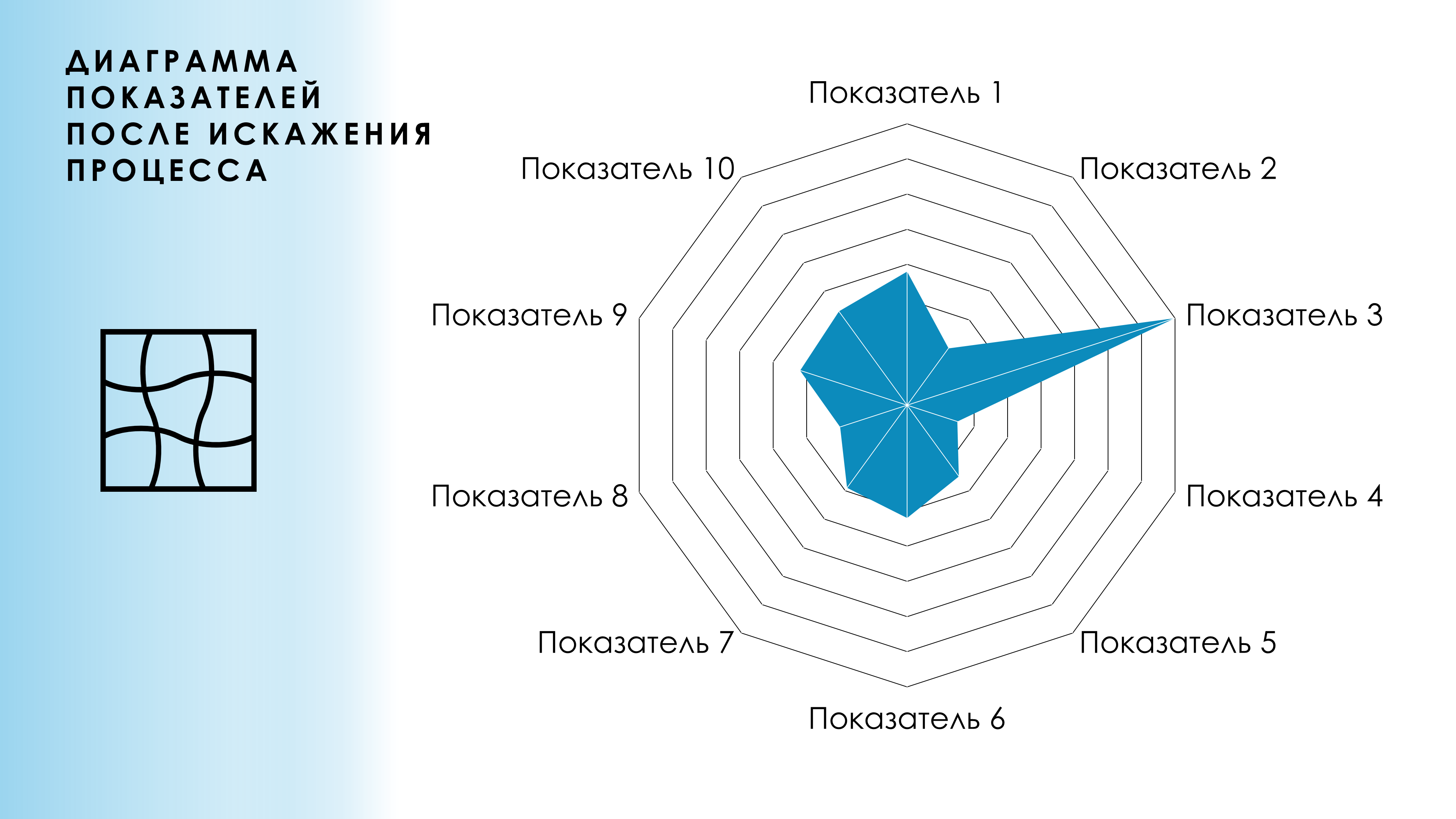
图 7. 流程扭曲干预后的跟踪指标。
最好的决定
在证明合理程度的统计控制的过程中,寻找导致观察到的随机变化高于或低于控制限范围内平均值的具体原因,并不具有成本效益。为了进一步改进(将平均流程转向预期目标并减少数据分散),需要在高层管理人员的能力范围内,在流程设计和所有输入的改进层面进行系统性变革,即:原材料和材料、设备和工具的技术条件、人员培训、环境、管理方式、技术规范的完整性和清晰度等。工人是否可以影响这些因素对其活动的结果?统计控制的过程控制图始终允许您跟踪管理层进行的任何变更的结果。参见图 8 和图 9。

图 8. 在具有统计意义的时期内评估流程(系统)变化。将目标指向高于平均水平的过程,并不断减少可变性。
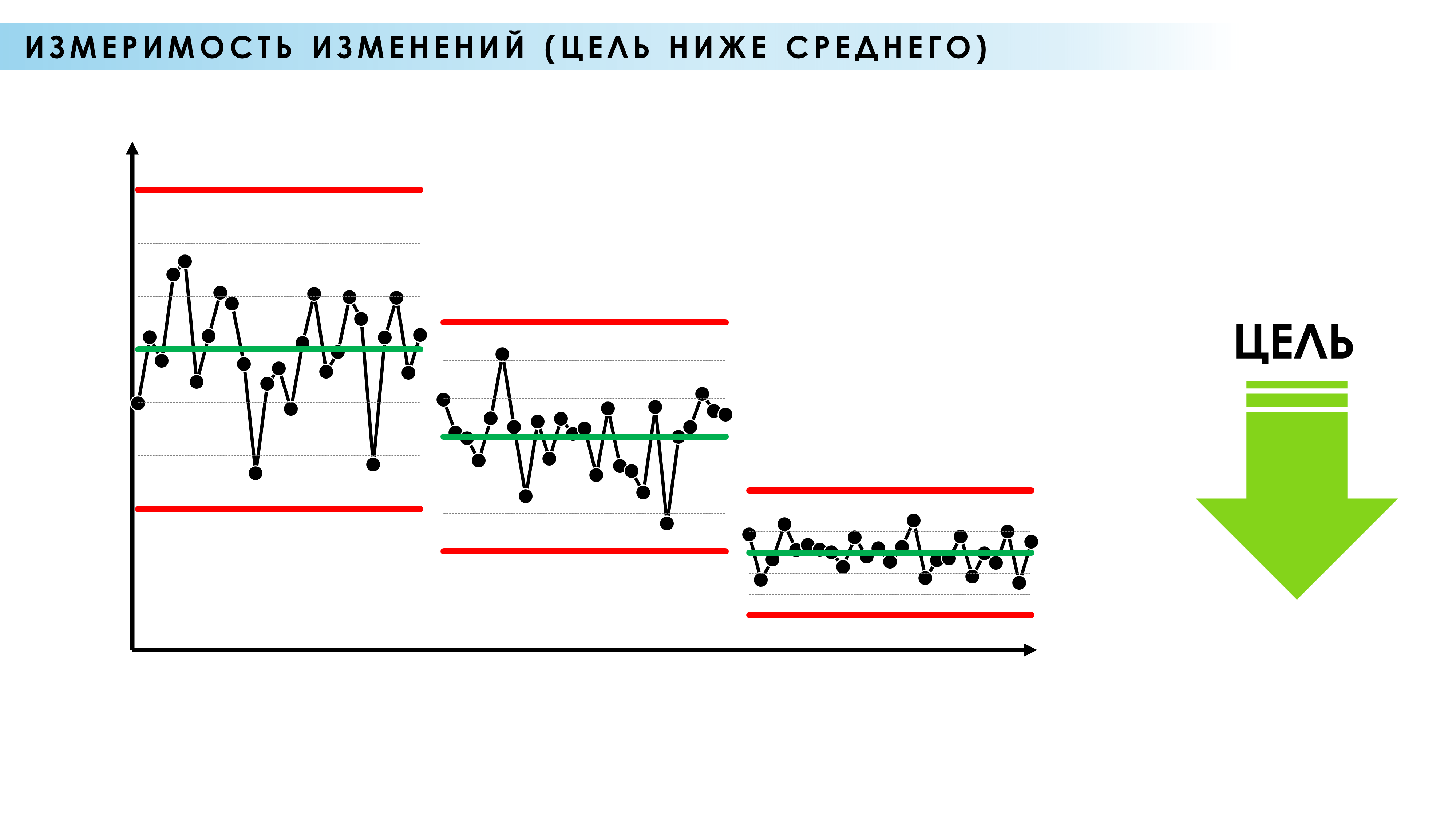
图 9. 在具有统计意义的时期内评估流程(系统)变化。将目标导向低于平均水平的流程,并不断减少变异性。
让我们回到配给
与我交谈过的经理们总是提到这样一个事实:工人在“配给”时故意使用“慢”模式。令人惊讶的是,尽管没有科学的解释,工人下意识地感觉到偶然性对他的工作的影响,或多或少地高于平均水平。当然,管理层会正常地接受标准化参数在管理层期望的方向上偏离平均值的随机波动。而同样在平均值“不良”一侧的随机波动将受到充分分析并寻找特殊原因。 “那些寻找的人总会找到”,即使是不存在的东西。
如果企业管理者不了解可变性的本质,工人和管理层之间的合作环境就不可能存在。结果,对管理层的不信任和恐惧持续存在。工人恐惧的后果是他们会可靠地隐藏流程问题(对于流程改进很重要的信息)。这是您在启动标准化生产运营计划时想要实现的目标吗?
