全有或全无计划反对使用表格进行随机质量验收检查。爱德华兹·戴明
“使用验收抽样检验表无法最大限度地降低进料检验的平均总成本以及允许有缺陷的材料投入生产的后果。”
引用资料来源:[2] - W. Edwards Deming,“走出危机”(“Out of the Crisis”,W. Edwards Deming - M.:Alpina Publisher,2017。科学编辑 Y. Rubanik、Y. Adler ,V.Shper)。您可以从出版商处购买该书 阿尔皮纳出版社 。
本文由 AQT 中心科学主任撰写 谢尔盖·格里戈里耶夫
免费获取文章不会以任何方式降低其中所含材料的价值。
前言
我们是否应该尝试拒绝接收的货物中的部分或全部有缺陷的物品?或者我们应该将每批产品绕过检验直接投入生产?一个经济上合理的解决方案是对爱德华兹·戴明提出的原材料、材料和部件采用“全有或全无”的控制计划。
无论如何,该公司生产的任何一件不符合要求的产品都不应到达我们的买家手中。
全有或全无输入控制规则用于最小化公司每单位生产的平均总成本。 “全有或全无”规则是一种决定对进货批次进行 100% 控制的规则,拒绝有缺陷的物料,或者在没有进货控制的情况下将该批次投入生产,然后更换和返工由于没有进料控制而通过的合格品所形成的缺陷产品的比例。
如果您对原材料、材料和部件进行进货检验以进行抽样控制,最好了解:
“如果对进料质量的统计控制程度很高,则样品的控制将无法深入了解被检验批次的其余部分,因为在这种情况下缺乏它们之间相关性的证据。”
爱德华兹·戴明的说法的实际证实是,抽样控制,例如,使用随机验收质量控制表并不能提供受控批次中缺陷产品数量的想法 用红珠子做实验 ,其中来自红色和白色珠子混合物的随机机械样本每次给出的红色珠子比例值与受控混合物中红色珠子的实际比例不同,既有较高也有较低。该实验使用相同大小样品的红色珠子数量的对照 np 图。
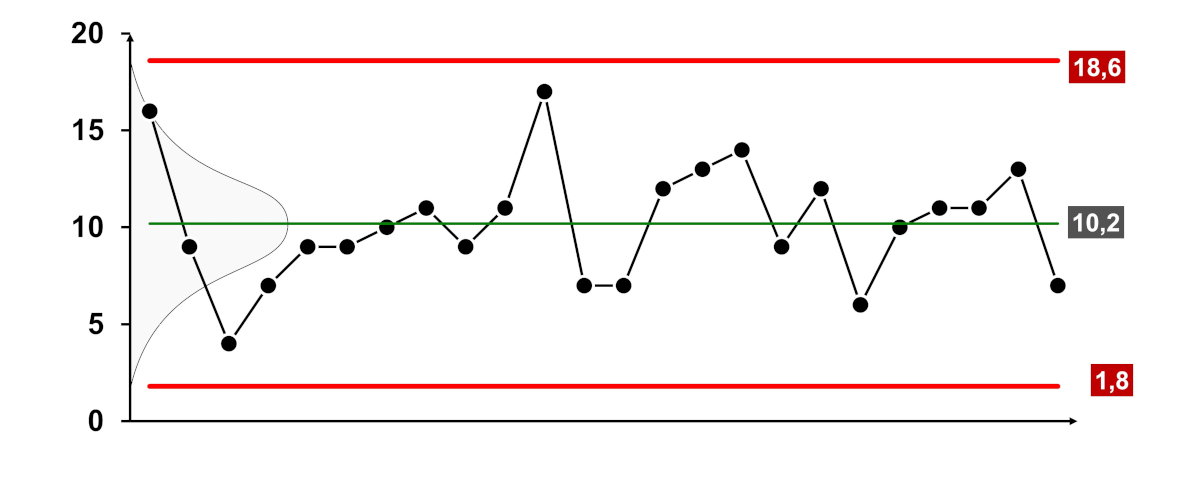
米。爱德华兹·戴明 (Edwards Deming) 于 1983 年进行的红珠实验的对照 np 图。
“在某些情况下,最小化总平均成本的规则被证明是极其简单的。
名称:
p为来料批次零件中不良品的平均比例;
k 1 - 一个零件的来料检验费用;
k 2 - 因投入生产的一个有缺陷的部件而出现故障的装置的拆卸、修理、重新组装和重新测试的成本。
条件一:
最差的进货批次的平均缺陷率 (p) 小于 (k 1 /k 2 )。
p<k 1 /k 2
在这种情况下:无输入控制。必须完全依赖于组件测试时的检查。
谢尔盖·P·格里戈里耶夫(Sergey P. Grigoryev)的解释:
公式条件1的推导,当纠正来料批次中所有有缺陷部件的单元的总成本(N×p×k 2 )将低于检查所有 100% 来料零件的成本 (N×k 1 )。
(N) - 传入零件批次的尺寸(件数)以及缺陷零件的比例 (p):
N×p×k 2 <N×k 1
将表达式简化为:
p×k 2 <k 1
然后:
p<k 1 /k 2
条件2:
最好的进货批次的缺陷品比例 (p) 大于 (k 1 /k 2 )。
p>k 1 /k 2
在这种情况下:100% 输入控制。并对成品检验点进行控制。
谢尔盖·P·格里戈里耶夫(Sergey P. Grigoryev)的解释:
公式条件 2 的推导,当纠正来料批次中所有有缺陷部件的单元的总成本 (N×p×k 2 )将大于检查所有 100% 来料零件的成本 (N×k 1 )。
(N) - 传入零件批次的尺寸(件数)以及缺陷零件的比例 (p):
N×p×k 2 >N×k 1
将表达式简化为:
p×k 2 >k 1
然后:
p>k 1 /k 2
(k 1 /k 2 ) - 平衡质量,或平衡点。
(k 2 ) 总是更大 (k 1 );
因此,比率 (k 1 /k 2 ) 将位于 0 和 1 之间。
如果在应该应用条件 1 规则的情况下应用条件 2 规则,则总成本将最大。反之亦然。”
示例(谢尔盖·P·格里戈里耶夫)
鉴于:
p(进货零件批次中缺陷品的平均比例)= 0.05;
k 1 (一件零件来料检验费用)=100.00₽;
k 2 (由于投入生产的一个缺陷部件而导致故障的装置的拆卸、修理、重新组装和重新测试的成本)= 1,000.00 ₽;
输入批次 = 1,000.00 件。
条件1:p<k 1 /k 2 - 没有进入控制。
条件2:p>k 1 /k 2 - 100% 传入控制。
计算
p = 0.05
k 1 /k 2 = 100.00 ₽ / 1,000.00 ₽ = 0.10
0.05 < 0.10
p<k 1 /k 2 - 对应于条件 1 - 无输入控制。
解决方案
选择“无控制”计划。
检查解决方案
入口处 100% 控制的成本为:
1,000 个×100.00 ₽=100,000.00 ₽
通过缺陷材料的成本为:
1,000个×0.05×1000.00 RUR=50,000.00 RUR
因此,在这种情况下,允许有缺陷的零件投入生产,随后对因一个有缺陷的零件进入生产而失败的单元进行后续拆卸、维修、重新组装和测试,实际上将比 100% 来料检验少花费 50,000.00 美元₽。
“因此,统计控制的状态具有明显的优势。要知道传入的批次流是否满足条件1或条件2,或者处于接近混乱的状态,只需使用建立的图表来跟踪统计控制和平均不良率基于正在进行的小样本试验(在任何情况下),最好与供应商合作并在供应商的场所进行。”
实践中观察到的其他条件(爱德华兹·戴明)
分布的中间位置,与统计可控性有中等偏差。
现在,我们将分析两种类型的中间情况,以了解来料批次中缺陷品比例的分布。也许,使用我们自己的控制图,或供应商的图表,或共同维护的图表,我们可以预测只有一小部分分布会落在平衡点的右侧。对于这种情况,我们可以采取“无控制”规则。这条规则将使我们能够接近平均总成本的最小值,前提是位于平衡点右侧的分布部分很小。
相反的情况:进货批次中缺陷产品比例的分布只有一小部分位于平衡点的左侧。了解了这一点,您就可以放心地接受 100% 控制进货批次的规则。
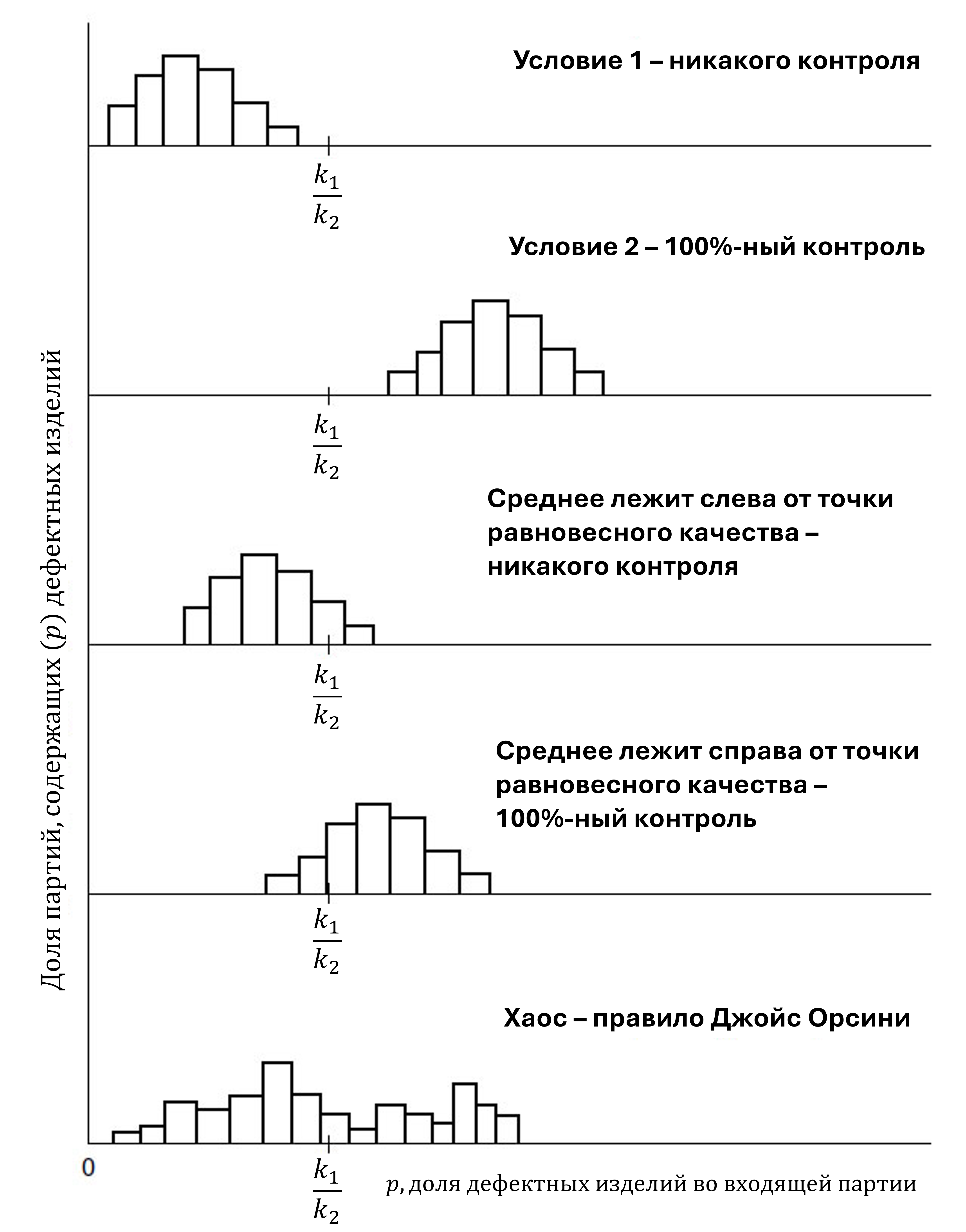
