使用公差字段的正确和错误方法。是否应该根据缺陷和良品的容差对产品进行分类,还是应该尝试定制流程?
文章:[26] DONALD J. WHEELER:“使用规格的正确和错误方法。排序还是调整?”
翻译、注释和附加图形材料及解释:AQT 中心科学主任
谢尔盖·格里戈里耶夫
,使用唐纳德·惠勒善意提供给他的材料。
免费获取文章不会以任何方式降低其中所含材料的价值。
在本文中,我们将了解公差字段的历史和用途,并了解在实践中使用它们的两种常见方法。我将通过简单的例子来说明使用公差字段(规格)的正确和错误方法。
注:Sergey P. Grigoryev:本文清楚地表明,机器操作员相对于公差范围对流程进行的操作调整仅对于不稳定和/或不在公差范围内居中的流程才有意义,而稳定和不居中的流程则有意义。公差领域中的中心化流程会导致更大的变异性(数据围绕平均值的分布更大),从而使工作人员无法理解“正在发生什么?”当他试图提高他生产的零件的质量时。
客户之声
大约 220 年前,Eli Whitney 发明了带有可更换部件的轧棉机。可互换零件的使用是当时的技术突破。在轧棉机取得成功后不久,惠特尼就收到了一份为美国陆军提供具有可互换零件的步枪的合同。在尝试生产大量零件以便它们可以互换使用时,他立即发现了一个事实,此后一直困扰着每一次生产:没有两件东西是相同的。
因此,他们必须满足于让事物变得相似,而不是让事物变得相同。一旦他们接受了这一点,问题立即出现:“足够相似的部分有多相似?”为了回答这个问题,创建了技术条件(公差范围、规格)。很明显,微小的偏差是可以容忍的,因为部件仍然可以发挥作用。然而,随着变化的增加,终有一天,丢弃该部件会比尝试使用它更便宜。容差范围(规格)旨在确定该损耗截止点。
200年前,大规模生产的经济规模非常大,可以容忍大量的浪费。到 1840 年代,量具(通过/失败)工具被发明。到了 1860 年代,这已演变为“go-no-go 量规”,可以将大量零件经济地分类为好零件和坏零件。这项 1860 年代的技术至今仍在使用。创建公差字段是为了将可接受的产品与不可接受的产品分开。每当产品流包含可通过无损检测识别的不合格元素时,如果能够以经济可行的方式完成,则使用 100% 测试仍然是一个合理的策略。吐司烤焦后,除了清理烧焦的碎片之外,还能做什么呢?
例子
