如果不将统计控制方法集成到自动化过程控制系统、自动化控制系统和数据管理系统、自动化控制系统、自动化控制系统中,您将增加在控制工艺过程时所犯的第一类和第二类错误的数量。
材料准备者:AQT 中心科学主任 谢尔盖·格里戈里耶夫 。
免费访问文章并不会以任何方式降低其中包含的材料的价值。
自动化过程控制系统或自动调节器的操作员在尝试控制过程时,经常犯第一类和第二类错误,不了解如何区分噪声和信号,从而降低了受控过程的经济效益并增加了紧急事件的可能性。
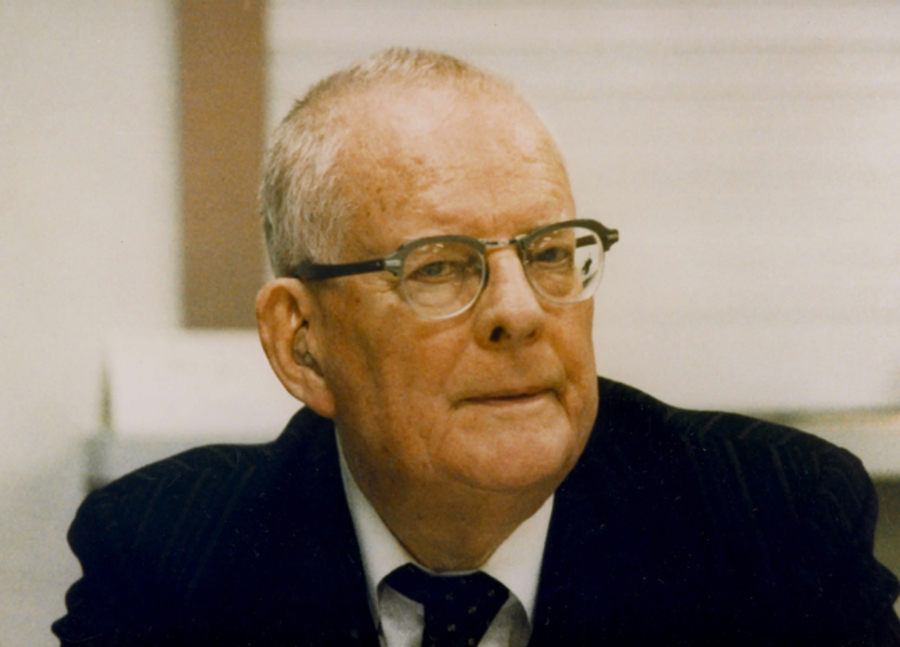
“知识是无可替代的。但使用知识的前景令人恐惧。”
西门子、GE等公司的过程控制系统和自动化控制系统软件产品已经采用集成的统计过程控制模块(分离自然过程变异性和特殊原因引起的非自然变异性),其主要工具是休哈特控制图。但这些公司也没有注意到上游过程控制统计方法的主要优势,仅在最终的多因素生产过程的质量控制模块中使用它们。
任何聚合指标(结果)都隐藏了可变性数据源中的信号,将它们转化为结果级别的噪音,从而使工作人员无法首先了解需要采取哪些措施来改进流程。同时,自动化过程控制系统或自动控制器的操作员对噪声的任何反应行为都是第一类错误,这只会让情况变得更糟。重要的是要理解,在高水平的聚合下,只有灾难性的变化才会以信号的形式被注意到(爱德华兹·戴明)。
“上游搜索是解决混合问题的强大杠杆。”