米。 1、批量接收来料时可能出现的情况。
B 点是平衡质量点,此时 p = k
1
/k
2
。来源:
[2]
爱德华兹·戴明《走出危机》
来料批次中缺陷产品的比例趋势
让我们假设缺陷产品比例已形成增加的趋势。今天我们处于条件 1 并且无法控制,但是 (p) 与时间相关并且可能以恒定速率或可能不规则地增加。两天后我们将进入条件 2 区域:我们已收到警告。供应商或我们的控制图将揭示一种趋势(如果存在)。这个问题很容易解决。
不同供应商切换带来的问题
由于系统输入的材料来源发生变化,总是会出现问题。让我们只考虑两个来源。如果两个源都受到良好或中等的统计控制并且可以彼此分离,则原则上每个源都满足条件 1 或条件 2,具体取决于该源的均值是落在平衡点的左侧还是右侧。这个想法说起来很简单,但在一些工厂中可能很难实施。
如果来自两个来源的材料以恒定比例均匀混合,并且如果两个来源都表现出足够的统计控制,则混合批次可以被视为二项式混合物,其最小平均控制成本可以使用全或无来实现规则。
来自两个来源的材料给生产带来了额外的问题。对于制造经理来说,来自两个来源的材料的均匀混合物是最糟糕的情况。
第一步是将供应商数量减少到一个。如果单一来源提供的产品质量参差不齐,那么供应商和客户必须共同努力改进它,旨在满足条件1并最终实现零缺陷。
混乱状态
在分布位置波动稍微接近或远离平衡点的情况下决定该怎么做相对容易。
在平衡点附近,我们是否有 100% 的控制或根本没有控制并不重要。我会选择100%控制来尽快收集信息。如果我们不能断言进料质量主要位于平衡点的右侧或左侧,而是相反地大幅波动,穿过平衡质量点,那么我们就处于混乱状态。
1. 当从单一来源提供具有高度可变性和不可预测质量的材料时,可能会出现这种不可接受的情况。
2. 平衡质量点附近的这种变化可能是由于从两个或多个质量差异很大的来源获取材料造成的。在这种情况下,从一个源到另一个源的切换是无法控制的,没有经过深思熟虑的顺序。我们应该尽快摆脱这种状态,转向条件 1。但是批次不断到来,我们必须对它们做一些事情。我们该如何对待他们呢?
如果每批产品都附有标签,告诉我们其中缺陷品的比例,那就没有问题了。我们可以通过将每个批次一个接一个地放置在平衡点的右侧或左侧并在批次之间应用“全有或全无”规则来实现最小平均总成本。
但批次没有标注。然而,在混乱状态下,样品中的产品质量与批次中的其他产品的质量之间存在一定的相关性。因此,在混乱的状态下,您可以测试样品,并使用一些规则来决定是将剩余部件完全投入生产还是拒绝它。
抽样,无论使用得多么好,都会导致一些批次最终出现在平衡点的错误一侧,从而导致错误识别批次的总成本最大化。
在混乱的状态下,人们可能倾向于 100% 的控制。这个决定有一定道理。
永远不会失去信息
不准入管制的规定并不意味着在黑暗中开车时要关闭前灯。应审查所有进货材料(可能跳过一些批次)以获取信息并将实际交货与供应商的装运单、供应商测试的检查以及随附的控制图进行比较。如果有两个供应商,请分别保存每个供应商的记录。
下一个建议是为每种产品寻找一个基于长期合作关系的供应商,并与他们合作提高进货质量。