图 1 和图 2 显示了 100 个最终测试值及其直方图和各个值的 Shewhart X-map。这些值来自我客户工厂之一的制造操作。这些值的公差范围从 67 到 71。直方图显示该过程的成品率仅为 34%,而 X 图显示该过程的运行不可预测。公差裕度使我们能够区分合格品和不合格品,但 34% 的良率是不可接受的。
你需要做点什么吗?
一种流行的做法是尝试通过进行适当的流程调整来提高产量。假设我们可以在选择检查(测试)的零件的每次测量结果后调整流程,并且每次调整都会影响后续生产的产品。我们将使用 67 和 71 的容差限制来确定调整的死区。也就是说,只有当我们收到不合适的测试结果时,我们才会调整流程。比如说,如果我们的测试结果为 65,那么我们会将流程向上调整 4,以使流程的平均容差值为 69,如果结果为 75,那么我们会将流程向下调整6. 但是,如果我们的测试结果是67、68、69、70或71,我们不会对此过程进行任何更改。我们将这种类型的调整进一步称为“P-控制器”。
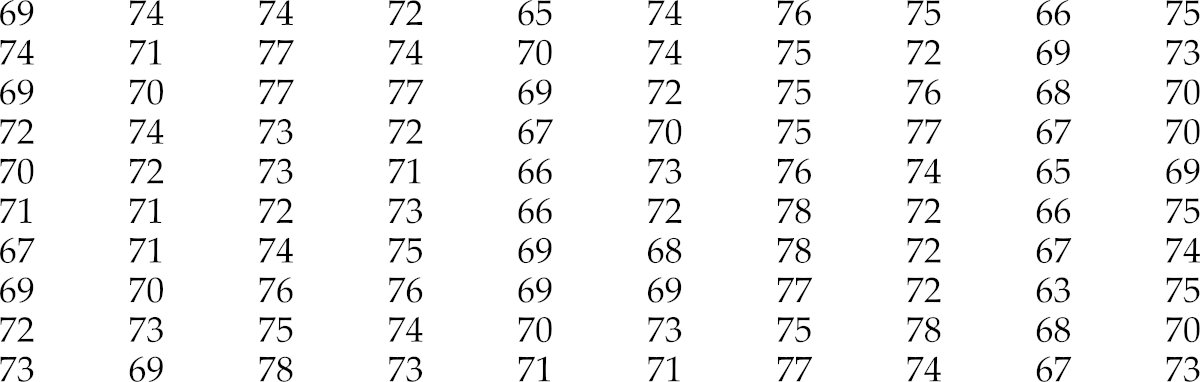
您可以下载 CSV 格式的排序列表中的数据来构建您自己的 XmR 控制图: 下载 。
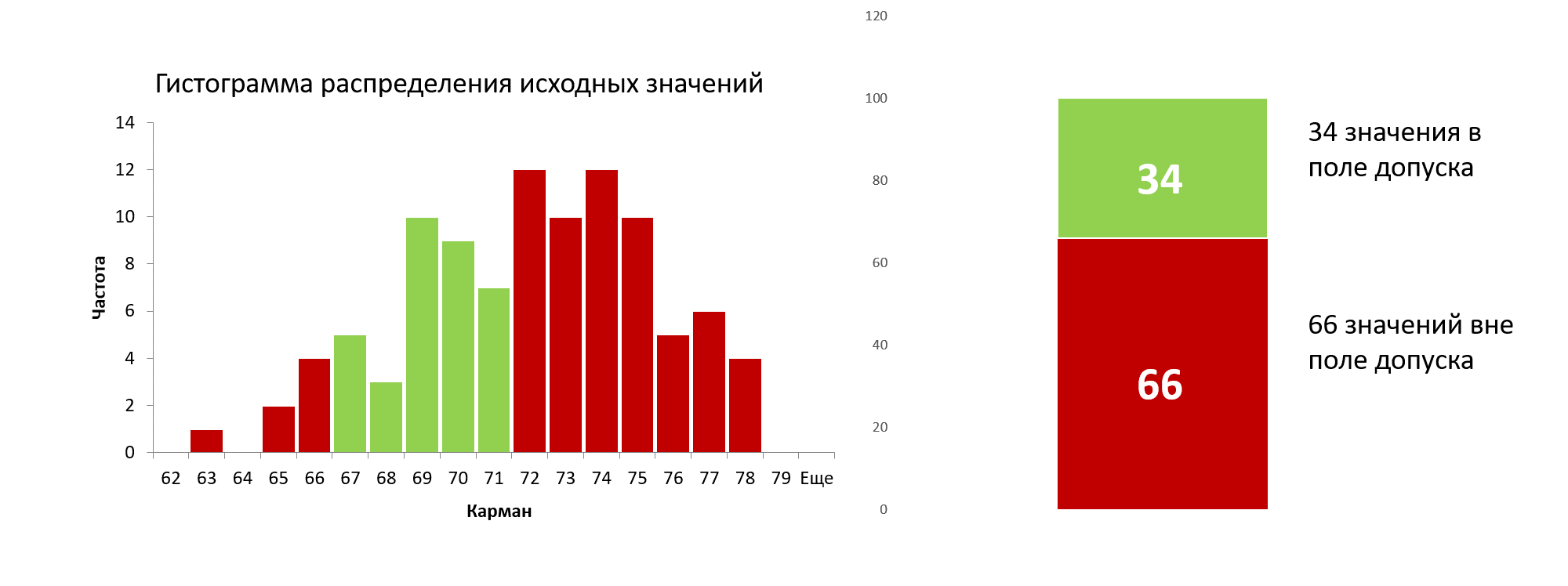
图1:调整前不稳定且中心不良的过程的100个初始值的分布直方图。
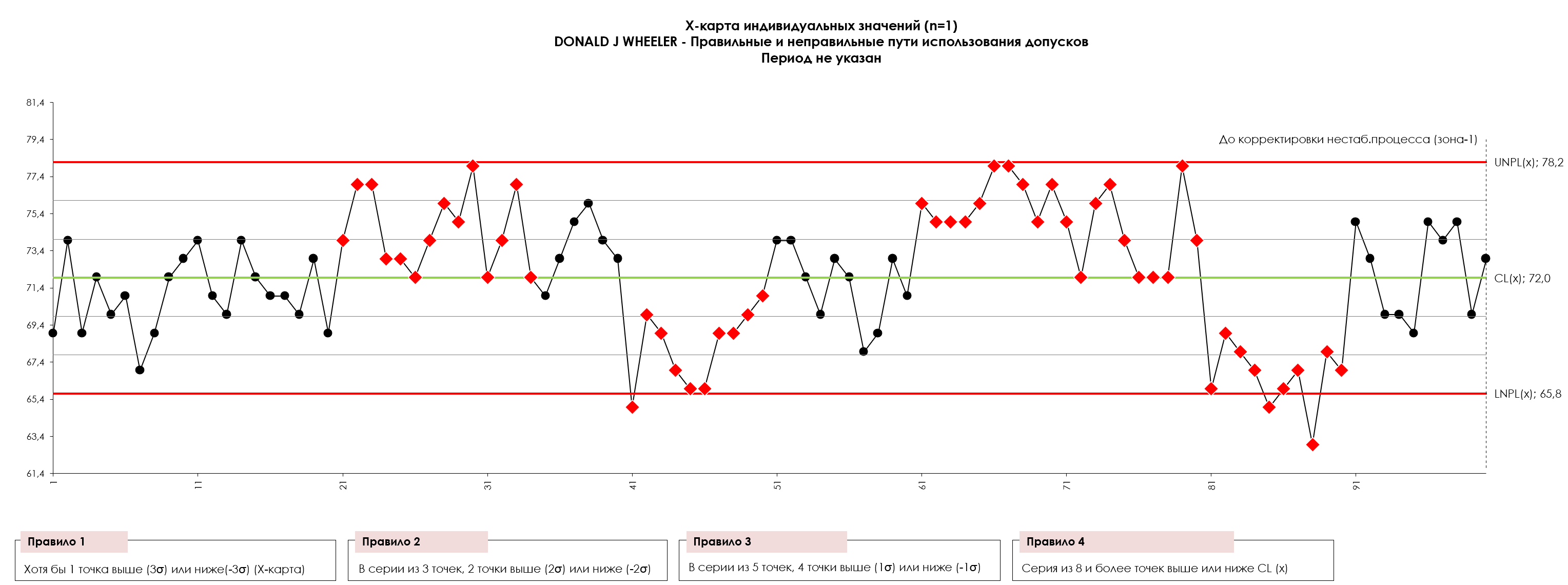
图 2:单个值(过程语音)的 X 映射 操作员校正之前不稳定且中心不良的过程的 100 个初始值。红线分别是过程的上下自然边界,绿线是过程的中心线(平均值)。红点(一系列点)是存在特殊原因的信号,表明过程处于统计上不可控的状态。该图纸是使用我们开发的 “Shewhart 控制图 PRO-Analyst +AI(适用于 Windows、Mac、Linux)” 。
下面的动画图 2 显示了调整过程如何处理图 1 中的原始数据。例如,初始值 69 不会导致后续值被调整。第二个值 74 加上对先前测量的零调整,得到调整后的值 74。这会导致过程目标 69 的 -5 调整。第三个值 69 加上先前的测量调整 - 5 给出了调整后的第三个值 64。这导致下一个过程值调整 +5,等等。
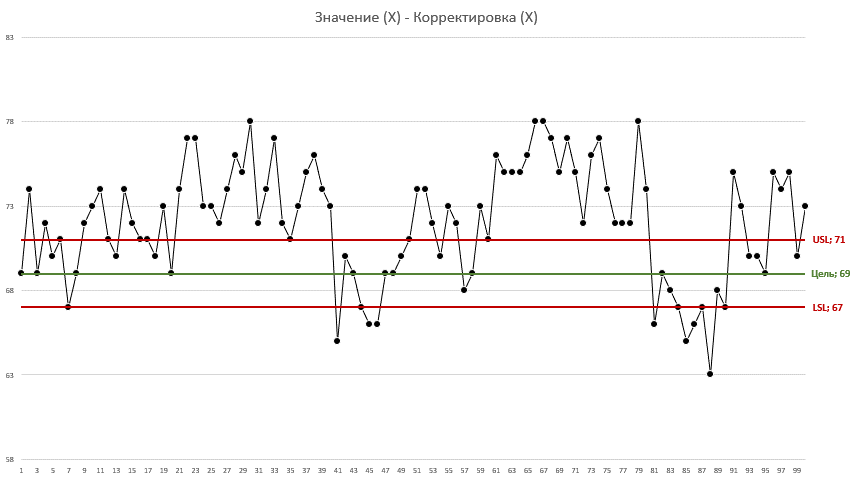
图 3:修正了不稳定且中心不良的过程时 100 个初始值变化的动画。 USL 为公差上限,Target 为公差字段标称值,LSL 为公差字段下限。