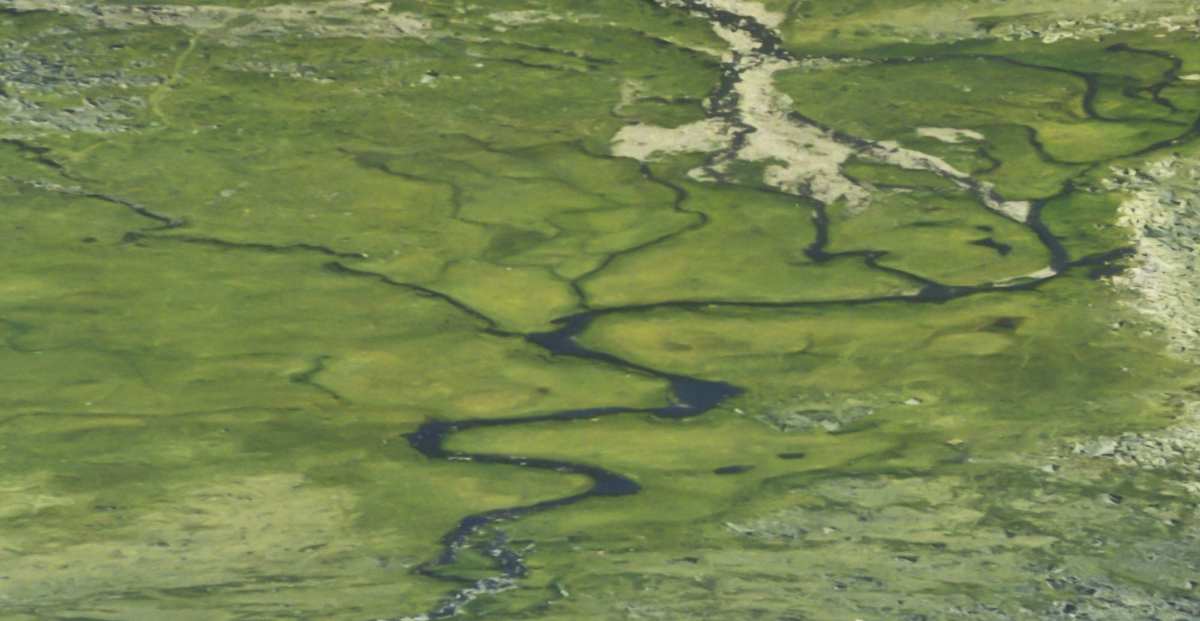
图 1. 上游搜索是解决混合问题的强大杠杆。
查找和消除技术过程失控(脱离统计控制状态)的特殊原因的系统助手应该是在操作员界面中直观地显示因果关系的所有已识别元素的控制图。此外,可以根据来自传感器的数据和来自在线记录事件的其他子系统的数据(例如,原材料的进货质量控制、测试实验室的数据)来评估原因(因素)监测指标的统计可控性状态。和互操作控制)。
此外,统计控制方法可以识别过程控制系统未监控但显着影响技术过程的变异量和稳定性的因素(变异的一般和特殊原因)的存在。这些因素必须在操作上进行定义,必须为它们分配过程控制系统中的控制指标。
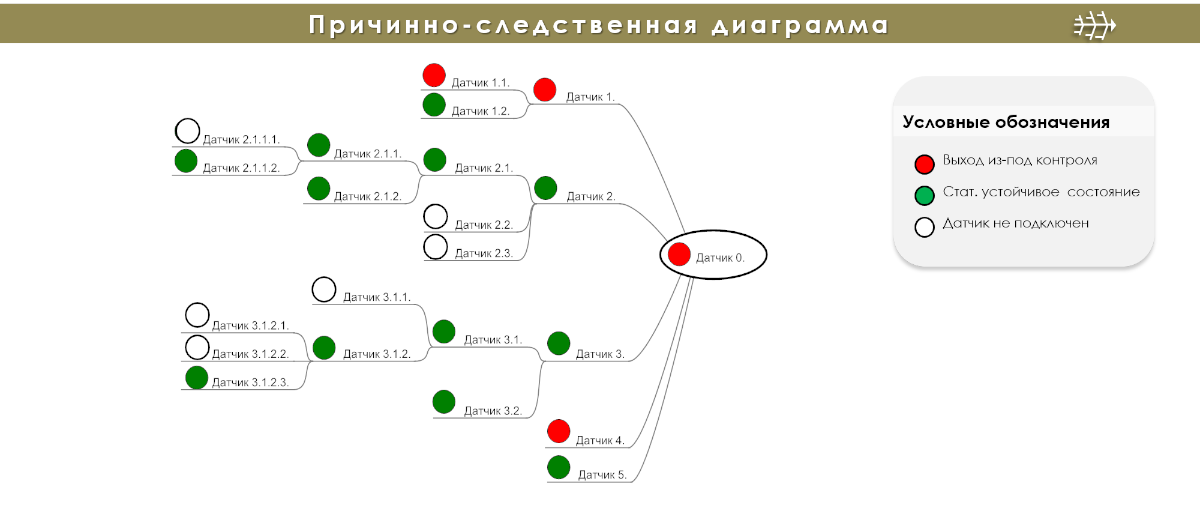
图 2. 自动化过程控制系统传感器生成的数据的因果关系。无论达到警告或紧急限制的程度如何,指示过程从统计稳定状态退出的点均显示为红色。
工业中使用的绝大多数工艺过程和公用网络自动化控制系统(APCS、ASUB、SMUS、ASUiD、过程控制系统)都没有配备用于统计过程控制(统计过程控制,SPC)的软件和分析模块,并且操作人员没有接受过这些管理技术的培训。
这导致操作员在尝试管理流程时不断地做出 第一类和第二类错误 ,不了解如何区分统计控制过程的自然变异(噪声)和非自然变异(信号),后者是由于特殊原因影响过程失控造成的。