破坏性测试
先前的理论基于原型的无损测试。有些测试是破坏性的;他们销毁受控样本。例如,灯泡的寿命、燃烧一立方英尺气体产生的热热量、保险丝的工作时间或测试一块布的羊毛含量。拒绝整个批次是没有意义的,因为没有任何东西可以转移到生产中。
显然,对于破坏性测试,唯一的解决方案是在零件的生产中实现统计控制状态,以便立即正确地制造它们。该解决方案最适合破坏性和非破坏性测试。
许多零件组装可能存在缺陷
在前面的部分中,我们讨论了由一个部件组成的简单产品。有些零件可能需要 100% 检查,以最大限度地降低总体成本。一旦经过测试,它们不会导致装配(assemblies)失败。其余部件将不会进行测试,有缺陷的部件如果进入生产,将导致故障。假设我们有两个未经测试的部分。
两个未经测试的零件存在缺陷 1 和 p 1 。那么组装失败的概率将等于:
普罗 (会拒绝) = 1 – Pr (不会拒绝) = 1 – (1 – p 1 )(1 – p 2 ) = p 1 +p 2 -p 1 p 2
如果两个 p 值 1 和 p 2 -小,那么这个概率将接近该值:
普罗 (会拒绝) = p 1 +p 2
写出任意数量零件的故障概率的一个简单方法是使用维恩图(在任何概率论书籍中都有描述)。
前提是所有p 我 小的。推广到 m 部分可得出:
普罗 (会拒绝) = p 1 +p 2 + … + p 米
因此,故障概率随着零件数量的增加而增加。一台收音机可能有 300 个零件,尽管这个数字取决于你如何计算它们。一辆车可能有 10,000 个零件,这同样取决于您的计数方式。汽车里的收音机是1零件还是300零件?燃油泵是1部分还是7部分?无论您怎么想,单个组件中的零件数量可能会令人难以承受。
` 但是还有另一个问题:k 2 (纠正有缺陷的组件的成本)随着零件数量的增加而增加。当装配失败时,哪个部件有问题?这很容易误诊。此外,两个部件中的两个部件都可能有缺陷。
对于由多个部件组成的产品:
1.我们可以只允许少数部分满足条件2(100%控制);否则控制成本将会过高。
2. 对于其他零件,只有接近零缺陷的质量才是可接受的。
由复杂组件组成的组件
创建辅助子系统时可能节省费用。在前面的理论中,成本k 2 通常会随着流程的每个步骤而增加(可能增加 10 倍),并且在最终组装期间可以达到非常高的值。有时,通过创建沿着组装流程移动并形成最终产品的子系统,可以避免不必要的高成本。一些子系统已经通过控制,需要进行较小的更换和调整,形成新的起点。成本k 2 现在将是监控和调整子系统的成本。理论加上有用的经验记录可以表明,某些子系统根本不需要测试,而其他子系统则应受到 100% 的控制,以避免随着流程的进展成本增加。本章介绍的理论可以帮助您做出正确的决定。
我们前面几节的目标是表明,如果遵循正确的理论,就有一些方法可以最小化成本并最大化利润。
同时,我们尽一切努力从过程中彻底消除缺陷产品。我们通过将我们的测试结果与供应商的测试结果进行比较并应用适当的统计方法(例如 X 图和 R 图(休哈特控制图))来系统地做到这一点。