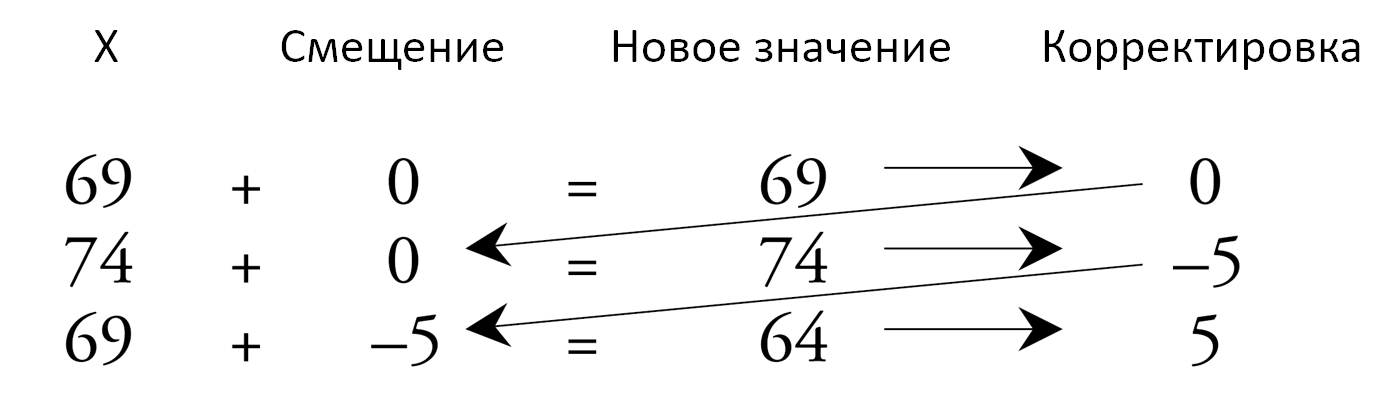
图 4:通过测量“缺陷”零件来调整流程的规则。
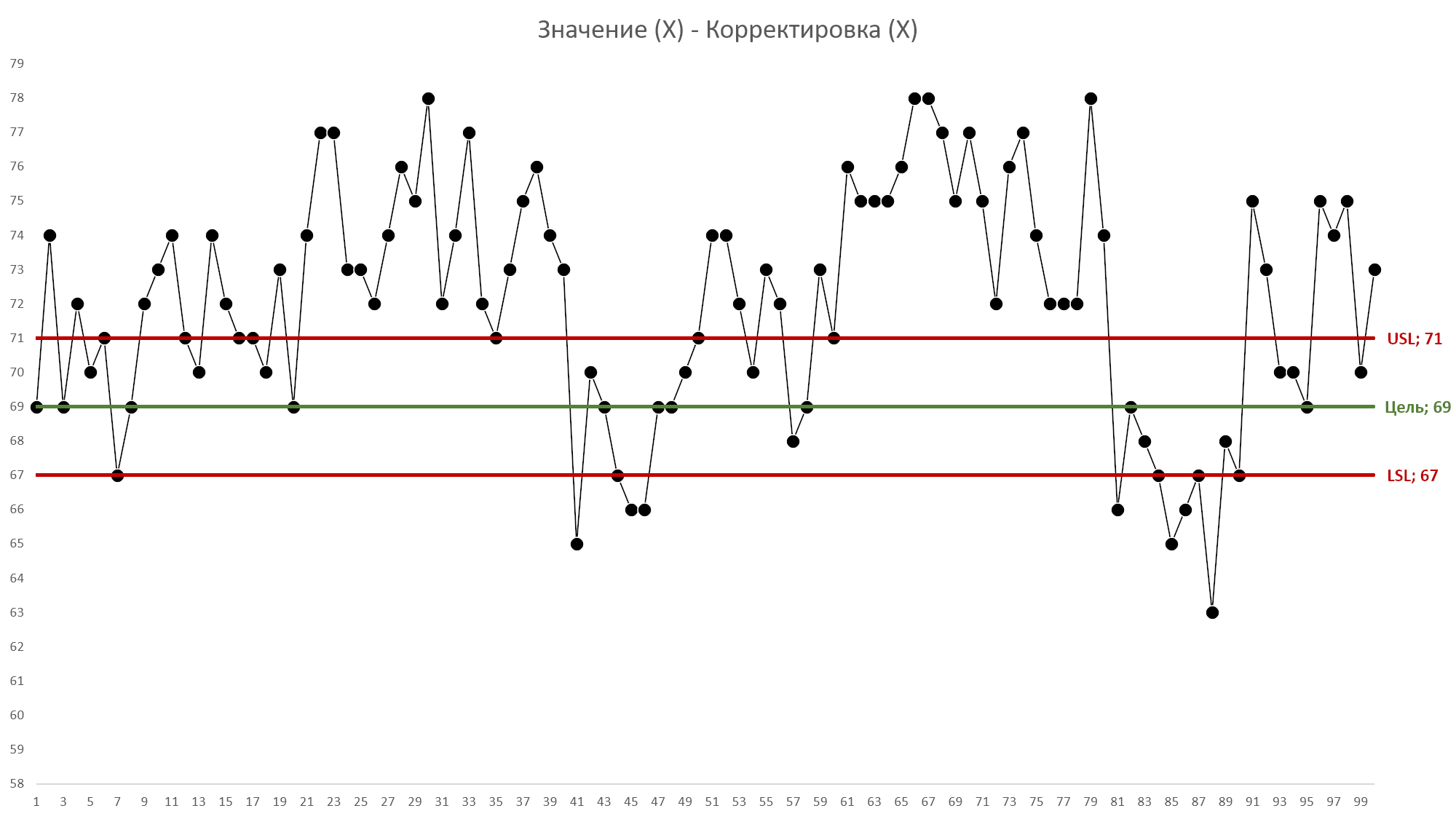
图 5:根据公差字段(客户的声音)调整不稳定且中心不良的流程之前的 100(一百)个初始值的图表。 USL 为公差上限,Target 为公差字段标称值,LSL 为公差字段下限。
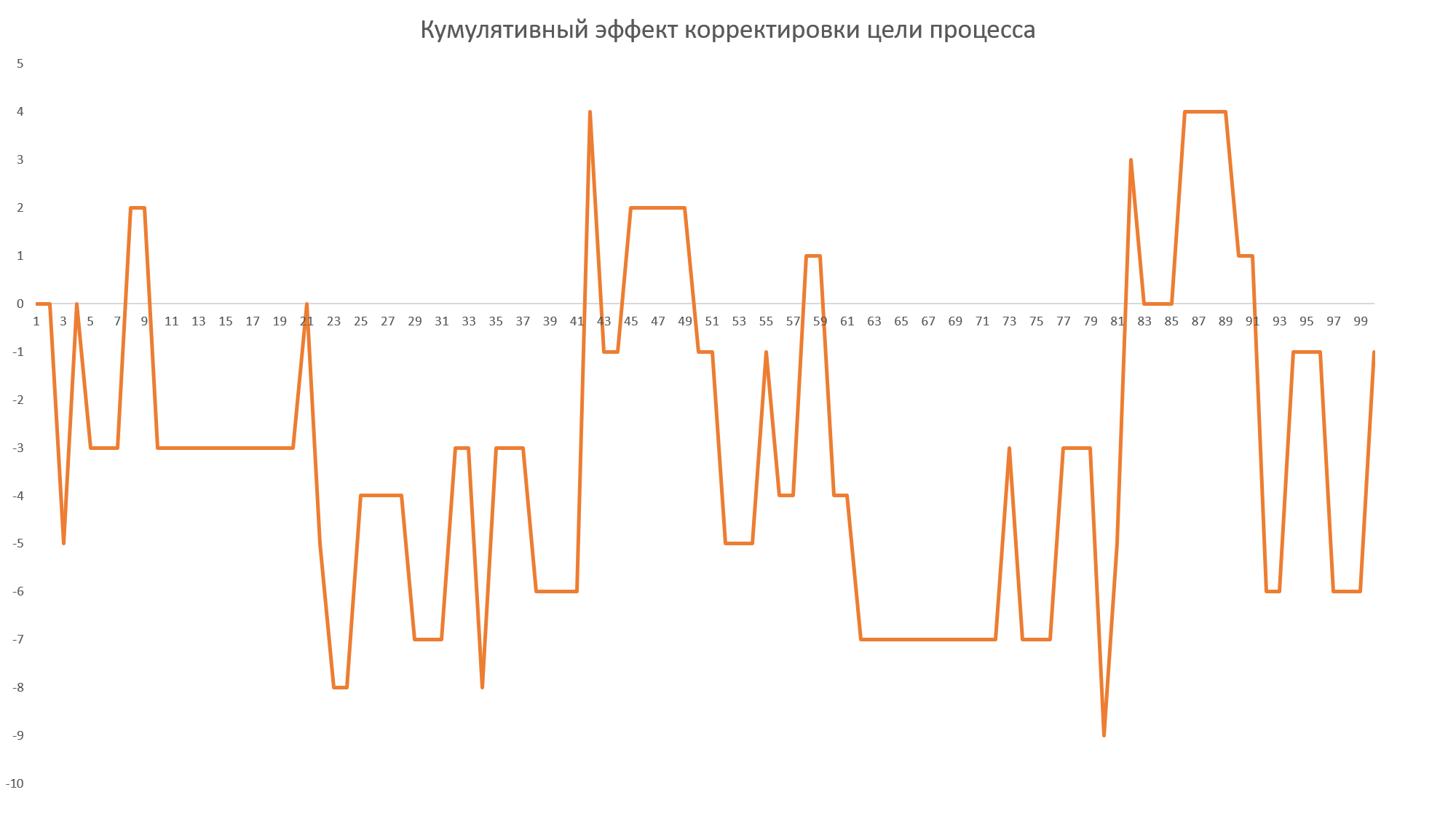
图 6:调整不受控制且中心不良的过程的累积效果。
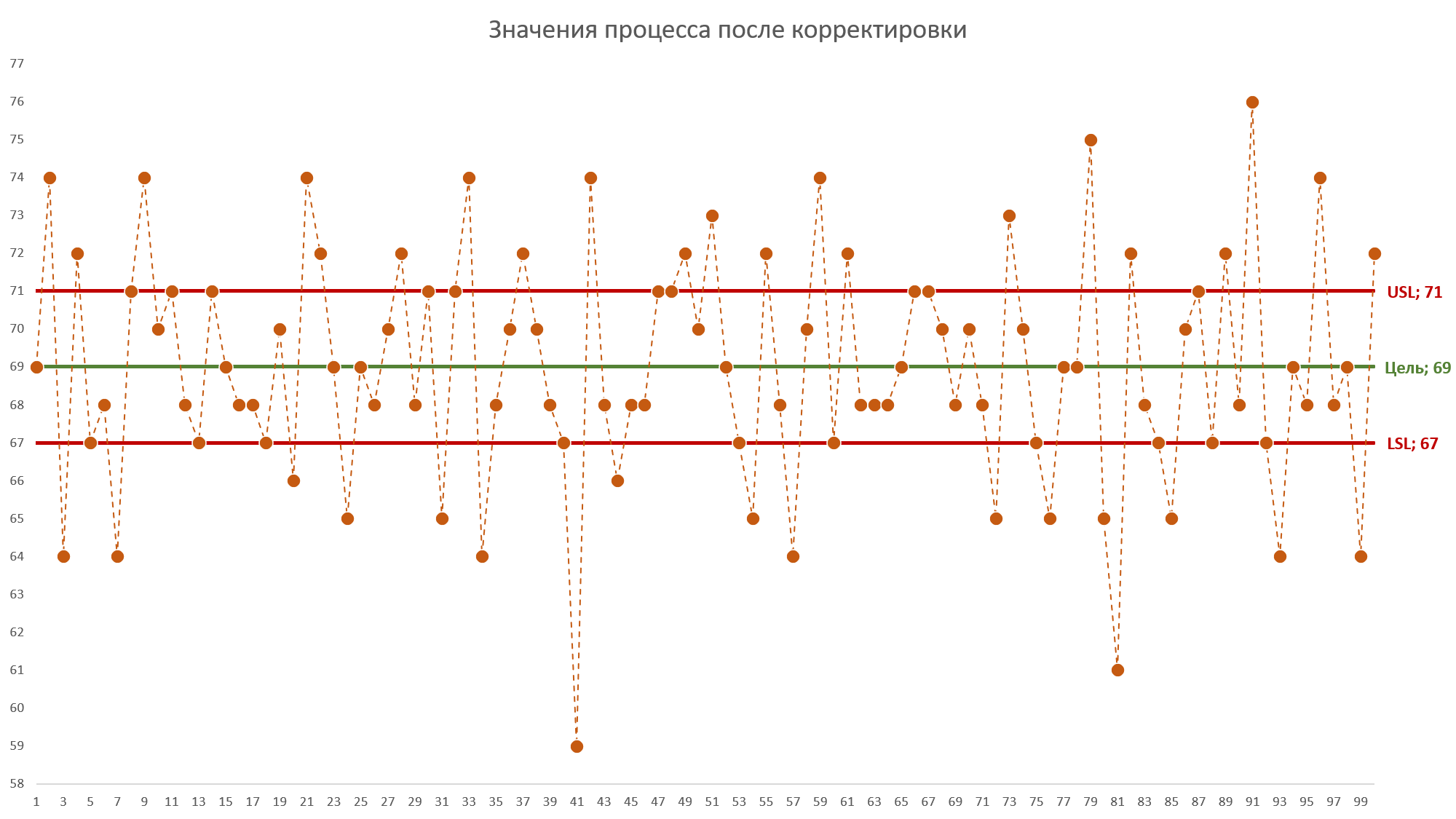
图 7:使用公差带作为死区的 P 控制器进行转换后,来自不受控制且中心不良的过程的结果数据。 USL 为公差上限,Target 为公差字段标称值,LSL 为公差字段下限。
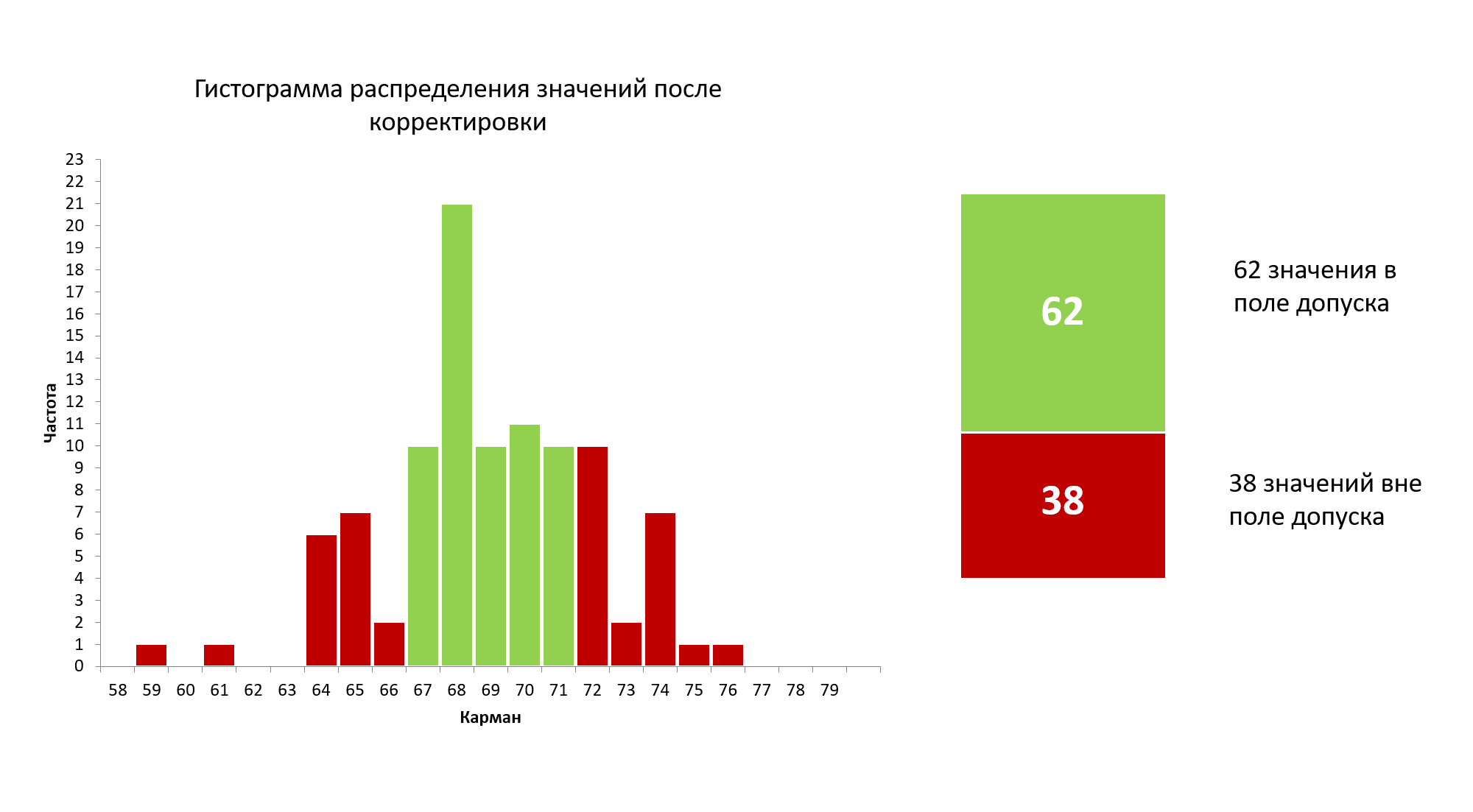
图 8:修正不稳定且中心不良的过程后 100 个新值的分布直方图。
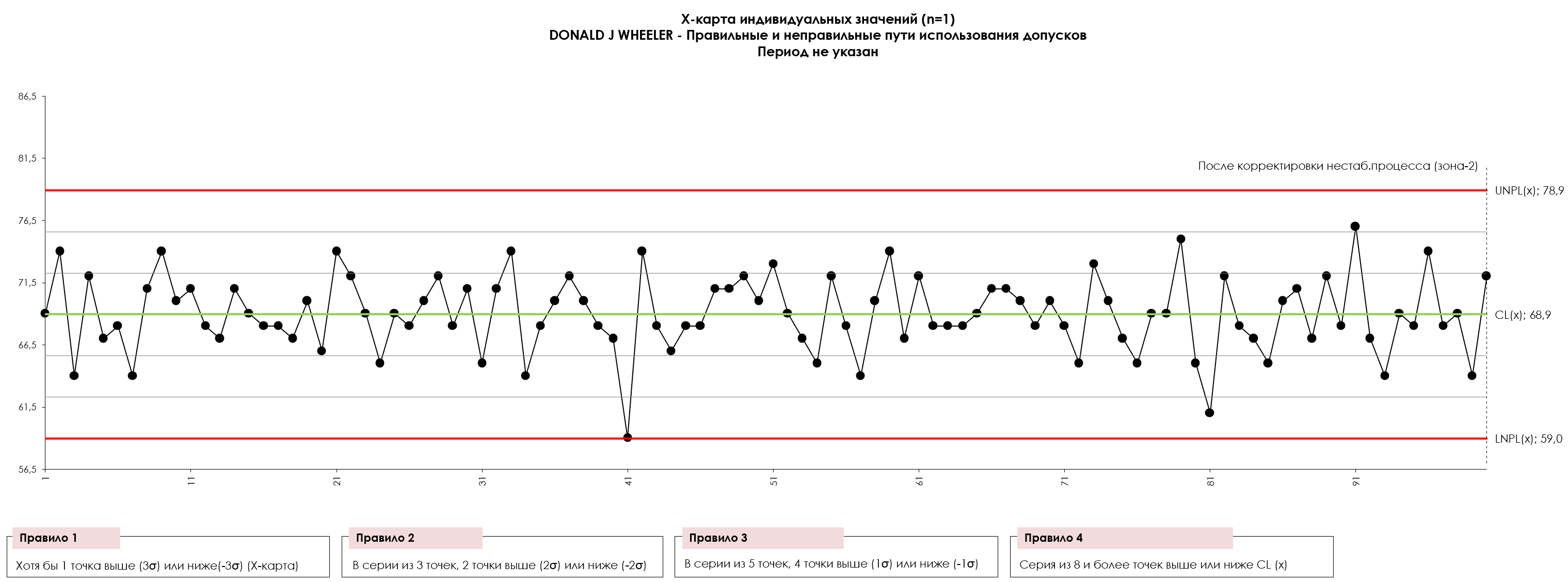
图 8.1.:对图 2 所示的不稳定和有偏差(非中心)过程进行操作员校正后的单个值(过程语音)100 个值的 X 映射,展示了统计上的稳定状态。该图纸是使用我们开发的 “Shewhart 控制图 PRO-Analyst +AI(适用于 Windows、Mac、Linux)” 。
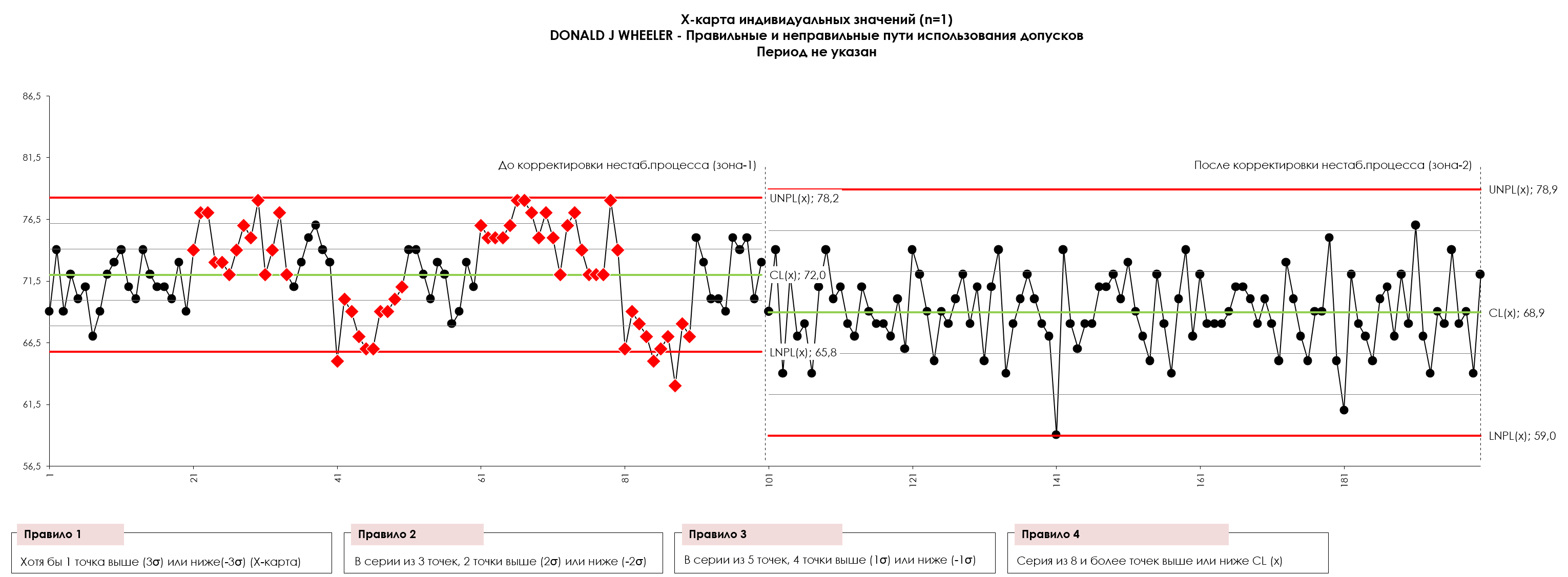
图 8.2.:不稳定和有偏差(非中心)过程校正之前(zone-1)和之后(zone-2)100 个值的单个值(过程语音)的 X 映射显示了统计上的稳定状态。该图纸是使用我们开发的 “Shewhart 控制图 PRO-Analyst +AI(适用于 Windows、Mac、Linux)” 。
那么我们是如何应对的呢? P 控制器使用公差限制来确定死区,将良率从 34% 提高到 62%。这是一个非常令人印象深刻的改进。发生这种情况是因为这个过程没有集中在公差区内并且受到不可预测的控制。由于图 2 中所示的这两个方面的数据,实际上需要改进三十二 (32) 项调整中的许多项,因此 P 控制器提高了性能。
然而,62% 的产率并不是该工艺所能达到的全部效果。本来可以更好。一旦我们确定了图 2 中所示的异常变化的特殊原因,并采取措施控制生产中的这些特殊原因,我们最终得到了图 9(下图)所示的流程。