如果应用得当,休哈特控制图可以准确地从信号中分离出噪声,从而揭示设备和过程故障的单独特征,而无需设置虚构的边界值。例如,专门提供 DSS 来监控和优化高价值资产的 OSyS(优化系统和解决方案,劳斯莱斯子公司)报告了一个表明缺乏此类知识的问题:
“在分析性能参数时,OSyS 专家面临这样一个事实:要么将阈值设置得太窄,然后警报数量会急剧增加,要么将值设置得太宽,结果发现警报中的值没有达到所需的限制,但是技术工具、知识和分析技能帮助他们为来自设备的各种数据流创建了故障签名。 ”
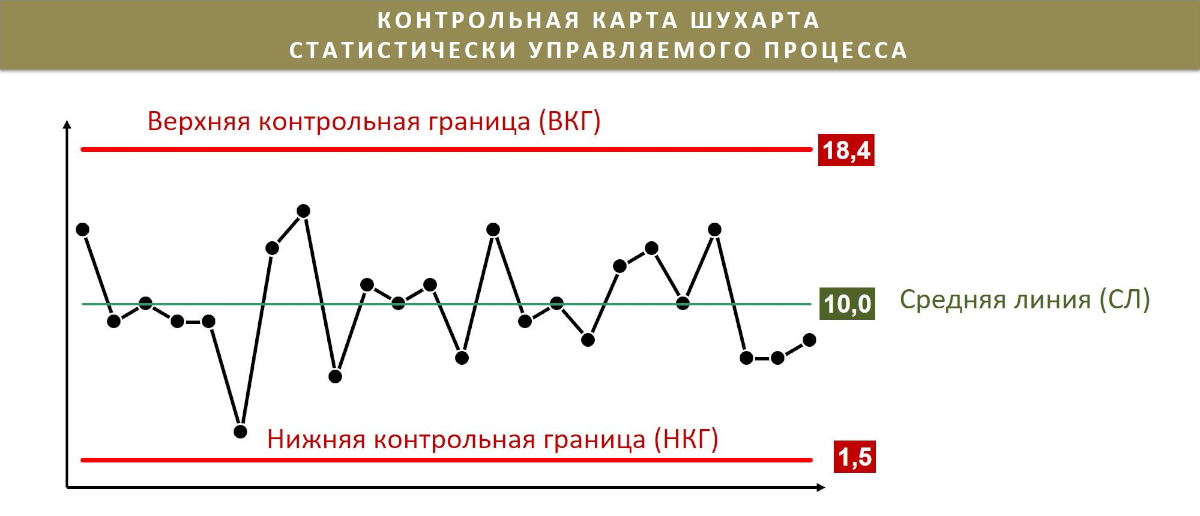
图 3. НКГ 和 НКГ - 通过分析过程的历史数据及其固有的可变性计算得出的控制上限和下限。文献:有关构建 Shewhart 控制图的规则,请参阅 GOST R 50779.42-99 (ISO 8258-91) - [11.1] 统计方法。休哈特控制图。
第一类错误(过度调节),见图 4,表现为对处于统计控制状态的过程进行持续手动或自动干预,并根据规则进行调节:2、3 和 4当达到紧急极限(调节开始极限、极限值)时,用漏斗进行实验。本质上,它就像响应信号一样响应数据中的噪声。休哈特控制图范围内的点是同质的,并且彼此没有差异,尽管这些数据的含义存在明显差异,除非这些点超出控制范围或形成结构,表明存在特殊的变异原因。定义数据中此类结构的规则通常称为 西部电气区域标准 。