参见实验描述 “漏斗和目标” 和 “红珠子” - 出色地展示了变化的本质和常见的管理实践。
“组织中所有问题(或改进机会)中不超过 6% 与变异的特殊原因相关;因此,它们可能(但不一定!)出现在普通员工的活动领域。在这种情况下,顶部在对其员工工作的系统的所有潜在改进中,管理者至少占 94%。
任何控制和工人的专业技能水平都无法克服该系统的根本缺陷。”
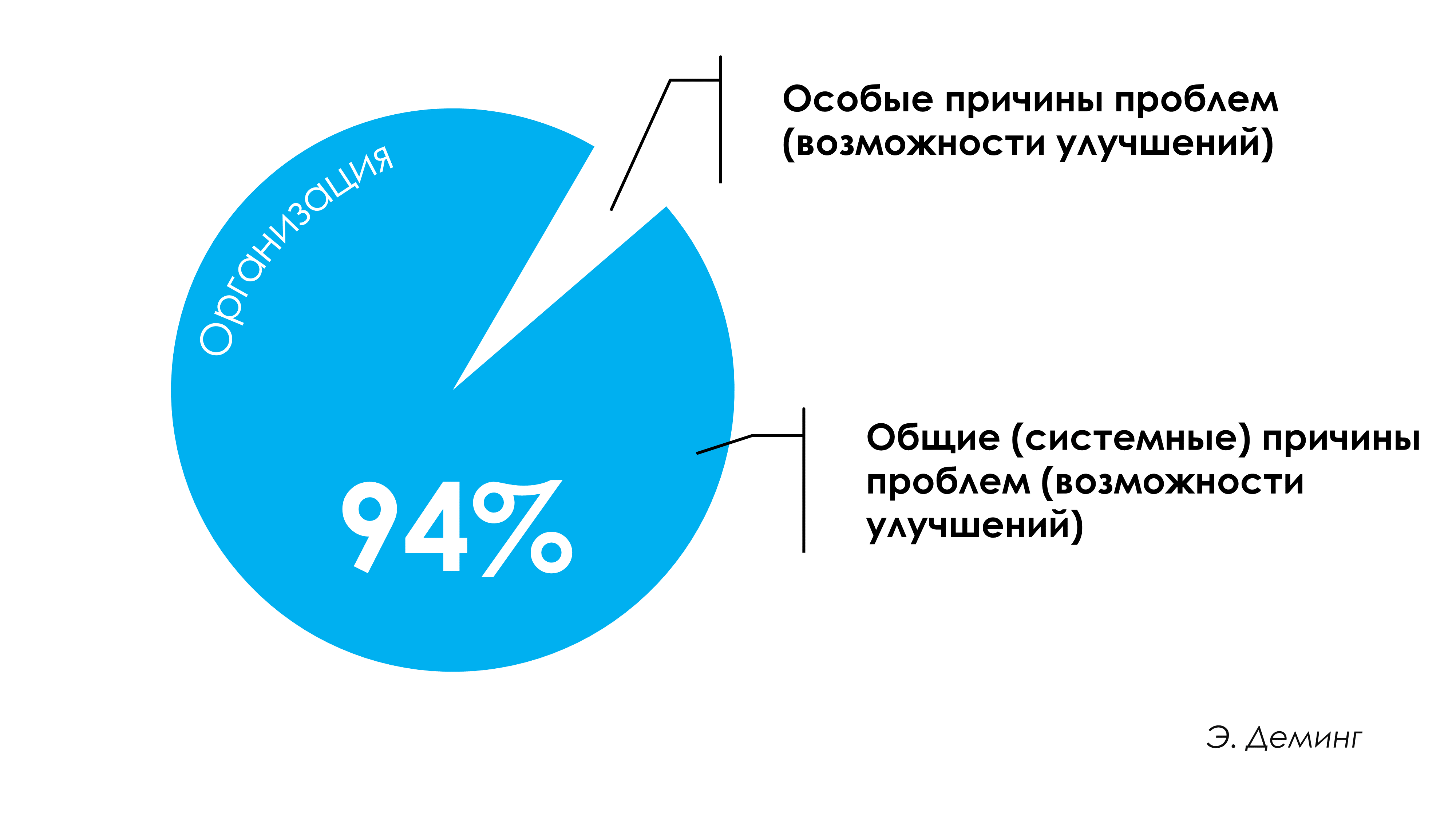
图 10. 在改进员工工作系统的所有潜在机会中,高层管理人员至少占 94%。 E·戴明
证据2
进行“标准化”的过程处于统计上不可控(不可预测)的状态。
如果一个过程表现出统计上的失控状态,则其行为是不可预测的(请参见下面图 11 和 12 中的控制图)。根据这一过程的过去来预测其潜力并讨论其可重复性是没有意义的。

图 11.休哈特针对统计上不可控过程及其无意义数值目标的控制图。 CL——中线,ВКГ——控制上限,LCG——控制下限。

图 12. 处于统计上不可控状态(不稳定过程)的时变过程的数据分布演示以及子组均值和极差的休哈特控制图。
想一想:标准化人员是否使用处于统计控制状态的流程来完成工作?你怎么知道?再说一遍,哪一天(点)?