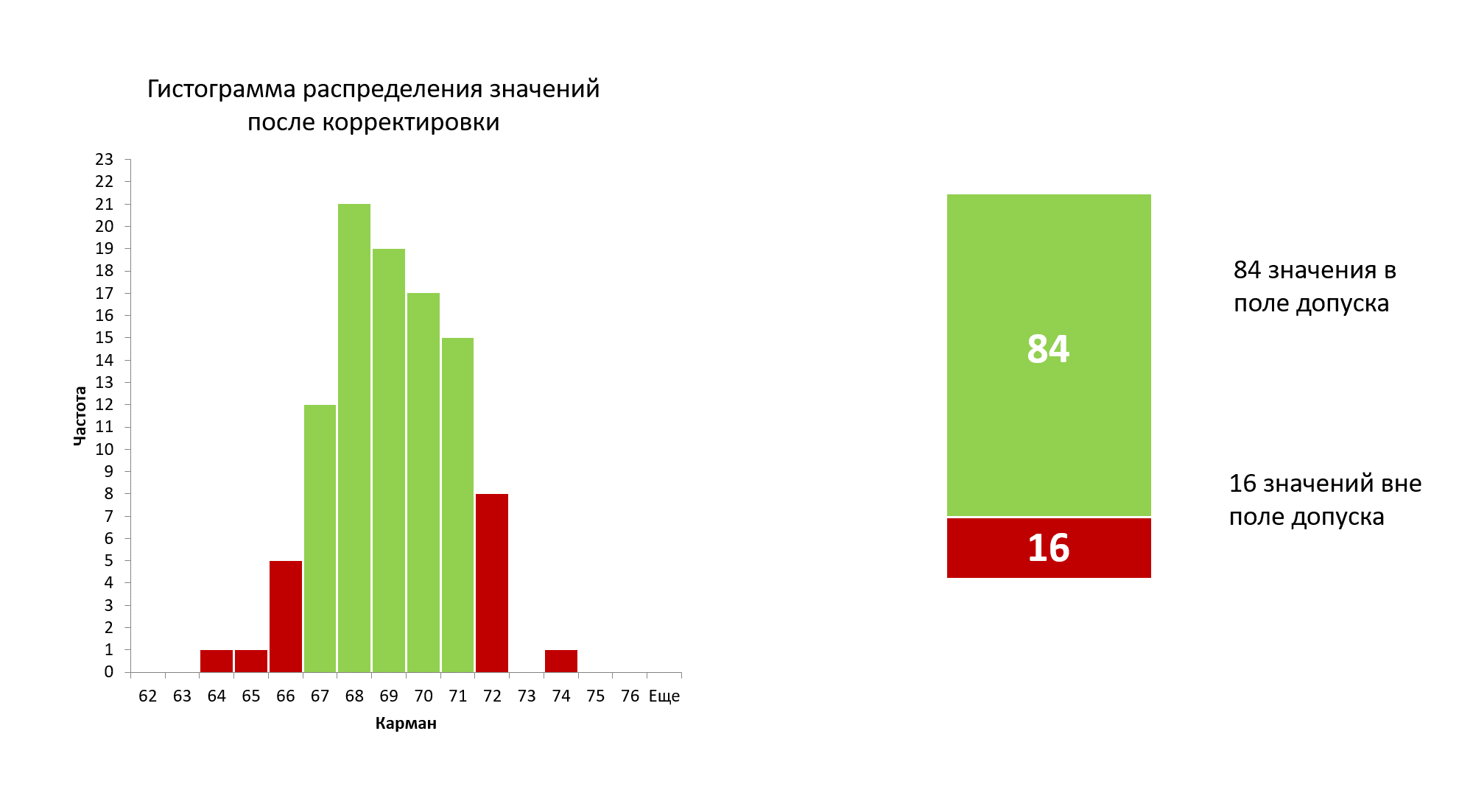
图 9:去除先前确定的特殊变异原因后 100 个新值的分布直方图。
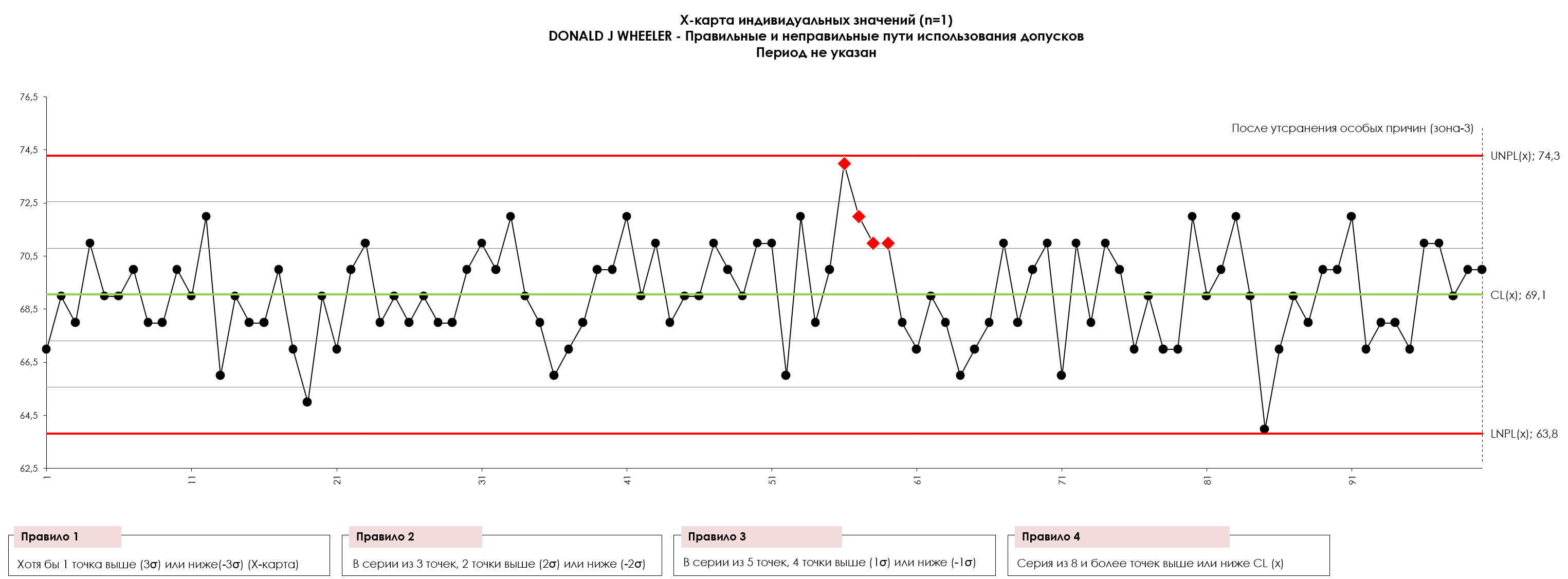
图 10:单个值(过程语音)100 个值的 X-map。图中的过程完全可以预见。先前表现出的特殊变异原因已被消除,除了一系列点55、56、57、58、59、60之外,其中可能出现了新的特殊变异原因。 UNPL 是过程的自然控制上限,LNPL 是过程的自然控制下限,CL 是中心线(平均值)。该图纸是使用我们开发的
“Shewhart 控制图 PRO-Analyst +AI(适用于 Windows、Mac、Linux)”
。
注意 Sergey P. Grigoryev:您可以以 CSV 格式下载排序列表中的稳定过程数据,以独立构建控制 XmR 图:
下载
。
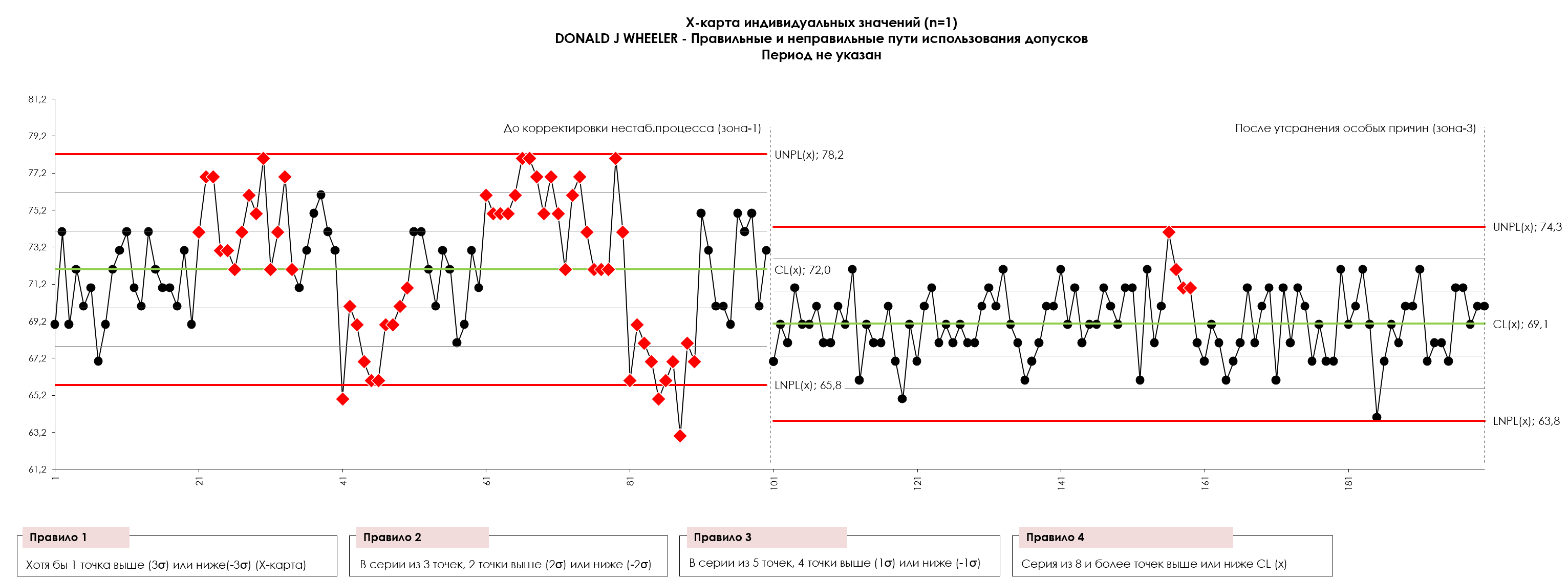
图 10.1:消除不稳定过程中变异的特殊原因之前(Zone-1)和之后(Zone-3)的 100 个值的单个值(过程声音)的 X 型图。 UNPL 是过程的自然控制上限,LNPL 是过程的自然控制下限,CL 是中心线(平均值)。该图纸是使用我们开发的 “Shewhart 控制图 PRO-Analyst +AI(适用于 Windows、Mac、Linux)” 。
当他们开始以可预测的方式管理此过程并达到其目标(公差值)时,其良率上升至 84%。这是该流程在当前状态下的全部潜力。 84% 的产率并不是什么不可能的目标,而只是该工艺在充分发挥其潜力时能够产生的结果。预测工作将最大限度地减少过程输出的变化,而针对过程目标的工作将最大限度地提高制造产品的一致性。
让我们尝试使用相同的方法来改进稳定的过程
但该流程仍然无法生产出 100% 合规的产品。难道我们就不能对这16%的不合格品做点什么吗?那么,如果我们在图 10 的数据容差字段中应用带有死区的 P 控制器会怎么样?当我们这样做时,我们最终会得到图 11 中的数据。
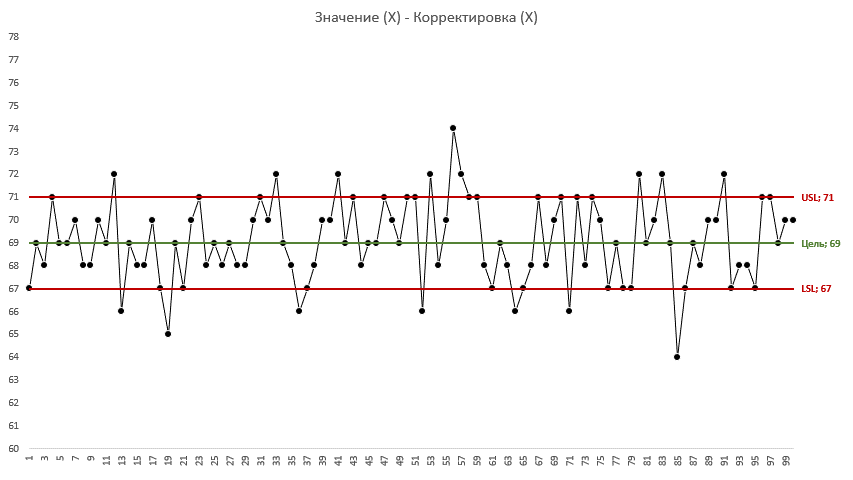
图 11:调整 100 个初始值作为稳定且中心良好的过程的动画。 USL 为公差上限,Target 为公差字段标称值,LSL 为公差字段下限。