如果过程的生存空间允许这样或如果过程的生存空间受到这些边界的限制,则数据的分布在自动响应的边界内接近均匀,这对观察者隐藏了过程的自然本质,这意味着改进此类过程的可能性显着降低。
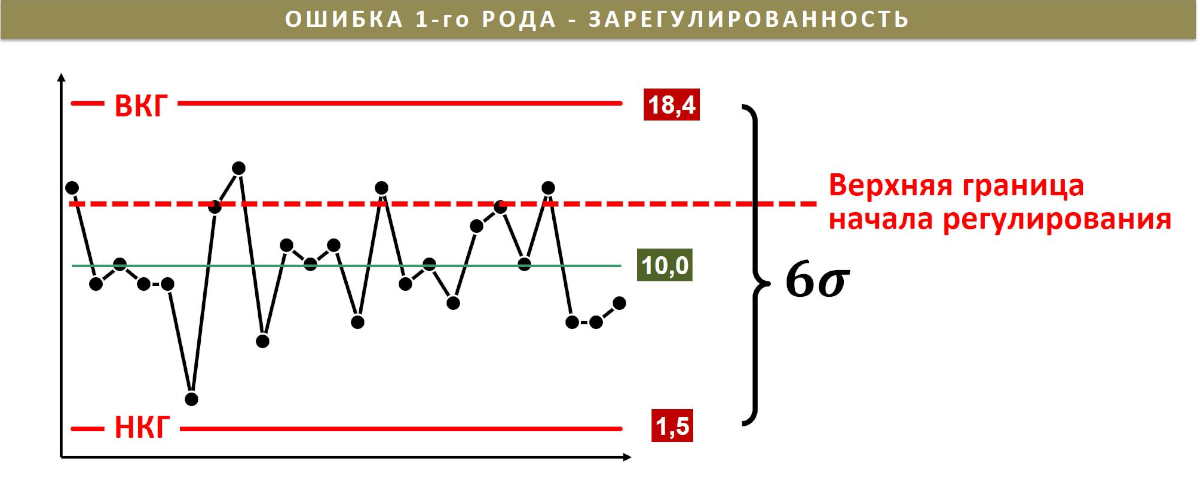
图 4. 第一类错误 - 过度监管。操作员或自动化调节开始的限制位于过程的控制限制内。
第二种类型的错误,参见图 5,在于当过程离开统计可控状态(变得不可预测)时,操作员不采取行动(对正在进行的过程控制不足),但仍未超过为以下情况建立的最大容差限制:它是紧急限制(监管开始的限制、限制数量)。第二种类型的错误是对处于统计上不可控状态的过程的潜在能力的任何推理。
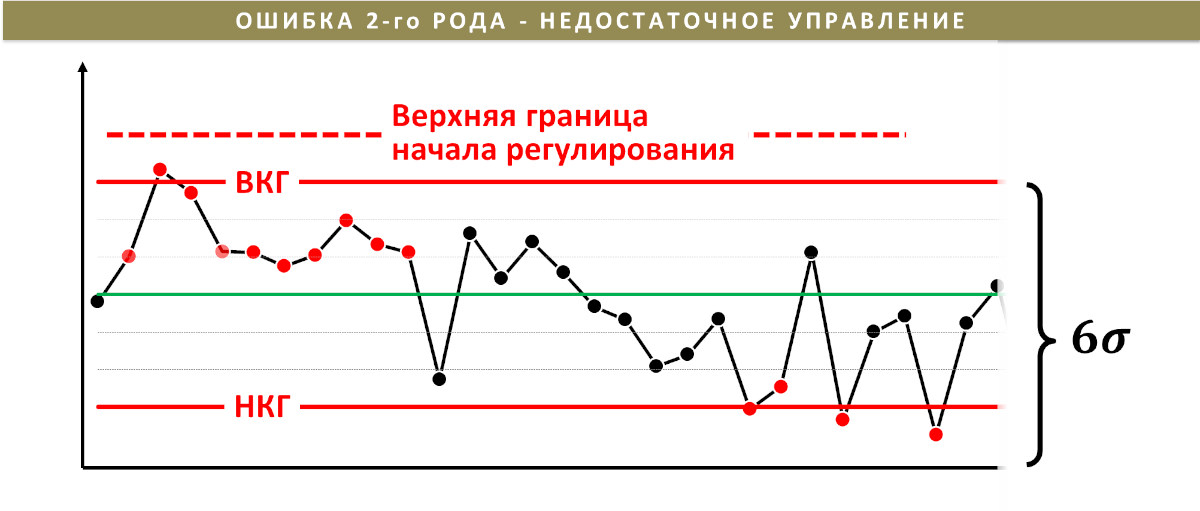
图 5. 第二种错误 - 控制不足(不作为)。操作员或自动化调节开始的限制位于过程控制限制之外(高于或低于)。这个过程已经失控,但没有人对此做出反应。
经典自动控制在自动化过程控制系统中的应用,PID控制器( 比例积分微分控制器 ),忽略了有关任何技术过程的可变性的知识,并且没有解决第一类和第二类错误的问题。使用这种自动调节器或手动过程控制只能对处于统计上不可控状态的过程有效,见图 5。但最有可能的是,由于自动化过程控制系统的设计者和由于技术人员缺乏必要的知识,在该过程达到监管限制之前不会应用必要的监管。