不受控制的过程(包括管理层甚至没有考虑到的过程)的总成本是最大的。使这样的过程正常化是鲁莽的。首先,管理层需要将这一过程置于统计控制状态,消除变异的特殊原因,其效果在最差结果的点上显现出来。需要找出具体原因,导致分数超出控制限度,并且取得更好的效果,也许这是员工的独特性或他的方法的结果,以及这些方法是否与整体目标很好地一致。业务系统,其他员工可以接受培训。

图 13. 不受控制的过程(包括管理层甚至没有考虑到的过程)的总成本是最大的。
那么如何计划生产呢?
你可能会反对:“那如果没有标准,没有具体数字的排班计划,我们怎么计划生产呢?”当您使用休哈特控制图来研究过程时,您拥有的不仅仅是任意的规范和任务。您知道流程的能力,并且对于处于统计控制状态的流程来说,这种能力是可预测的。有关更好解决方案的提示,请参阅第 11 段。“消除任意的定量规范和任务” 爱德华兹·戴明的 14 条管理要点 。
在规划时,需要使用的不是“凭空而来的标准”或随机获得的测量结果,而是有关稳定流程的能力、生产率的平均值和变化(例如每小时的产品)的知识。了解任何系统中数据分布的经验法则,以证明合理程度的统计可控性(无论围绕平均值的数据分布形状如何),请参见上面的图 3。
当然,这比在下次董事会会议上提出所需的“数字”要困难得多。您必须聘请统计过程控制领域的专业人员,研究过程的特性,并从办公室到车间再到工作场所。但这绝对更有效。