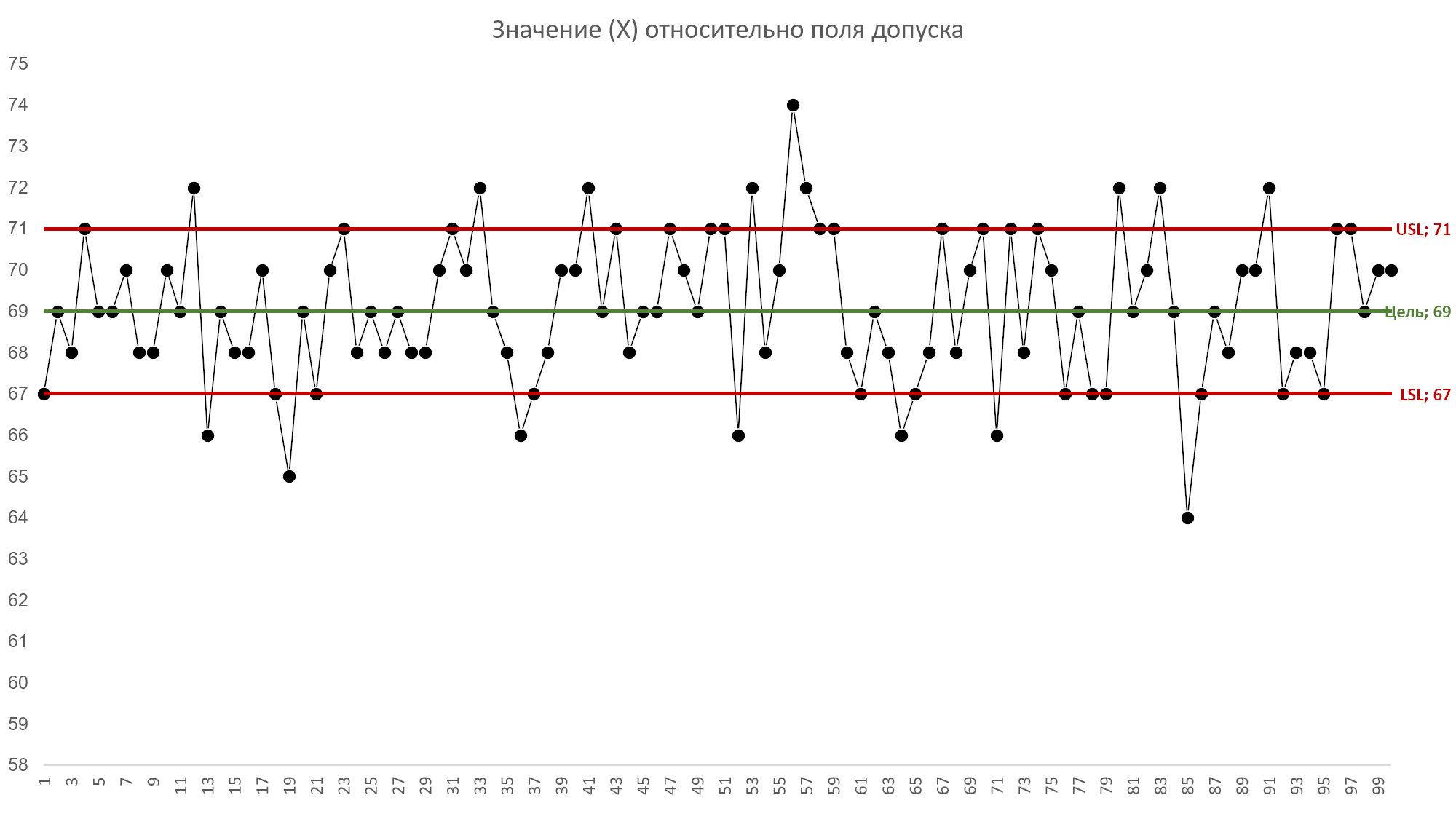
图 12:根据公差裕度(客户的声音)调整稳定且居中的流程之前的一百个初始值的图。 USL 为公差上限,Target 为公差字段标称值,LSL 为公差字段下限。
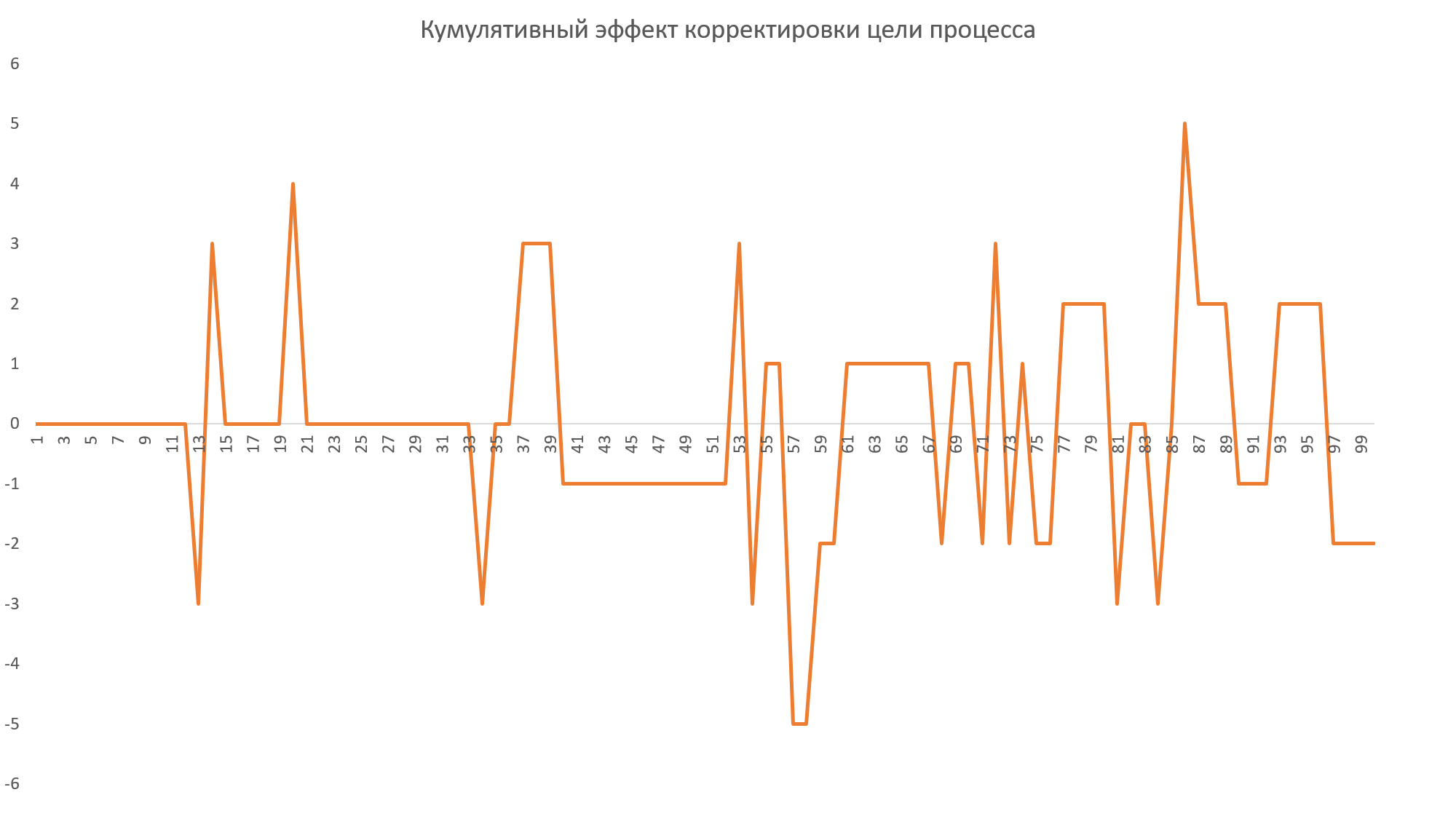
图 13:调整稳定且中心良好的过程的累积效果。
Sergey P. Grigoryev 的注释:请注意,图 13 所示的稳定且中心良好的过程的调整累积效应图与不稳定且中心良好的过程的同一图在其关于 (X) 轴的对称性方面有所不同。 (图6)。图 13 的情况表明,在尝试调整稳定且中心良好的流程时,我们只是随意将一些值向下移动,而将其他值向上移动,只会让事情变得更糟。 “我们想要最好的,但结果还是一如既往。” - V.S.切尔诺梅尔金。
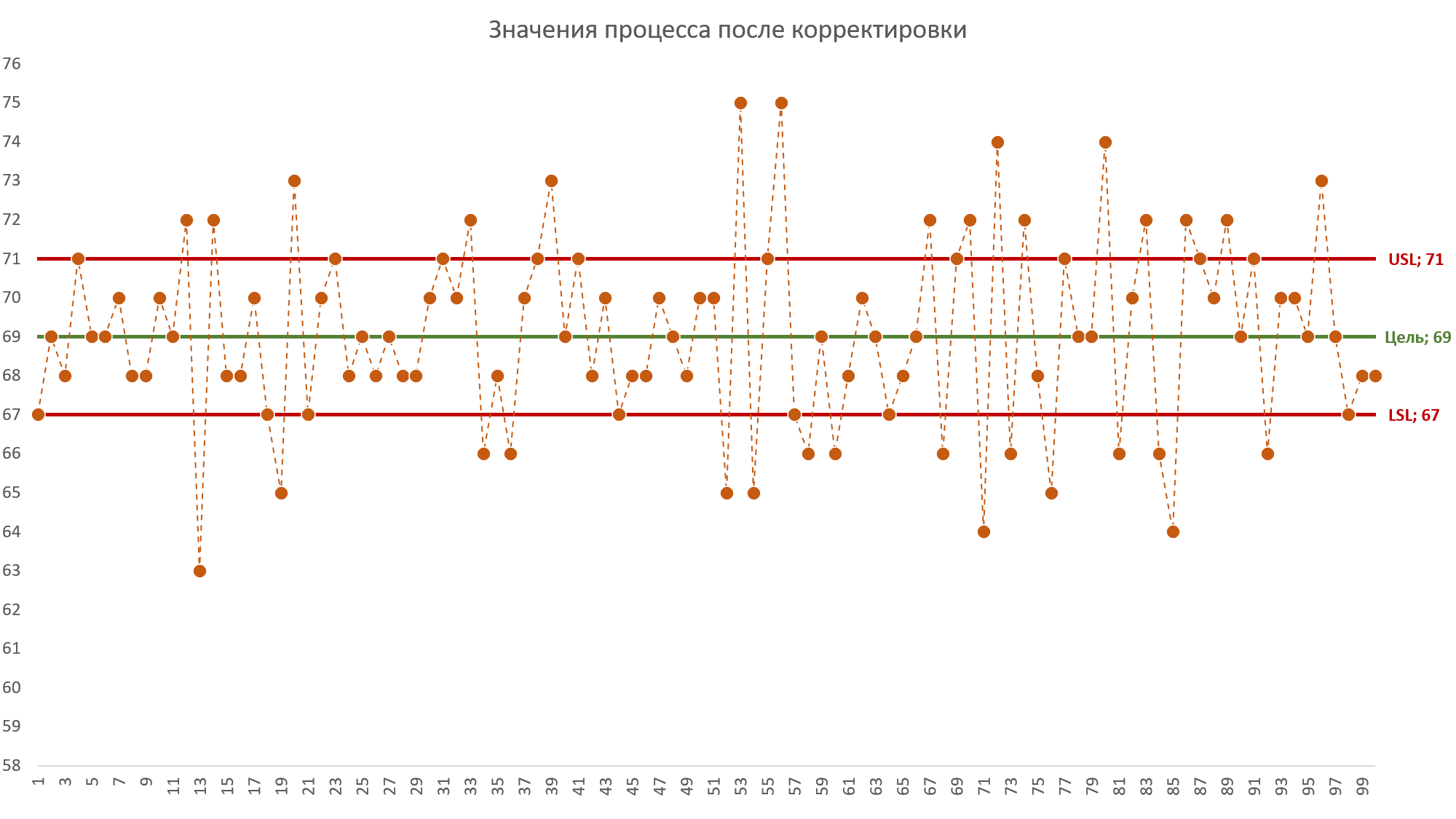
图 14:使用公差带作为死区的 P 控制器进行转换后,稳定且居中的过程产生的数据。 USL 为公差上限,Target 为公差字段标称值,LSL 为公差字段下限。
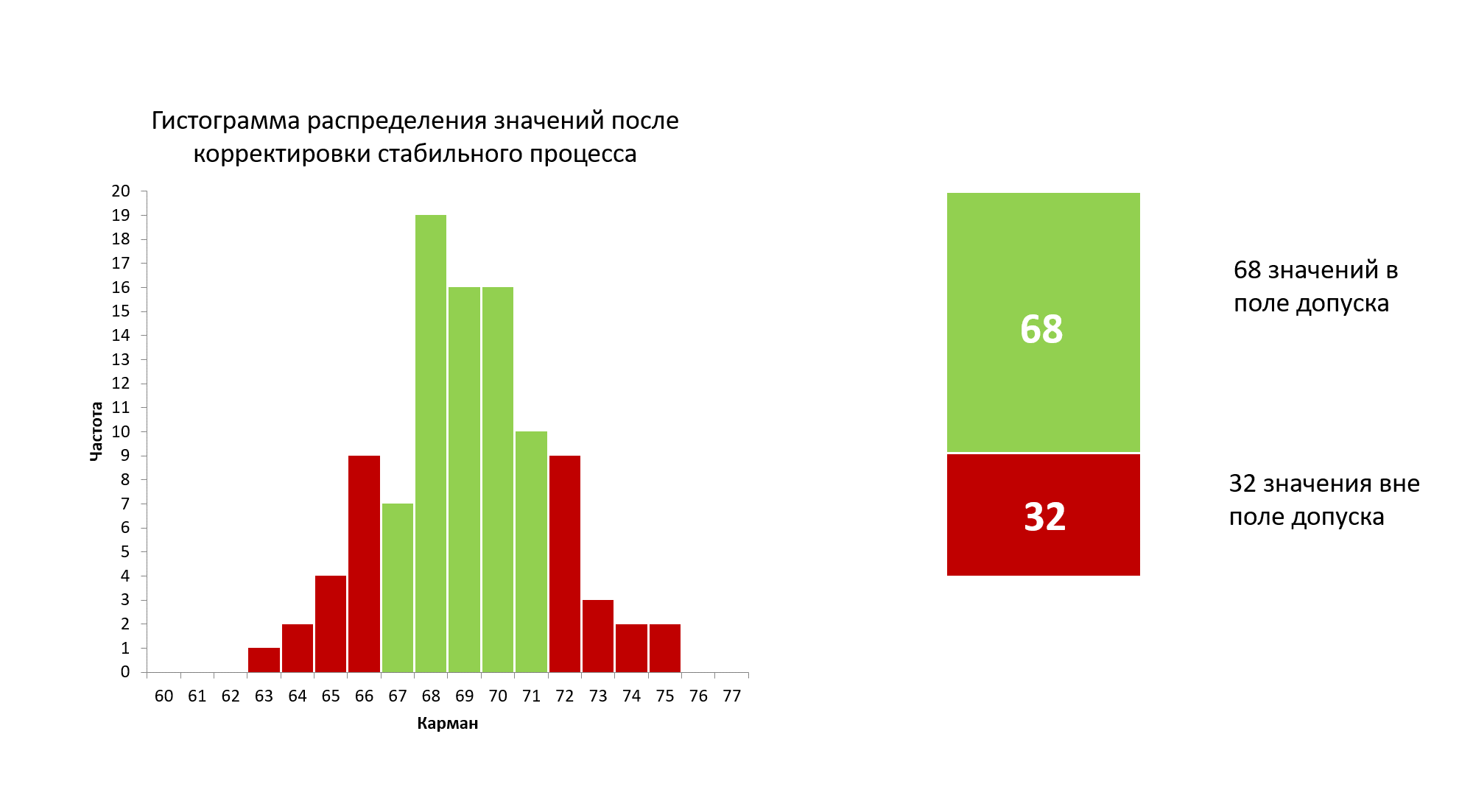
图 15:尝试调整稳定且中心良好的过程后 100 个新值的分布直方图。
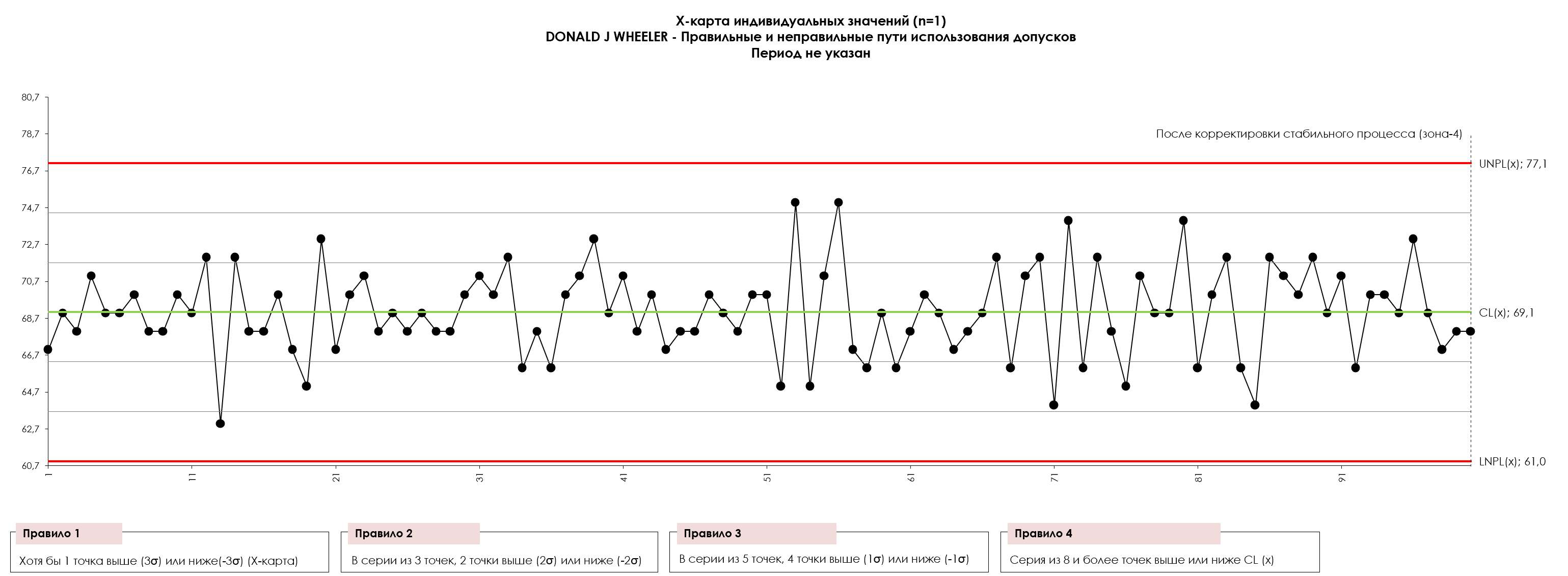
图 16. 尝试调整稳定且居中的流程后 100 个值的各个值(流程语音)的 X 型图。 UNPL 是过程的自然控制上限,LNPL 是过程的自然控制下限,CL 是中心线(平均值)。该图纸是使用我们开发的 “Shewhart 控制图 PRO-Analyst +AI(适用于 Windows、Mac、Linux)” 。
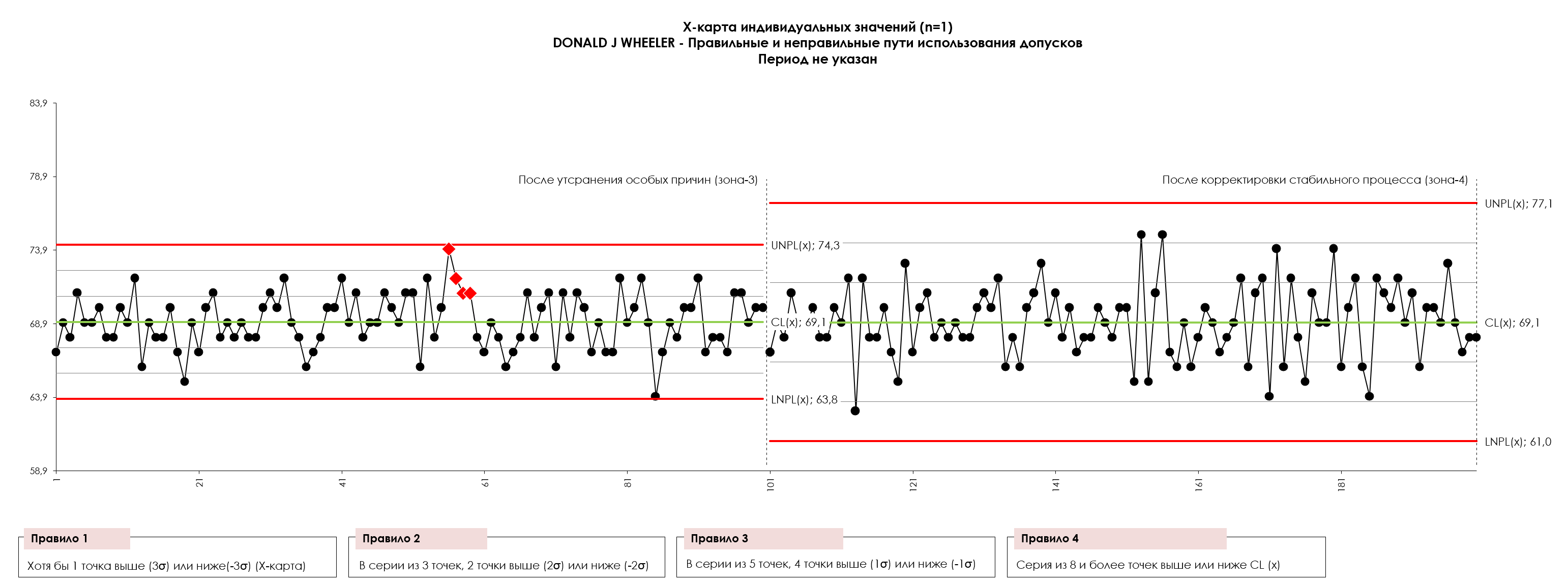
图 16.1。操作员尝试纠正稳定且居中的过程之前(Zone-3)和(Zone-4)之后的各个值(过程语音)的 X 轴图 100 个值。 UNPL 是过程的自然控制上限,LNPL 是过程的自然控制下限,CL 是中心线(平均值)。该图纸是使用我们开发的 “Shewhart 控制图 PRO-Analyst +AI(适用于 Windows、Mac、Linux)” 。
这里,P 控制器使用公差带作为死区,将一个合规性为 84% 的过程转换为另一个合规性为 68% 的过程!不合格产品的比例翻了一番,从 16% 增至 32%。