不知道如何最小化犯第一类和第二类错误的风险会导致损失,有时甚至会造成严重后果。
文章中描述了第一种类型的更实际的错误: 可变性和过程控制的概念 ,作者 Netsvetaev A. G.、Rubanik Yu。 T.,米哈尔琴科 V.V.
为了对过程进行操作诊断(统计可控性、可预测性分析)并对其采取必要措施,避免第一类和第二类错误,可以使用自动或手动收集的任何工艺过程的“语音”数据:
- 任何关键绩效指标、采购效率、销售、设计、设备维护等;
- 有关来料 C&M 控制、供应商质量管理、自有半成品和产品质量的数据;
- 事件发生频率(事件、事件)、任何计数数据(缺陷、故障、计划外停机等);
- 有关尺寸、重量、间隙、流量、液位、振动(振动诊断)、压力、温度、湿度、气体分析、位置、速度、力、粘度、密度、硬度、放射性、照明、灰尘含量、浓度的数据,杂质的存在和数量、摩擦诊断、酸度、污染、声学测量、电学测量和其他测量。
托木斯克理工大学教育手册“灵活自动化生产控制系统设计”的第[15]章专门介绍了自动化控制系统在使用休哈特控制图对技术设备状态进行操作诊断中的任务。
结论
不要忽视可变性的本质。将统计过程控制(Statistical Process Control,SPC)的智能方法集成到自动化过程控制系统和自动化控制系统中。