例如,计划订单是根据连成一条线的工序生产链中瓶颈(生产率最低的工序)的平均生产率值来进行的,呈现出统计受控状态。
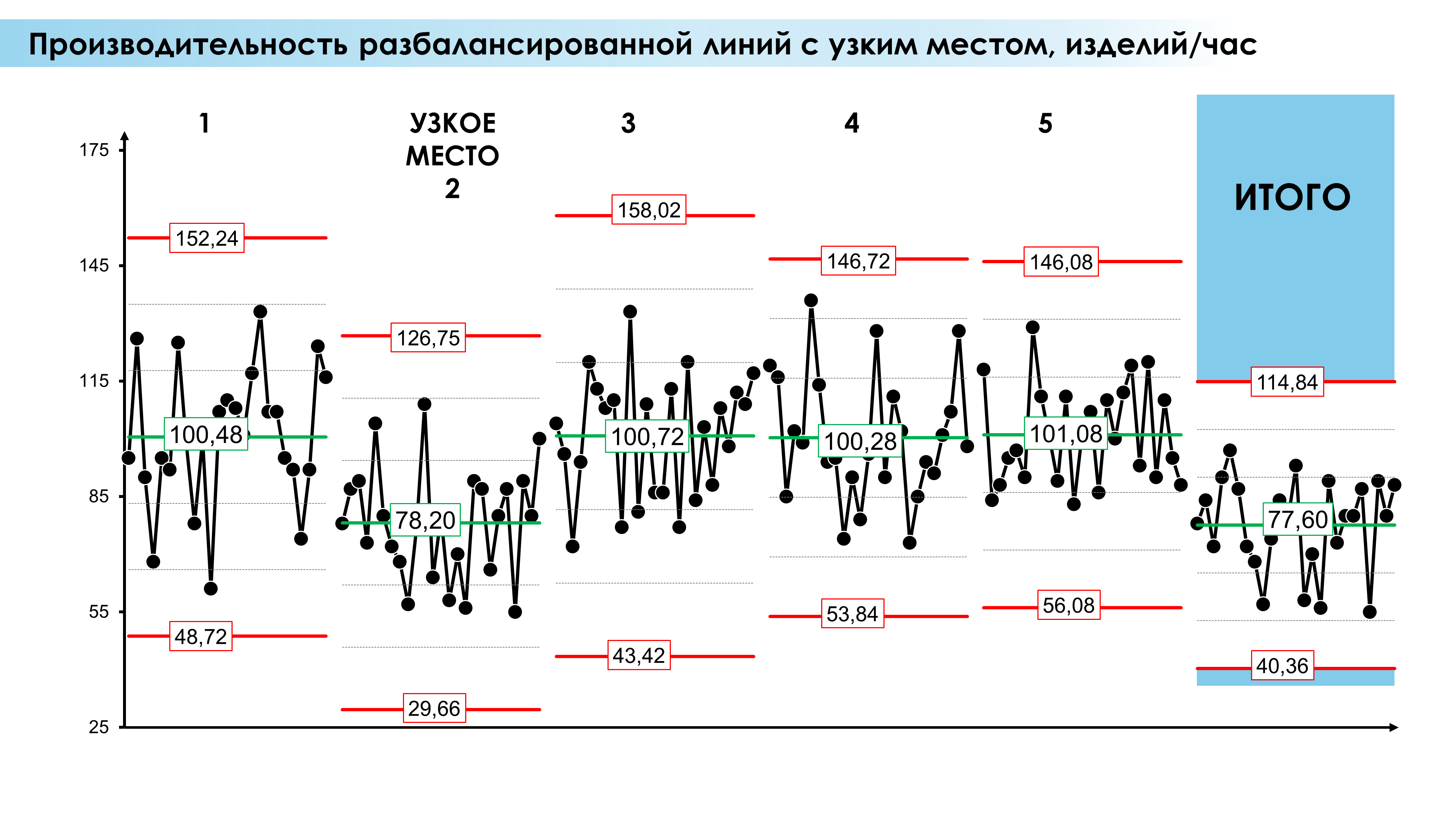
图 14. 使用 Shewhart 控制图演示了具有瓶颈的不平衡生产线的最终性能。分析不平衡线路性能的方法,在模拟方法方面,借鉴了Donald Wheeler和David Chambers的书。 “统计过程控制:使用 Shewhart 控制图进行业务优化”,第 366-370 页 [4]。该图纸是使用我们开发的 “Shewhart 控制图 PRO-Analyst +AI(适用于 Windows、Mac、Linux)” 。
通过在流程前面存在最大的互操作库存,可以轻松确定流程链中的瓶颈。
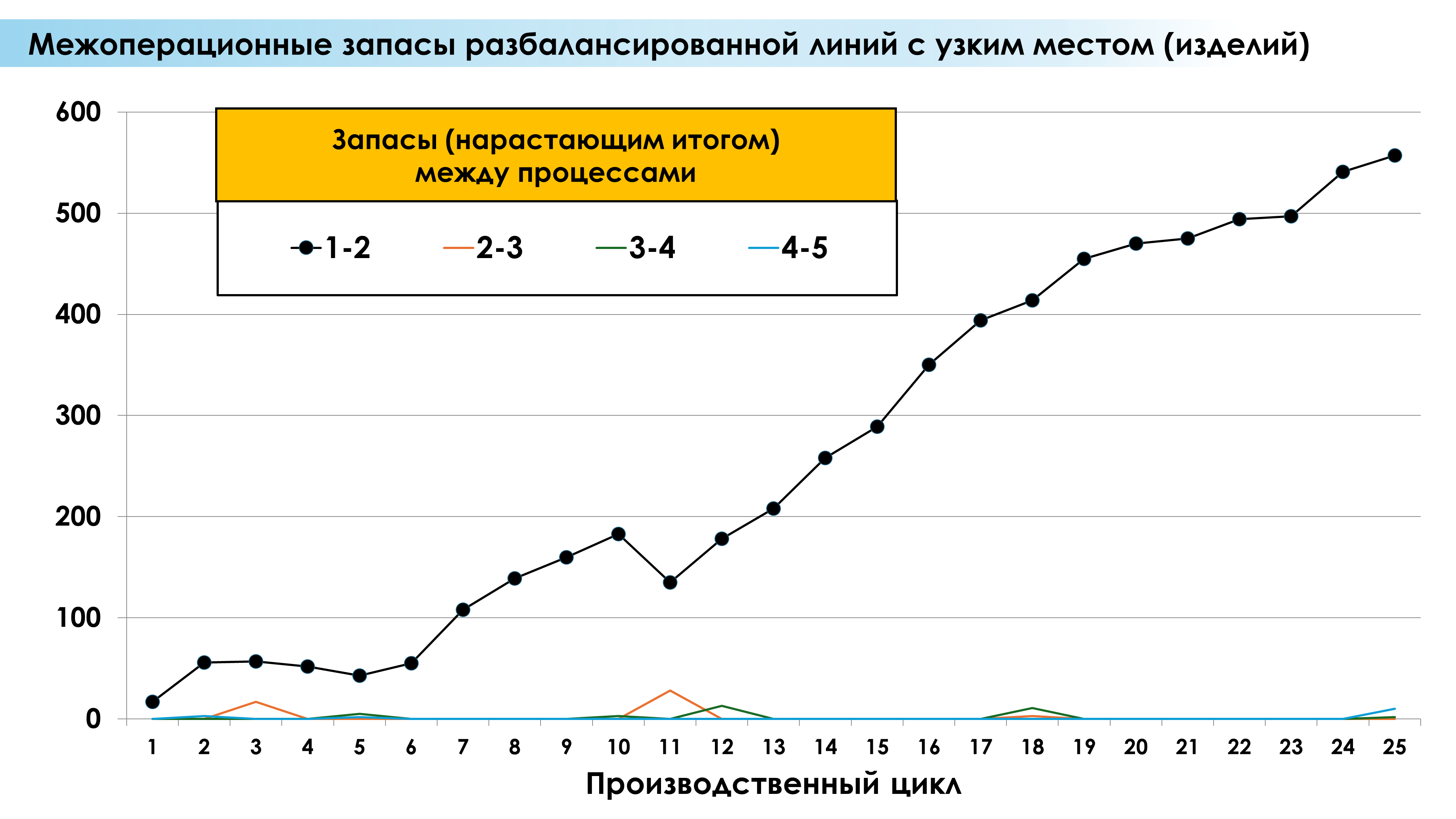
图 15. 在有瓶颈的不平衡生产线中,在瓶颈之前可互操作库存的积累图。
有意义的是,不要计划每个班次的产量,而是在基于先进先出原则的“无限”滚动生产计划中维持准备投入生产的订单(订单的活缓冲区,队列中的一些订单离开,其他订单到达)位于队列末尾)。该订单缓冲区是互操作库存。维持当前的缓冲量不低于线路瓶颈的性能控制上限,让瓶颈在任意时刻不停机运行,发挥最大性能。如果准备生产订单的过程不是瓶颈,则不需要额外的努力,因为在几个周期之后,这样的缓冲库存会以自然的方式在瓶颈前面形成。