为什么会发生这种情况?这是由于 P 控制器对噪声做出反应并做出不适当的调整。在第一种情况下(图 2),只需进行一些调整,P 控制器就开始产生积极的结果,但最终不必要的调整使过程进一步偏离目标,并使情况变得更糟。
Sergey P. Grigoryev 的注释:为了改进稳定的流程,需要进行 32 项调整。采取与第一种情况相同的行动(图 2),损失的调整时间只会使情况变得更糟。这可能会让任何高技能的操作员陷入完全昏迷。您认为这种情况下运营商会怎么做?管理层会帮他解决这个问题吗?哦,如果管理层能知道这一点就好了!实验中用简单的语言解释了任何纠正中心良好且稳定的过程的尝试的结果 有漏斗和目标 爱德华·戴明。
“我们自己,会通过自己的不懈努力,毁灭一切。”
在图 2 中,该过程未集中在公差范围内,并且行为不可预测。在那里,P 控制器使用公差带作为死区,确实改善了情况。在图 14 中,这个过程是集中的并且是可预测的。 P 控制器只是在过程中增加了噪音,从而增加了产品流的变化并使情况变得更糟。
那么,我们得出了什么结论呢?我们可以使用容差来调节处于统计上不可控状态的过程吗?虽然使用将公差带作为死区的 P 控制器可能比什么都不做要好,但它不允许您充分利用过程。
当过程按可预测方式运行且位于公差范围内时,为什么 P 控制器无效?任何手动和自动过程控制机制本质上都是反应性的。无论是简单的 P 控制器还是更复杂的 PID 控制器,它们在接收到感测信号之前都无法采取行动。由于原始过程是不可预测的并且不在公差范围内,因此 P 控制器捕获了许多真实信号。然而,P控制器也响应了一些微弱的信号(噪声),导致不必要的调整。如果死区与过程声音完全不协调,你的过程调节机制就会导致调节过多。无论哪种情况,结果都会增加产品流的可变性。使用自动控制器来实现稳定的过程通常会导致比该过程在充分发挥其潜力时所能承受的变化更大的变化。
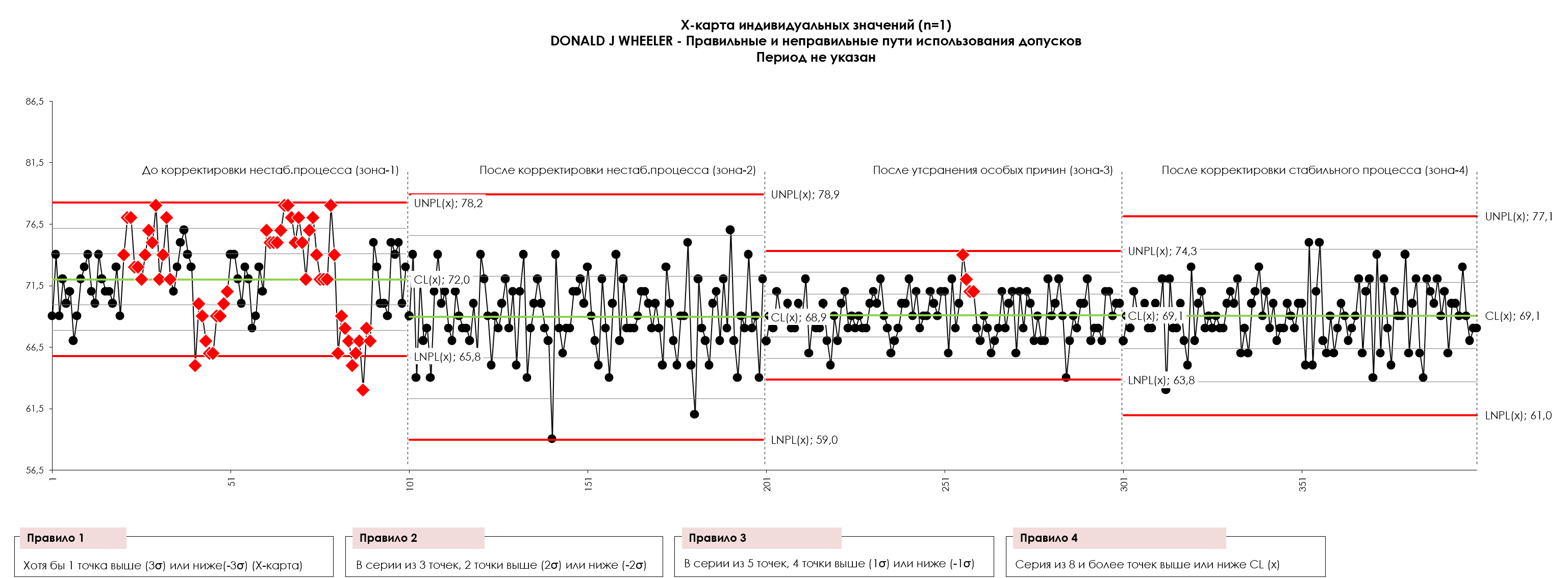
图2; 8.1; 10; 16. 单个值的 X-map(过程语音) 上面文章中讨论的所有情况的 100 个值。 UNPL 是过程的自然控制上限,LNPL 是过程的自然控制下限,CL 是中心线(平均值)。该图纸是使用我们开发的 “Shewhart 控制图 PRO-Analyst +AI(适用于 Windows、Mac、Linux)” 。