与零部件供应商(尤其是关键零部件供应商)的富有成效的合作,以及子系统的成功测试和调整,将系统最终检查期间的所有重大问题减少为罕见事件。
进料是供应商的副产品
当供应商的客户关键材料可能是副产品时,占其业务的比例不到 1%。不能指望供应商承担安装设备以改进产品的成本和风险。
一个可能的建议是将这种材料视为铁矿石或其他高度可变且未经纯化的投入。安装您自己的材料清洁系统或使用第三方公司的服务。这个计划在某些情况下是有效的。
检测罕见缺陷的困难
罕见的缺陷很难被发现。随着缺陷产品比例的降低,确定缺陷数量到底有多大变得越来越困难。使用检查不可能检测到所有缺陷,尤其是当缺陷很少时,目视检查和自动检查都是如此。与声称 5,000 种产品中只有 1 种缺陷的制造商相比,没有理由相信声称 10,000 种产品中只有 1 种缺陷的制造商。在这两种情况下,这个比例都很难估计。
因此,如果 (p) 等于 1/5000 并且过程处于统计控制状态,则必须检查 80,000 个零件才能发现 16 个有缺陷的零件。
谢尔盖·格里戈里耶夫:
5000×16=80000
这些数据可以估计标准误差为 σ = √16 = 4 的生产过程的平均缺陷率 p = 1/5000。尽管难以监控大量缺陷,但这种缺陷率的估计并不精确。 80,000 个零件。问题出现了:在 80,000 个零件的生产过程中,工艺是否保持稳定?如果不是的话,16个不良品是什么意思?很难回答的问题。
谢尔盖·格里戈里耶夫:
在这种情况下,如果供应商的过程处于统计控制状态,则假设以 80,000 个零件大小的子组形式的批次的平均值 c = 16 个缺陷左右运行,其值上限 (VKG , UCL) 和下限 (NKG, LCL) 控制限 C- 图表:UCL, LCL = c ±3σ 或 UCL, LCL = c ±3√c,这会导致值在平均值周围分布 (c=16) ±12以内。
公式可在 GOST R ISO 7870-1-2011 (ISO 7870-1:2007)、GOST R ISO 7870-2-2015 (ISO 7870-2:2013) - 统计方法中找到。休哈特控制图 [十一] 。
为了计算 (σ),Deming 使用 C 图表,其中每个恒定定义区域的缺陷数量等于 80,000 个零件。
为什么是16?平均值 (16) 可以轻松计算 C 图表的 (σ) 值,并提供控制下限和上限。
因此,对于供应商来说,要声称这样的缺陷率(1/5000)需要了解其生产过程的稳定性,这只能使用休哈特控制图来确认,并且控制图必须构建,例如,在至少八个点,其中每个点是每批 80,000 个零件的缺陷数,可能的整数值从 4 到 28 个缺陷分布 经验法则 平均水平为:每批次 80,000 个零件有 16 个缺陷。
为什么对于 5000 个零件的恒定定义域,缺陷平均值 c = 1 无法执行这些简单的数学运算?是的,因为您将无法从控制图上低于平均值 c=1 的缺陷数整数中获得分数(零除外)。虽然在数学上很容易在计算中得到小数,例如 = 0.3,但您如何想象在实际情况下获得测试批次(子组)中缺陷数为 0.3 的可能性?