通过控制图,您可以在报告期结束之前监控生产链中流程的统计可控性状态,以及流程绩效的好坏变化。在生产线中的工序稳定的情况下,根据每种产品的瓶颈(工序)的平均生产率来规划生产线(顺序工序链)的生产率。
您认为与 20 世纪 80 年代发展的高德拉特约束理论 (TOC) 有什么相似之处吗?休哈特控制图的开发要早得多,与 TOC 不同,休哈特控制图考虑了可预测或不可预测的过程行为,并且基于基础科学而不是判断。
以下是没有瓶颈的均衡生产线的性能示例。平衡生产线的最终性能总是略低于该生产线中任何流程的平均水平。
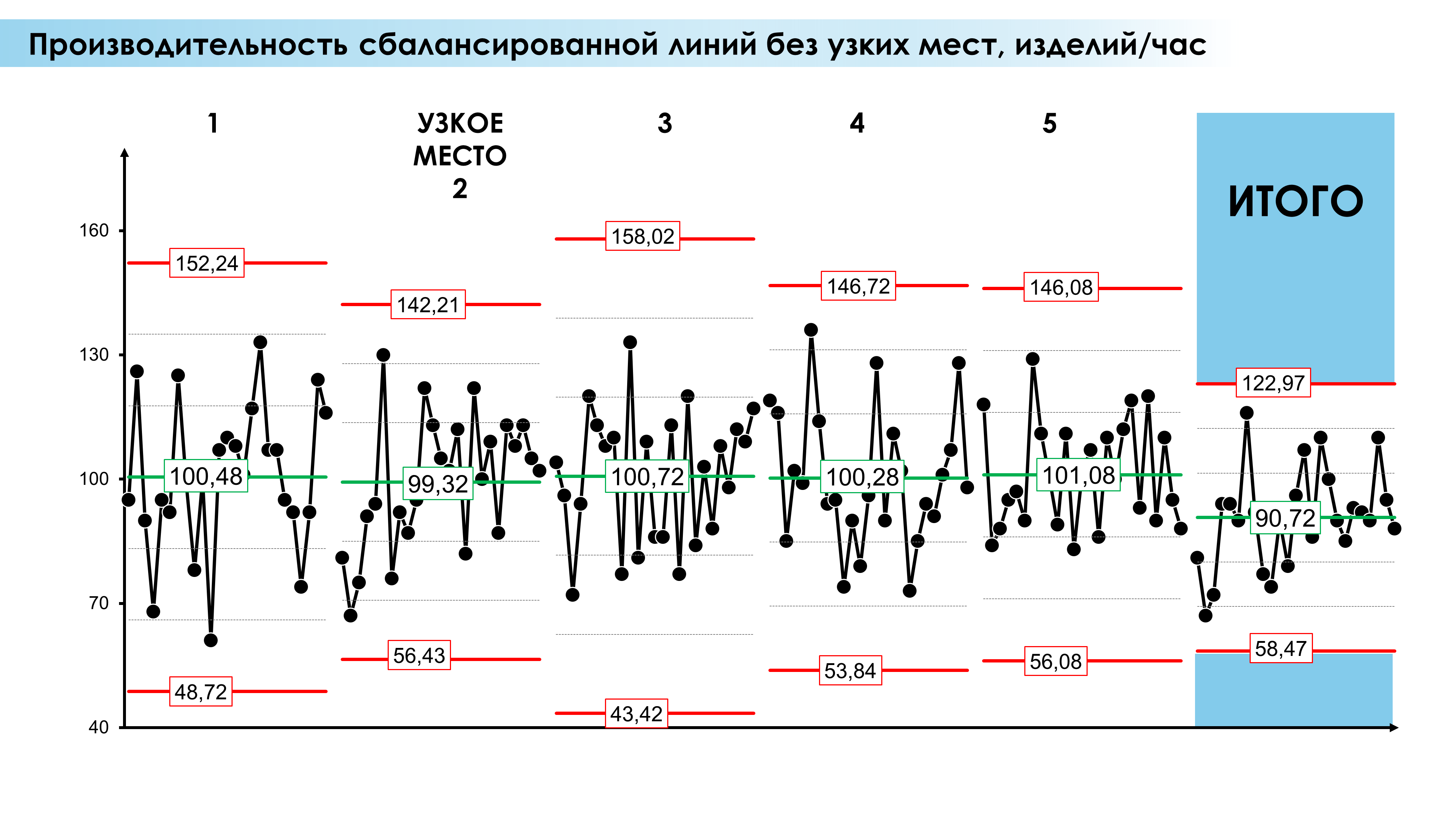
图 16. 使用 Shewhart 控制图演示的无瓶颈的平衡生产线的最终性能。分析方法,就模拟方法而言,是借用了Donald Wheeler和David Chambers的书。 “统计过程控制:使用 Shewhart 控制图进行业务优化”,第 366-370 页 [4]。绘图是使用我们开发的软件准备的 “Shewhart 控制图 PRO-Analyst +AI(适用于 Windows、Mac、Linux)” 。