请参阅文章中生产生物甲烷的企业中操作员干预气体流量控制过程的示例: 过程控制中可变性的概念 。
第一类错误
- “但这意味着你不会对超出规范的值做出反应!”
是的,64、65、66 和 72、73、74 的不合格值是该过程在可预测地运行且在公差范围内良好居中时产生的结果的一部分。让我重复一遍。从图 9 和图 10 中可以看出,当该流程充分发挥其潜力时,将生产出 64 至 74(Y 轴)范围内的产品。一次取一个,这些值并不表示过程有任何问题,即使它们可能不符合规格。公差字段旨在从不合适的产品中筛选出合适的产品。它们是客户的声音,而不是流程。间隙字段不应与过程本身的声音相混淆。
- “你是说我应该忽略不合格产品吗?”
不合格产品必须被拒绝。但是,如果您的流程受到可预测的控制并调整为目标,那么某个项目不合规的事实并不意味着您需要进行流程调整。
Sergey P. Grigoryev 的注释:在这种情况下,进一步的改进将需要系统性的改变(原材料、技术、设备、工具、操作员培训等的改变)。
当然,如果不绘制过程行为图(单个值的 Shewhart XmR 图),则无法以可预测和集中的方式控制过程控制,因此不应涉及猜测。如果您没有流程行为图,则您运行流程的可能性至少为 10 比 1。如果是这种情况,那么自动过程控制器只能让您实现过程能力的一小部分。
简要信息
现代质量运动是关于学习如何停止烤面包。这并不意味着我们不必时不时地剥面包皮;而是意味着我们不需要时不时地剥面包皮。这意味着我们向上游进行流程工作,而不是在生产线末端将好材料与坏材料进行分类。容差字段仍然相关,它们仍然定义客户的声音,但将它们与过程的声音区分开来很重要。虽然我们确实希望流程的声音与公差字段(客户的声音)保持一致,但公差字段并未提供有关需要做什么才能充分发挥流程潜力的正确信息。
另一个简单的案例(Sergey P. Grigoryev)
我确信,当过程处于统计稳定(受控)状态但未集中在公差范围内时,有必要考虑另一种情况。在此类过程的一个示例中,有 77 个值超出了公差范围。
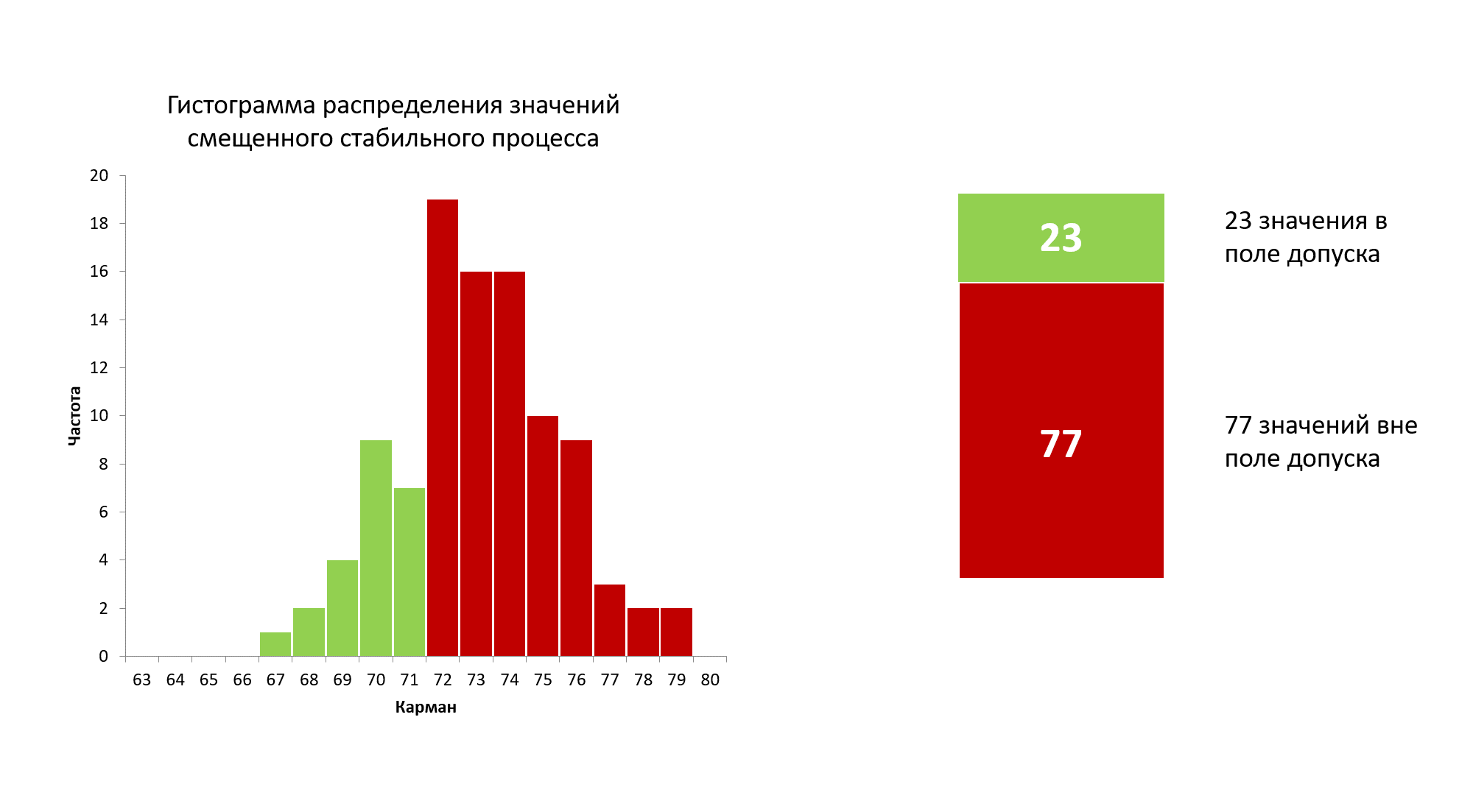
图 17:稳定但中心不良过程的 100 个初始值的分布直方图。
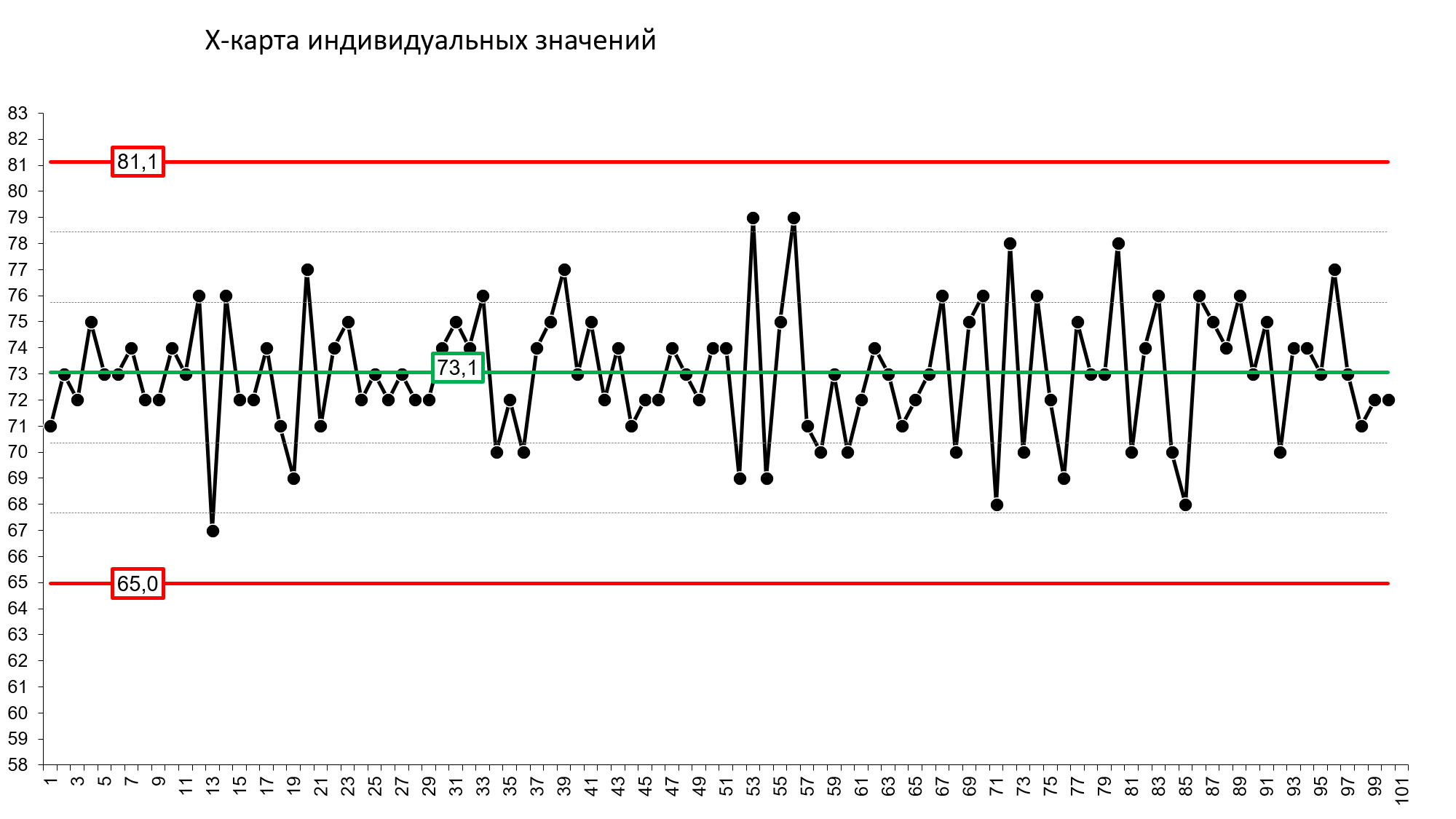
图 18. 稳定但中心不良的过程的 100 个初始值的各个值(过程声音)的 X 映射。红线分别是过程的上下自然边界,绿线是过程的中心线(平均值)。