有的例子是,数百万个零件没有一个故障,或者数量很少,或者100亿个零件缺失。当缺陷产品的比例如此之低时,对成品的控制将无助于获得所需的信息。了解在如此极端的要求下发生的情况的唯一可能方法是使用控制图以及过程中对零件的实际测量。一百个观察值(例如每天 25 次连续观察 4 个项目)将为子组均值和极差的 X 和 R 图表生成 25 个样本点。休哈特控制图将显示过程是否按原样进行,或者是否在某个地方发生了故障,并且必须停止许多产品的生产,直到找到原因。一旦找到原因,您可以决定在一段时间内拒绝整套产品或跳过某些产品。 XbarR 平均值和极差子组控制图的不断增强的功能变得越来越明显。
谢尔盖·P·格里戈里耶夫(Sergey P. Grigoryev):文章中的唐纳德·惠勒(Donald Wheeler) 替代数据(计数)p 图、np 图、C 图和 u 图或单个值的 XmR 图的控制图? 强化了爱德华兹·戴明的这一建议:
“由于在可以获得测量结果时使用离散量(计数)几乎没有意义,因此属性的使用通常仅限于可以计算“错误”的情况。然而,定义“错误”通常会带来很大的困难。定义“blooper”的主要困难是一个问题 操作定义 ”。
使用预订
有时,在设计复杂设备时,将两个或多个部件并联放置是可能且合理的,这样如果其中一个部件发生故障,另一个部件将自动接管其功能。两个平行部件,每个部件的平均缺陷率为 p 我 ,相当于平均缺陷率等于 p 我 ².例如,如果 p 我 =1/1000,则 p 我 ²=1/1000000。
当然,重量和尺寸限制可能会妨碍冗余的使用。
还有其他问题:备份部分在需要时能工作吗?也许最好的解决方案是单个部件的高可靠性。
结论
制造过程中不允许出现有缺陷的材料和工艺。上述理论告诉我们,在生产的任何阶段都不容忍有缺陷的材料是多么重要。一次操作的产品是下一次操作的输入材料。有缺陷的材料一旦生产出来,就会一直存在缺陷,直到缺陷被发现为止,幸运的是,在以后的测试中,然而,纠正和更换的成本并不便宜。
统计可控状态具有明显优势。要了解传入的批次流是否满足条件 1 或条件 2,还是处于接近混乱的状态,只需使用由小样本的持续测试构建的休哈特控制图来监控统计控制和缺陷品的平均百分比(如任何情况),最好与供应商合作并在其领土上进行。
例外情况
许多输入材料并不遵循上述理论。例如,用空气软管搅拌后的一罐甲醇。从储罐的几乎任何部分采集的甲醇样品几乎都是相同的。然而,化工公司对甲醇进行多个级别的采样。也许更接近的例子是品尝一杯杜松子酒或威士忌。我们一致认为,从哪里取出部分并不重要:从顶部、从瓶子中间或从底部。
解释 Sergey P. Grigoryev:以上段落指的是样品控制结果可归因于整个批次的特殊情况。
高炉加热会产生问题,这是本章理论不适用的另一个例子。加热不均匀。一些公司从每个装瓶中抽取少量样品。如果对这些样本进行分析,可以为流程图提供数据,该流程图可以显示从第一次到最后一次铸造的质量变化,从而提供改进的线索。
Sergey P. Grigoryev 的解释:上一段涉及特殊情况,根据定义,过程在过程的不同阶段是异构的,并且可以从每个阶段抽取一个样本;在这种情况下,为了分析不同批次(铸件)之间的差异,有必要使用单个值的对照 XMR 图。
查看开源解决方案: 使用表格进行随机验收质量控制的问题 。