平衡生产线各工序之前的工序间库存必须保持在所需水平,以防止工序停机。例如,当停止平衡生产线中的某个流程时,将互操作库存积累到高于维持此库存的流程的控制上限是没有意义的。如果所有流程稳定、连续运行,在绝大多数情况下,自然产生的少量互操作库存足以满足整条生产线的连续运行(见下图)。
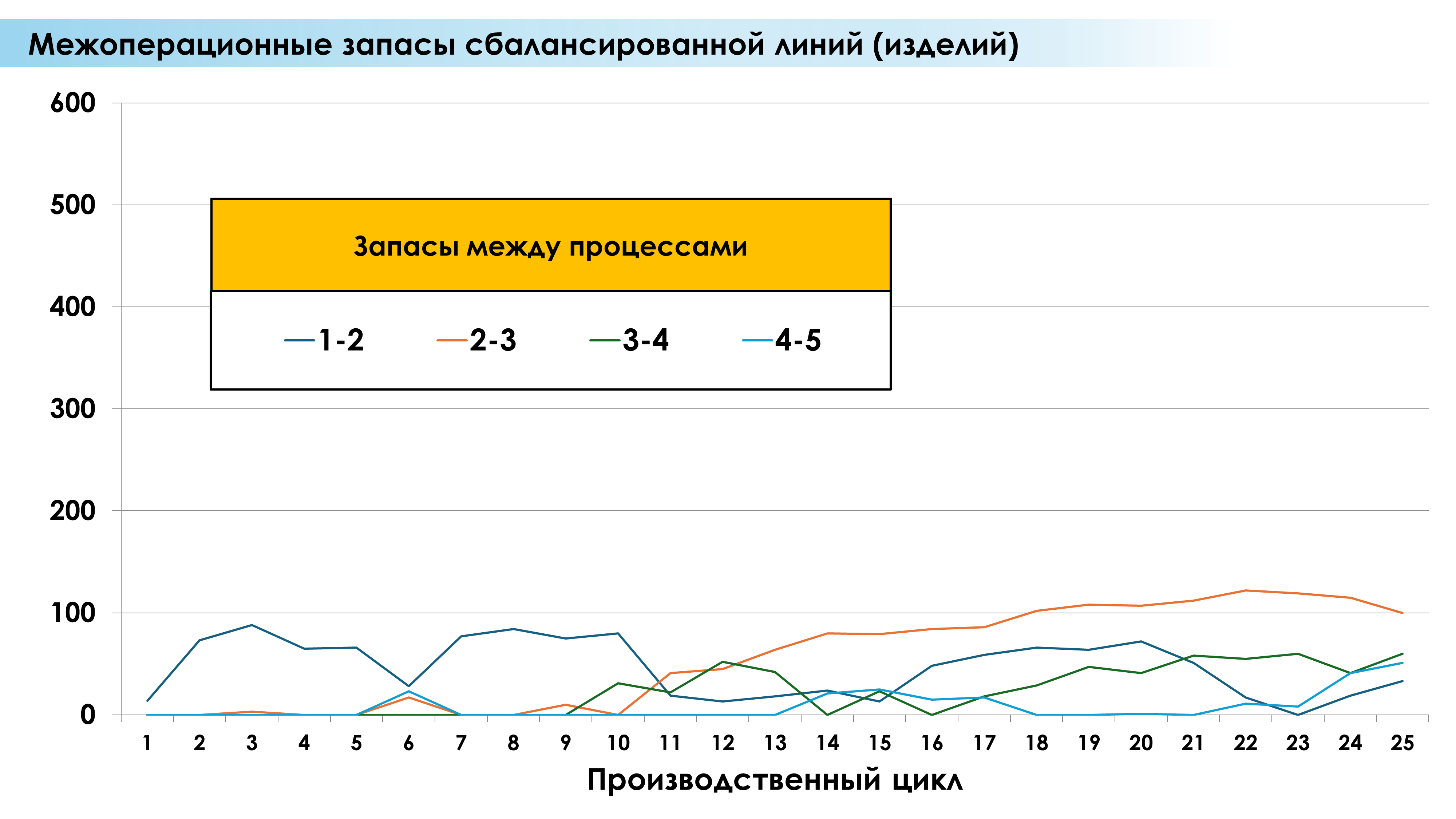
图 17. 无瓶颈的平衡生产线中可互操作的库存积累计划。
通过减少所有流程输入的可变性(提高原材料、设备和操作等的稳定性)、引入创新,不断改进所有流程。石川因果图、控制表、帕累托图、单个值的密度直方图、散点图、休哈特控制图是最好的工具。此外,休哈特控制图是最重要的工具。所有这些都将带来更准确规划的可能性。这是一项终生的工作,非常适合优化整个系统的目标。

图 18. 因果图。石川图。鱼骨架。
该过程是改善还是恶化(瓶颈)?控制图将显示均值和数据围绕均值的极差的变化(从极差控制图中很容易看出),过程中可持续变化的第一个迹象将是表明系统发生变化的信号。通过添加变化状态的 8 个新点,可以构建新的控制限来跟踪过程新状态的统计稳定性。
观看一部有关使用休哈特控制图快速诊断过程(系统)中的积极和消极变化的方法的电影。
视频 1。一种快速诊断过程(系统)变化的方法。
对于订单准备日期(计划)的初步计算,您只能使用能够证明合理程度的统计可控性(可预测性)的流程指标。例如,在不平衡生产线的批量生产中:
- 每个产品处于“瓶颈”的平均绝对印刷准备时间(绝对值,因为在绝大多数情况下,印刷准备时间不取决于批量大小);
- 每种“瓶颈”产品的单位时间平均生产率;
- 计划外瓶颈停机时间的平均值。
从技术链“瓶颈”的特定产品对应的每日总时间中,我们减去所有计划的设备停机时间(维护、修理、非工作时间等)。
按原因类型和过去时间划分的计划外停机控制图有两个目的:努力减少其数量和持续时间,以及让流程(瓶颈设备)在计划外停机方面展示合理程度的统计可控性 - 采取在计划中将它们考虑在内,从上一步剩余的工作时间中减去此类停机的平均时间。
对于剩余的工作时间,我们会根据每种产品的订单、平均准备时间和平均生产率来分配订单。根据定义,处于统计上不可控状态的过程是不可预测的;他们的平均值用于规划(预测)是不合理的。为了改进计划系统,您必须使此类流程进入统计稳定(可控)状态,然后努力减少此类流程的可变性。
重要的
重要的是要明白,生产产品的不是计划的数量(规范),而是不关心这个计划目标的流程。如果我们收集和分析数据并与车间层面(现场)的人员和流程合作,我们就会对流程和其中的人员了解很多。我们希望提高生产力 - 我们通过监控“输出”并了解问题并使用休哈特控制图进行数值可测量指标来改进流程的“输入”以及流程本身,我们根据其目标优化整个系统。

图 19. 功能建模方法 IDEF0 [16] 。