在这种情况下,只需进行一次调整即可将过程集中在公差范围内。只需更改一次机器设置即可从公差带中心偏移平均稳定过程。
因此,如果稳定且中心不良的过程的平均值为 73.1,公差域的中心为 69。稳定且中心不良的过程的位移: 69.0-73.1 = -4.1
生产这些零件的机器的设置必须根据位移量进行更改。并致电技术服务人员,他们应该设置机器。请参阅下面的结果。
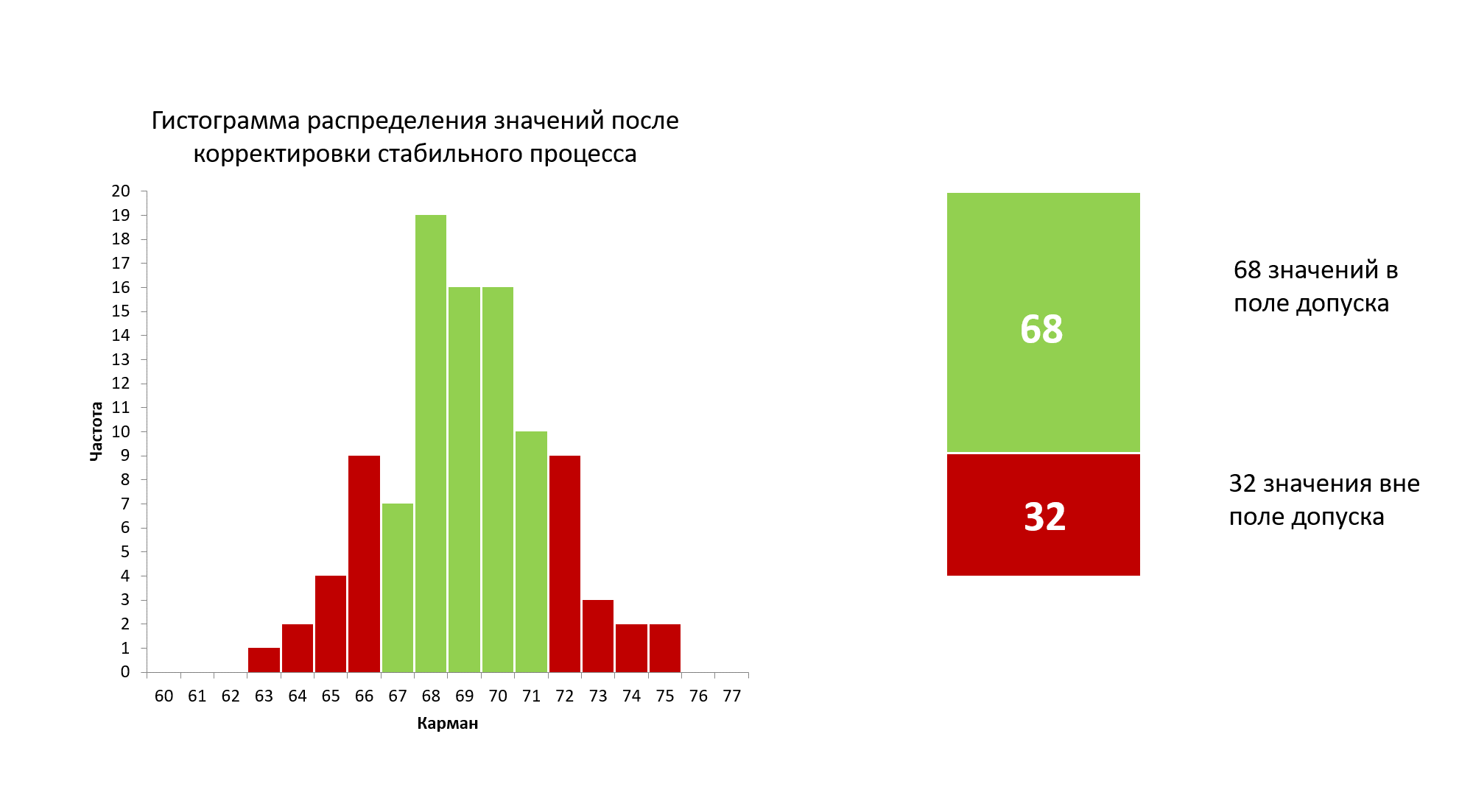
图 19:以稳定过程的公差范围为中心后 100 个新值的分布直方图。
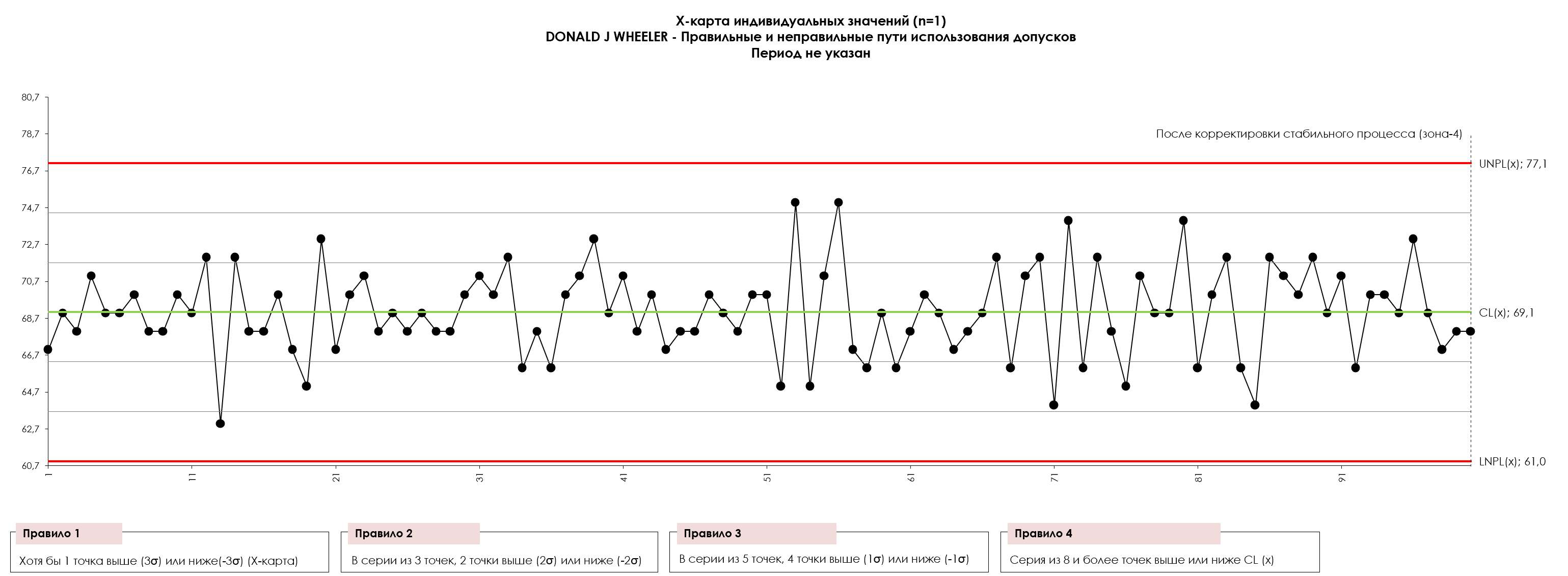
图 20. 各个值(过程语音)的 X 型图 集中在稳定过程公差字段后的 100 个新值。红线分别是过程的上下自然边界,绿线是过程的中心线(平均值)。该图纸是使用我们开发的 “Shewhart 控制图 PRO-Analyst +AI(适用于 Windows、Mac、Linux)” 。
如果您认为后一种情况很少发生,那您就大错特错了。如果您不保留流程的控制图并构建指标相对于公差字段的分布直方图,您甚至无法判断这一点。如果您熟悉过程性能(再现性)指数Cp(生存空间指数)和Cpk(过程中心指数),那么您应该知道,绝大多数情况下Cpk小于Cp,这表明平均值发生了变化从公差范围的中心向公差下限或上限进行的过程。无论如何,将稳定和任何不稳定的工艺都集中在公差区域内,可以减少“一键”超出公差限制的有缺陷工艺零件的比例。如果过程在公差带内运行,定心可显着提高零件和装配体 (DSE) 的质量,使大多数零件更接近公差带的中心(对于对称公差带)。最后一条语句解释了 田口损失函数 。
通过一次调整,流程改进从 77 个有缺陷的零件到 32 个。
“你觉得怎么样,埃隆·马斯克?”
重要的!
- 显着提高质量的唯一经济可行的方法是首先使过程进入统计控制状态,然后才开始将其集中在公差区域内。
- 在进行任何流程研究之前,请确保您的 测量系统 操作者对工艺过程进行调整时使用的,处于统计受控状态,不存在显着偏差,查明其精度是否足以评估过程,均匀测量是否足够(测量深度)或者,相反,您是否正在录制噪音。 - 请参阅我们软件的说明 休哈特控制图 。
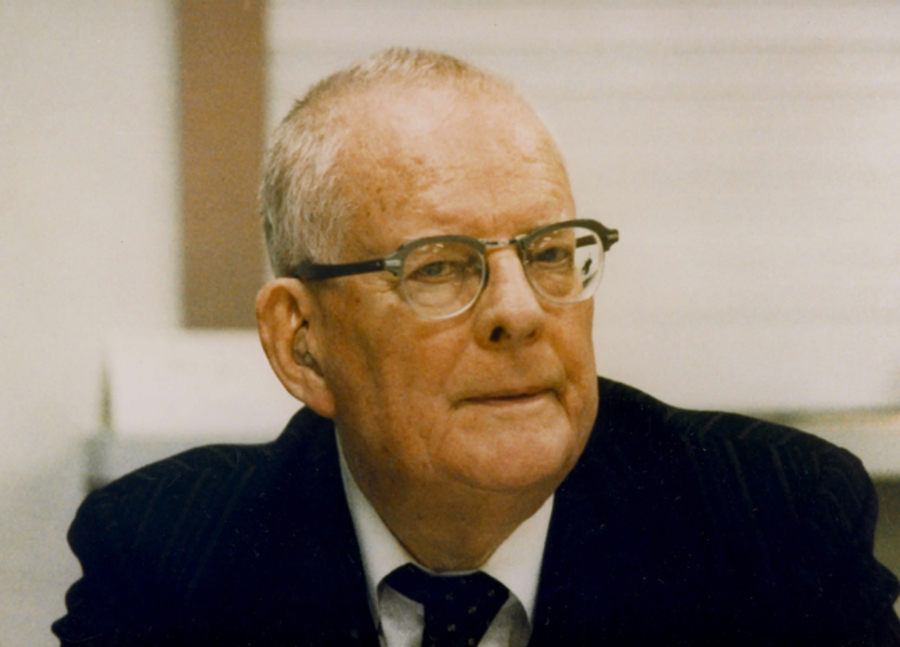
“知识是无可替代的。但使用知识的前景令人恐惧。”